Aperçu
Depuis plus de 100 ans, l'ammoniac est utilisé dans les installations de fabrication de produits alimentaires et de transformation de la viande comme principale méthode de refroidissement dans les zones de traitement et de production. Bien que généralement considérés comme sûrs, des pannes et des rejets imprévus se produisent. Les risques inhérents doivent être compris dans la conception de ces systèmes et les utilisateurs finaux doivent faire preuve de diligence dans leur surveillance et leur maintenance. Même avec des soins appropriés, des accidents surviennent. La sécurité des travailleurs et des premiers intervenants doit être prise en compte et les systèmes de détection et d'alarme secondaires peuvent constituer une solution efficace pour assurer une visibilité de la zone et faciliter une intervention appropriée.
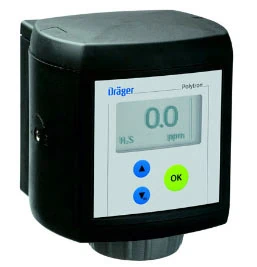
Les usines de fabrication de grande taille et complexes utilisent le refroidissement dans de nombreux domaines. La localisation et l'évaluation rapides du niveau de rejet sont essentielles pour une réponse rapide et sûre à tout incident. Même si les équipementiers et les utilisateurs finaux ont intégré des systèmes de détection des fuites et d'arrêt pour la surveillance principale dans les locaux techniques, une lacune peut exister dans de nombreuses grandes zones de production distribuées et dans les installations de stockage frigorifique éloignées. Les organisations prudentes se sont tournées vers des systèmes de surveillance et d'alarme autonomes pour offrir une visibilité améliorée et aider les équipes d'intervention dangereuses à localiser avec précision et à déterminer la gravité du rejet depuis l'extérieur de la zone affectée.
La portée du projet
ENTREPRISE : UNE GRANDE ENTREPRISE DE FABRICATION ALIMENTAIRE
NOTRE RÔLE : DÉVELOPPER UNE SOLUTION STANDARD POUR LA SURVEILLANCE, L'ANNONCIATION ET LE CONTRÔLE DES TRACES D'AMMONIAC ET LA DÉTECTION DES FUITES CATASTROPHIQUES
Un important client de fabrication de produits alimentaires s'est tourné vers Spiroflow Automation Solutions pour travailler avec lui afin de développer une solution standard pour la surveillance, l'annonce et le contrôle de la détection de traces d'ammoniac ainsi que la détection de fuites catastrophiques. Le système fournirait des fonctions d'affichage et d'alarme hors site situées au bureau de sécurité, et fournirait aux premiers intervenants et aux équipes d'intervention en cas de danger une indication claire de l'endroit où la panne du système s'est produite. De par la nature de la conception de l'instrumentation à 2 niveaux, le système leur permet d'évaluer la situation comme un rejet mineur ou une défaillance plus grave du système avec un rejet important d'ammoniac.
Le système conçu par Spiroflow Automation est un système de surveillance et d'alarme secondaire – autonome du contrôle du compresseur OEM et des systèmes SCADA OEM. Ce système a été développé en réponse aux lacunes découvertes par les équipes EH&S et d'ingénierie de réfrigération de l'entreprise et fonctionne de manière fiable depuis plus de 6 ans sur des sites à travers l'Amérique du Nord.
Critère de design
Le client, en collaboration avec les ingénieurs de Spiroflow Automation, a développé les spécifications des systèmes de critères de conception et a également utilisé les normes d'ingénierie de l'entreprise comme ligne directrice pour la solution finale. Ils se sont tournés vers une conception de système ouvert afin de minimiser la formation, le support et les pièces de rechange pour les équipes de l'usine. Spiroflow a relevé ce défi avec une approche globale. En tant qu'intégrateur de systèmes Rockwell Automation reconnu, Spiroflow connaissait les avantages matériels et logiciels de cette plate-forme et en a recommandé l'utilisation au client.
Dans l’ensemble, les critères de conception suivants ont été identifiés par l’équipe :
1. Plateforme matérielle : Rockwell Automation était la norme en matière d'automatisation des installations et ce système utiliserait l'automate RA ControlLogix et les systèmes d'E/S associés.
2. E/S distribuées : Étant donné que les points de surveillance et de contrôle devaient être situés dans les zones de production, les E/S distantes et l'interface des capteurs devraient utiliser les réseaux Ethernet de fabrication existants.
3. Capteurs : Spiroflow a utilisé des capteurs de détection d'ammoniac de Draeger, Inc. Des sorties analogiques ont été utilisées pour fournir des informations de niveau en temps réel au processeur CLX pour les fonctions de surveillance, d'enregistrement et d'affichage. Les capteurs ont été localisés et installés par les équipes de réfrigération et d'ingénierie du client en fonction de leur connaissance de l'équipement et du processus de l'usine.
4. États d'alarme : Le système devait surveiller et déclencher des alarmes pour plusieurs états. Premièrement, un capteur de détection de fuite mineure serait utilisé pour surveiller la présence d’ammoniac inférieure aux limites OSHA. L'indication d'alarme est déclenchée et affichée sur les écrans PanelView. Si une fuite majeure, causée par une défaillance d'un équipement ou d'une ligne, se produit, des mesures supplémentaires sont nécessaires et le système répond automatiquement par des alarmes visuelles et sonores. De plus, un contrôle automatique se produit pour déclencher les verrouillages et contrôler les ventilateurs de ventilation dans les zones affectées.
5. Verrouillage des commandes : Les exigences ici étaient de fournir un verrouillage et un contrôle spécifiques de l'approvisionnement en ammoniac pour les pannes de zone sur la base d'un plan défini pour chaque installation. En collaboration avec les équipementiers de l'entreprise en matière de réfrigération, d'ingénierie d'installations et d'équipements, Spiroflow Automation a modifié les programmes de contrôle tiers pour verrouiller les systèmes.
6. Évolutivité : Étant donné que chaque installation est unique, la conception du système devrait être modulaire et facilement évolutive pour s'adapter à chaque installation d'usine. L'application devait utiliser des architectures de programmation et de contrôle communes afin de pouvoir évoluer de manière rentable en fonction de la taille de l'installation et des points de surveillance. Les E/S Rockwell Automation ControlLogix ont été utilisées ainsi que des techniques de programmation structurées pour minimiser le temps de conception, de mise en œuvre et de démarrage. Les coûts de formation et de support continu ont été minimisés grâce à l’approche standard utilisée.
EXIGENCES DE SURVEILLANCE ET DE CONTRÔLE DU SYSTÈME
Les fonctions de surveillance, d'alarme et de contrôle suivantes ont été intégrées à la conception :
1. Surveillance continue de tous les capteurs: Les capteurs d'ammoniac à distance ont été scannés en continu par le processeur CLX et une stratégie d'alarme automatisée à 2 niveaux est utilisée.
2. Niveau 2: Une fuite majeure détectée déclenchera une alarme critique et les fonctions de verrouillage du système se produiront.
FONCTIONS DE COMMANDE
Le système fournit des fonctions de contrôle automatisées et manuelles.
CONTRÔLE MANUEL
Déclencheur shunt : le panneau à distance offrira la possibilité de contrôler l'alimentation dans les zones de production via des relais de déclenchement shunt. Étant donné que l'ammoniac peut présenter un risque d'inflammabilité en concentration, il est possible de laisser tomber l'électricité dans une zone affectée.
Test/Contrôle automatique : Chaque relais shunt peut être testé pour permettre la maintenance du système sans déclencher le relais.
CONTRÔLE AUTOMATIQUE
Le système de surveillance de l'ammoniac est conçu pour communiquer avec des équipements discrets et des vannes de régulation dans toute l'usine. En cas d'alarme, le CLX de surveillance établira un verrouillage avec des vannes d'alimentation à distance pour arrêter le flux d'ammoniac dans les systèmes en alarme.
COMMANDE DU VENTILATEUR DE LA SALLE DU COMPRESSEUR
La salle des compresseurs d'ammoniac et d'autres emplacements désignés nécessitent l'utilisation de ventilateurs d'alimentation et d'extraction utilisés pour évacuer l'air en cas d'urgence. Le système surveille les ventilateurs d'alimentation et d'extraction et neutralise les systèmes en cas d'alarme de vapeur.
ALARMES VISUELLES ET AUDIO
Le système offre la possibilité de localiser les alarmes visuelles et sonores dans les zones de production, de maintenance et de sécurité.
Solution automatisée
La solution technique répondait à tous les critères de conception et est opérationnelle depuis 2006. Spiroflow Automation a fourni les panneaux UL/NEMA pour le contrôle et la surveillance centraux de la cabine de garde. Des panneaux distants ont également été installés dans toute l'usine, ce qui a permis une connexion facile aux capteurs.
La conception du programme a utilisé des routines et des fichiers de programme communs faciles à concevoir et à déployer. La conception était également facile à dépanner et à modifier à mesure que les équipements de production et les processus étaient modifiés, ce qui était particulièrement important pour l'usine.
Un écran graphique Rockwell PanelView 1250 a été utilisé. Cette solution a été choisie par Spiroflow Automation car elle permettait l'intégration des configurations d'usine avec des alarmes graphiques et textuelles. Puisqu'il s'agit d'un système dédié et ne nécessite pas de PC, il permet un degré de disponibilité plus élevé et un support négligeable de la part des équipes de maintenance et informatiques du client.
Résumé
Spiroflow Automation a apporté de la valeur au client en tirant parti de la plateforme Rockwell Automation ControlLogix et en développant une stratégie de conception modulaire pour réduire les coûts d'ingénierie et d'installation. La logique de base ayant été validée dans le cadre du déploiement initial du système, la migration vers de nouveaux sites avec des configurations différentes a été simple et directe. Les mises à niveau communes du système ont été facilement prises en charge et la logique a été standardisée dans toute l'entreprise.
De plus, étant donné que les ingénieurs de l'usine étaient expérimentés avec le matériel et la programmation du RA CLX, d'autres personnes peuvent apporter des modifications au système si nécessaire. L’avantage global est que le client dispose d’un système fiable, rentable et qui sera pris en charge pendant de nombreuses années.