La Industria 4.0 está remodelando la eficiencia de la producción y cambiar la cara de la fabricación. Es un mundo donde las máquinas se comunican, los datos impulsan las decisiones y los procesos de producción se optimizan en tiempo real. En este blog, exploramos cómo esta revolución tecnológica mejora la eficiencia, la calidad y el mantenimiento predictivo en la fabricación. Los casos del mundo real demuestran su poder transformador. Únase a nosotros en este viaje hacia el futuro de la industria.
Bienvenido al futuro de la fabricación. Industria 4.0, la cuarta revolución industrial, está aquí para remodelar la forma en que producimos bienes. En este blog, profundizaremos en el increíble impacto de la Industria 4.0, donde las máquinas se comunican, los datos impulsan las decisiones y la producción se vuelve más inteligente y eficiente. Descubra cómo está cambiando las reglas del juego para los fabricantes y allanando el camino para una nueva era de la industria.
¿Cómo la Industria 4.0 está remodelando la eficiencia de la producción?
Categorizado como Internet de las cosas (IoT), implica una intrincada red de sistemas inteligentes y computadoras conectadas que intercambian y acumulan datos. El término “cosa” abarca cualquier Objeto tangible o dispositivo capaz de transmitir datos.. Pero, ¿cuál es la aplicación de la Industria 4.0 en las plantas de fabricación, donde está remodelando la eficiencia de la producción?
Las tecnologías de transporte, que funcionan según principios similares, son parte integral de esta transformación. El Internet industrial de las cosas (IIoT) se diferencia porque se centra en diversos flujos de datos, como los sensores de las máquinas. Estos sensores tienen la capacidad de monitorear varios parámetros, desde temperatura hasta niveles de fluidos, e interactuar con una variedad de plataformas de software avanzadas.
IIoT explicado: cómo los sensores revolucionan la fabricación
Robert Schmid, tecnólogo jefe de IoT de Deloitte Digital, lo aclara, ”En la tecnología IIoT, los sensores se fijan a activos físicos, recopilan datos, los almacenan de forma inalámbrica y utilizar análisis y aprendizaje automático para desencadenar acciones de respuesta.” Esto se aplica a una amplia gama de activos físicos, incluidos sistemas avanzados como el sistema de cinta transportadora.
Notablemente, probablemente te encuentres con IoT en la vida cotidiana, a veces sin conciencia. Los dispositivos cotidianos, como los relojes inteligentes con seguimiento del estado físico y los termostatos domésticos automatizados, aprovechan la funcionalidad de IoT y se adaptan a su actividad y preferencias. IIoT ha reforzado significativamente la fabricación, con un aumento de ingresos promedio de 28,51 TP3T, según TATA Consultancy Services, logrado mediante la aplicación experta de datos y análisis en el momento adecuado.
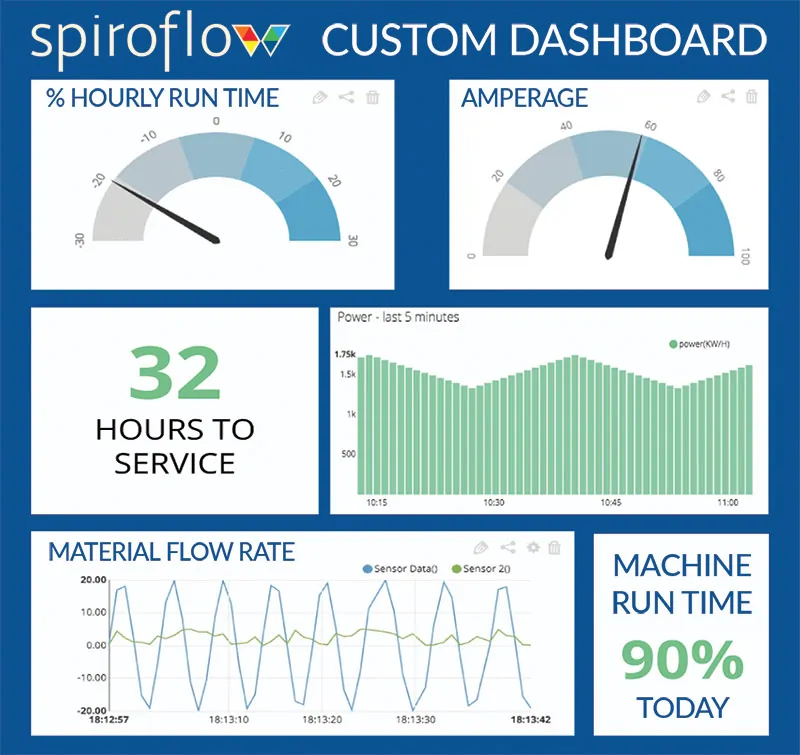
Transformando la fabricación con datos en tiempo real y mantenimiento predictivo
Los equipos de fabricación, incluidos los sistemas avanzados de cintas transportadoras, también pueden equiparse con sensores que recopilan datos de las máquinas y los reportan en tiempo real y en un formato de fácil acceso. Con IIoT, experimentará Toma de decisiones más rápida y mejor informada. desbloqueando datos críticos sobre el rendimiento del equipo y entregándolos a las manos adecuadas precisamente cuando es más relevante.
Anteriormente, cuando un sistema fallaba, podía provocar costosos tiempos de inactividad no planificados e inspecciones de rutina, lo que resultaba en un cambio de piezas de repuesto. Ahora, al utilizar IIoT, los sensores informan continuamente datos a las personas adecuadas y les notifican antes de una falla crítica.
Y con informes que sugieren que el 40% de las organizaciones no utiliza ningún tipo de mantenimiento predictivo, las interrupciones no planificadas podrían reducirse hasta en el 50% con dispositivos IIoT. El mantenimiento es cada vez menos reactivo y más proactivo, con datos tanto históricos como en tiempo real disponibles.
Seguimiento e informes habilitados para una resolución de problemas más rápida
Al seleccionar los problemas que desean resolver, los fabricantes pueden rastrear e informar sobre los datos que más necesitan, incluidos datos críticos de sistemas de transporte industriales, y tomar medidas inmediatas. Esto se puede lograr con el uso de informes, como gráficos, enviados a un panel accesible desde una PC, computadora portátil, dispositivo móvil, tableta e incluso dispositivos inteligentes portátiles como relojes.
A menudo, en la fabricación, si no se toman las medidas correctas en el momento adecuado, puede ser perjudicial para la producción y dar lugar a una pérdida desproporcionada de beneficios con respecto al mantenimiento planificado. Con 82% de fallas de activos que ocurren aleatoriamente, monitoreo remoto Puede indicar cómo y cuándo ocurrió la falla..
Lo bueno es que puede permitir a las partes operativas aprender del evento y predecir eventos futuros con más precisión. Esto, a su vez, permite reacciones más rápidas a los problemas y reduce los problemas potenciales al obtener visibilidad crítica de los datos que ya tiene.
Para ganar visibilidad en varios sitios de fabricación diferentes en todo el mundo, un fabricante global está implementando uno de esos sistemas IIoT para aumentar la eficiencia de producción, como se demuestra en el Caso A a continuación.
Caso A: SAM y monitoreo remoto
Un fabricante global de productos para el cuidado de la salud tiene múltiples sitios en varios continentes. Para ganar visibilidad sobre el rendimiento de cada línea de producción, el fabricante está actualizando a un sistema de monitoreo remoto conocido como SAM de los especialistas en transporte y manipulación de supersacos, Spiroflow, para que puedan realizar un seguimiento de los datos de cada planta.
Utilizando un panel personalizado, las personas clave podrán monitorear remotamente los datos desde cualquier parte del mundo y comparar el rendimiento de cada proceso de fabricación con el del otro. Esto permitirá una racionalización global de sus costos de fabricación a medida que se puedan identificar los cuellos de botella y mejorar la eficiencia general.
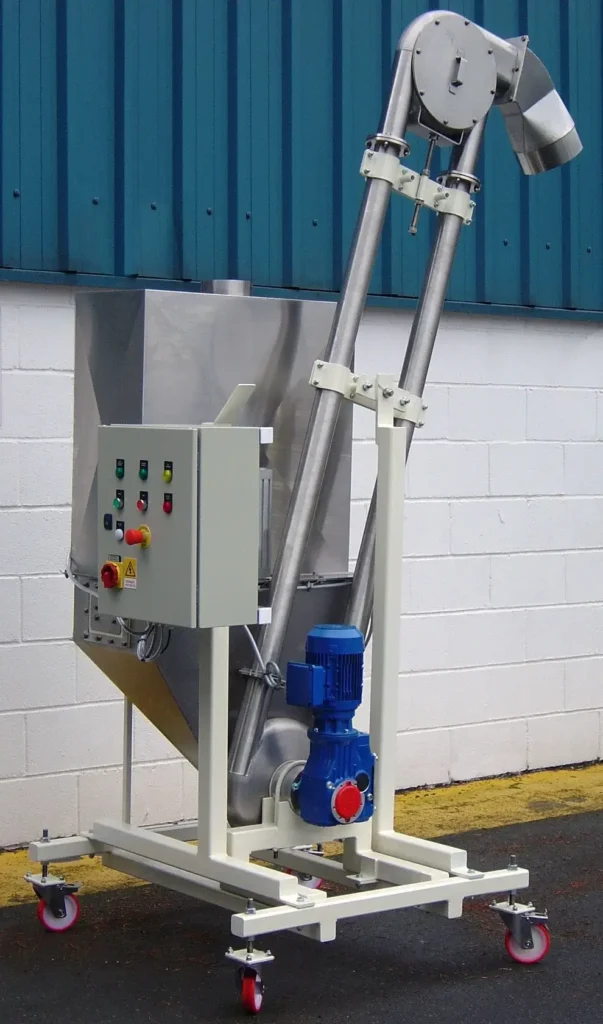
Optimización de la producción mediante estrategias de mantenimiento predictivo
Otra mejora importante se puede lograr en la reducción del tiempo de inactividad con un mantenimiento planificado y previsto. Todos los fabricantes son conscientes de que la clave para obtener grandes beneficios es producción precisa, de alta calidad y confiable. Si una máquina deja de funcionar en medio de un turno y no hay repuestos críticos en el sitio, esto puede resultar en costosos retrasos.
Adoptar la Industria 4.0 abre la puerta a recopilar y analizar datos de sus máquinas y desarrollar un programa de mantenimiento predictivo, incluido el monitoreo de soluciones de cintas transportadoras. Este enfoque no sólo mejora la eficiencia de la producción sino también identifica posibles obstáculos en sus procesos.
Anteriormente, cuando un sistema fallaba, podía provocar costosos tiempos de inactividad no planificados e inspecciones de rutina, lo que provocaba un cambio de piezas de repuesto. Al utilizar SAM, Los sensores informan continuamente datos a las personas adecuadas. y les notificará antes de una falla crítica. Esto, a su vez, permite que el sistema aprenda y se adapte continuamente a su entorno de proceso específico. Los fabricantes que trabajan para lograr cero tiempos de inactividad no planificados pueden beneficiarse de información inteligente que mejorará la eficiencia y reducirá los costos.
Mantenimiento justo a tiempo: minimizar el tiempo de inactividad y maximizar la eficiencia
Como se mencionó anteriormente, no tomar las medidas correctas en el momento adecuado puede ser perjudicial para la producción y provocar una pérdida de beneficios. Las soluciones de transporte SAM de Spiroflow, en este caso, indicar cómo y cuándo ocurrió la falla y aprenderá de este evento, lo que le permitirá predecir eventos futuros con mayor precisión.
Además, al conocer el momento óptimo para reemplazar las piezas desgastables, la producción puede avanzar hacia el mantenimiento justo a tiempo (JIT). Él Permite mantener la cantidad correcta de stock de repuesto., asegurando que no haya exceso de existencias pero teniendo el repuesto correcto para el mantenimiento predictivo. Esto, a su vez, permite reacciones más rápidas a los problemas y reduce los problemas potenciales al obtener visibilidad crítica de los datos que ya tiene, como en el Caso B, que ocurrió con un fabricante de productos químicos.
Caso B: Prevención de averías costosas y ahorro con la Industria 4.0
Un importante fabricante de productos químicos sufrió una avería un sábado por la tarde durante el turno de noche. El El rodamiento de un motor había fallado.. El director de mantenimiento de la planta estimó que el coste de la avería fue de alrededor de $12.300 (£10.000) por hora, y como la avería se produjo en un turno de noche del fin de semana, no se pudo conseguir ninguna pieza de repuesto hasta el lunes. Esto tuvo graves implicaciones financieras para la empresa, que normalmente opera 24 horas al día, 7 días a la semana.
Este fabricante contaba con un sistema de monitoreo SCADA (Supervisión, Control y Adquisición de Datos) para revisar una falla crítica. Esto requirió esperando que ocurra un fracaso, y solo después de eso podrían comenzar a analizar e interpretar los datos antes de realizar un Análisis de Causa Raíz (RCA).
Pasar a la Industria 4.0 y la monitorización remota les habría dado visibilidad continua sobre el motor. Con datos en tiempo real, podrían haber evitado la avería, ahorrando potencialmente a la empresa alrededor de $295.000 (£240.000).
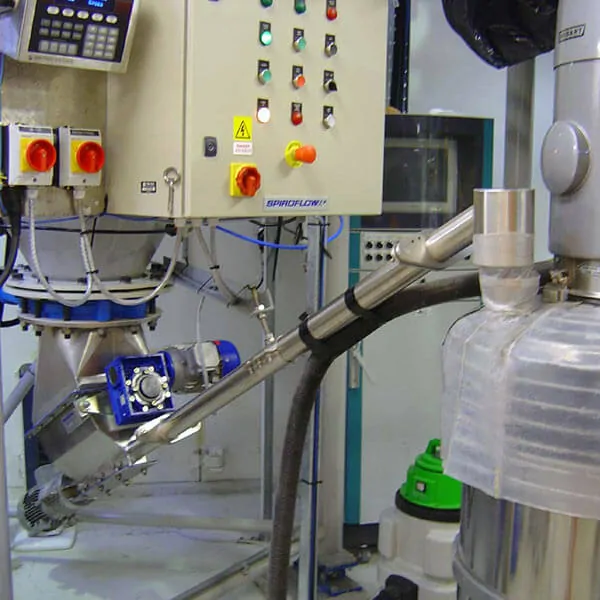
Mejora del control de calidad y la confiabilidad del producto con IIoT
Los fabricantes de sistemas transportadores saben que su rentabilidad depende de tener una producción precisa, de alta calidad y confiable. Según Verizon, en 2017, 60% de los pioneros están mejorando la confiabilidad o el rendimiento de productos y servicios con IIoT. Siendo capaz de Identificar los problemas que pueden causar un producto de calidad inferior. Es esencial, especialmente si el problema es causado por un equipo defectuoso.
Mejorar la calidad del producto está siempre a la vanguardia para muchos fabricantes, ya que genera beneficios potenciales como:
- Mayor satisfacción del cliente,
- Mayores ventas,
- Aumento del precio de venta,
- Costos de fabricación reducidos,
- Reducción de desperdicios.
Mientras que un Un producto de mala calidad tiene el poder de dañar su marca. con costosas retiradas de productos y una pérdida de confianza del consumidor que podría tener graves consecuencias financieras.
Detección temprana y resolución para mejorar la calidad
Identificar los problemas que pueden afectar la calidad del producto es crucial, especialmente cuando pueden detectarse y resolverse tempranamente. Se pueden mitigar los problemas que surgen de equipos que no están calibrados con precisión, que tienen un mantenimiento deficiente o una configuración incorrecta. En este proceso, por ejemplo, el sistema de cinta transportadora desempeña un papel fundamental.
Los dispositivos conectados a IIoT, como SAM, aprovechan los sensores para monitorear y analizar datos continuamente, informando instantáneamente a los empleados clave. Esto les permite tomar medidas inmediatas, ya sea deteniendo la producción o haciendo los ajustes necesarios mientras la línea permanece operativa, abordando eficazmente cualquier problema.
Desbloquear la eficiencia energética: el poder de las actualizaciones de IIoT
Mejorar la eficiencia energética es otra ventaja potencial de una actualización del IIoT. El sector manufacturero, que incluye equipos como un transportador de tornillo flexible, se encuentra entre los mayores consumidores de energía, representando más 37% de consumo energético mundial. Curiosamente, el consumo de energía no está vinculado principalmente a las tasas de producción. En cambio, está fuertemente influenciado por la duración de estados operativos específicos.
Maximizar la eficiencia energética: conocimientos y acciones con IIoT
En un estudio de 2009, se descubrió que se pueden lograr importantes ahorros de energía, estimados en aproximadamente 10-25%, reduciendo los tiempos de espera y optimizando el modo de inicio de máquinas. Esto se aplica a varios aspectos de la fabricación, incluidas las cintas transportadoras. Sin embargo, antes de que la optimización de las máquinas pueda ser efectiva, los fabricantes deben establecer inicialmente una comprensión integral de sus patrones actuales de consumo de energía.
La mayoría de las plantas tienen un programa de producción ininterrumpido en el que realizar un seguimiento del consumo de energía llevaría demasiado tiempo en el día a día. Además, a menos que la información se entregue en tiempo real, es muy probable que Poco pueden hacer los fabricantes para mejorar la eficiencia. de las máquinas.
Con IIoT, los problemas que enfrentan los fabricantes mejoran enormemente porque Los datos sobre eficiencia energética se envían instantáneamente a un panel de control. para que se puedan tomar acciones en tiempo real. Esto puede dar como resultado que los gerentes de planta impulsen un comportamiento de ahorro de energía en el personal y que los directores desarrollen una estrategia clara de ahorro de energía para el taller.
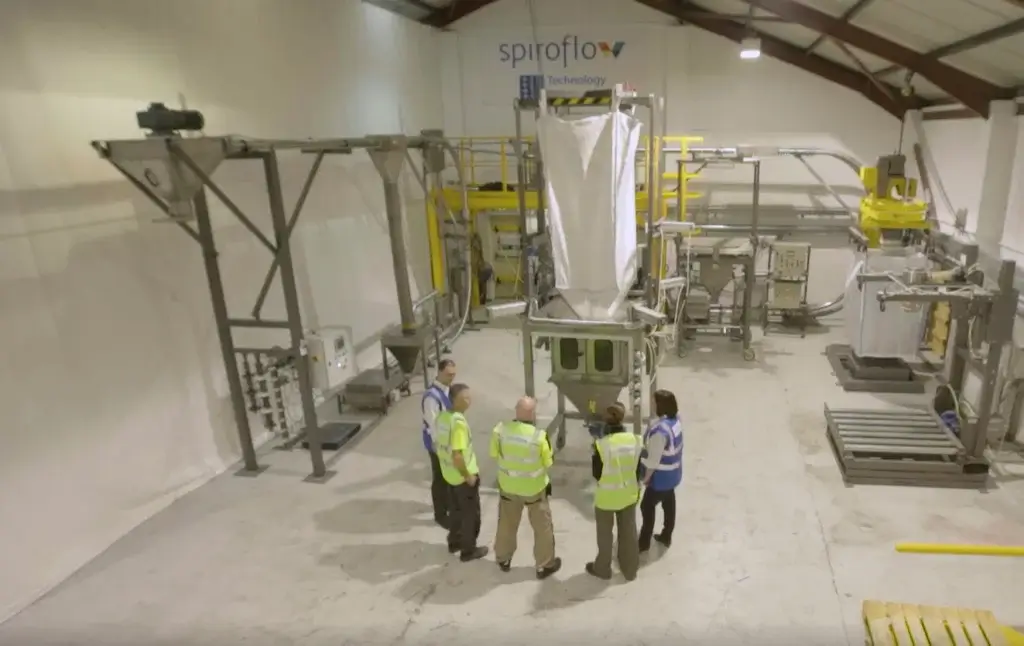
Spiroflow le ofrecerá las mejores soluciones IIoT
El uso de alertas en tiempo real ha cambiado el panorama de la industria en todo el mundo, especialmente entre los fabricantes de cintas transportadoras. Los datos se pueden utilizar como punto de referencia. contra otros equipos para determinar cuáles tienen un mejor rendimiento y al mismo tiempo permitir la resolución proactiva de problemas de bajo rendimiento.
En Spiroflow, nos dedicamos a empoderar a los fabricantes con las últimas soluciones IIoT para optimizar la producción, mejorar la calidad y reducir el tiempo de inactividad. Póngase en contacto con nuestros expertos hoy y emprenda su viaje hacia una fabricación más inteligente.