Wir freuen uns, dass Premier Foods, der führende Hersteller, kürzlich bei uns eingekauft hat. Sie kauften zwei Spiroflow Big Bag-Entleergeräte und vier flexible Schneckenförderer, um verarbeitete Produkte zu den Verpackungslinien am Standort Histon zu bringen. Das fragliche Produkt ist SMASH Instant-Kartoffelpüree. Da die „Martians“-Werbung von Premier Foods aus den 1970er Jahren zum besten TV-Werbespot aller Zeiten gewählt wurde, zählt SMASH zu den bekanntesten Verbrauchermarken Großbritanniens.
Erstklassige Lebensmittel betreibt sieben Produktionsstandorte in Großbritannien und beschäftigt über 3.000 Mitarbeiter. Ihr Standort in Histon besteht seit über 100 Jahren und beschäftigt rund 350 Mitarbeiter. Hier sind auch Hartley's Jam, Rose's Marmalade und Chivers Jelly zu Hause.
Einführung in die erweiterte Entladung und Förderung
Eine Änderung des Produktions- und Speicheransatzes von SMASH machte die Integration neuer Big-Bag-Entleergeräte und flexible Förderschnecken. Im Gegensatz zu der bisherigen Methode der Bewegung von Produkten durch Überkopf Förderbänder Von der Produktion bis zur Verpackung, die Der derzeitige Prozess beinhaltet die Verwendung von 2m3 grosse Taschen. Diese werden mit Gabelstaplern transportiert, mit einer Rate von 16 pro Tag, was eine optimierter und kontinuierlicher Workflow Von der Produktion bis zur Verpackung.
Effizienter und sicherer Entladevorgang
Die Einführung von Spiroflow Big Bag Entleerer hat deutlich verbesserte den Betrieb der Packhalle. Diese Entleerer, ausgestattet mit Big Bag Hebe-/Stützrahmen, gewährleisten eine staubfreies Umfüllen des Inhalts.
Das einzigartige Design mit einem ringförmige flexible Membran sorgt für eine staubdichte Abdichtung, was einen kontrollierten und sicheren Entleerungsprozess ermöglicht. Die Effizienz des Systems wird durch pneumatische Verschlussstangen und einen intelligenten Mechanismus, der die Blitzbeutel allmählich anhebt, um die Produktentladung zu optimieren, weiter verbessert.
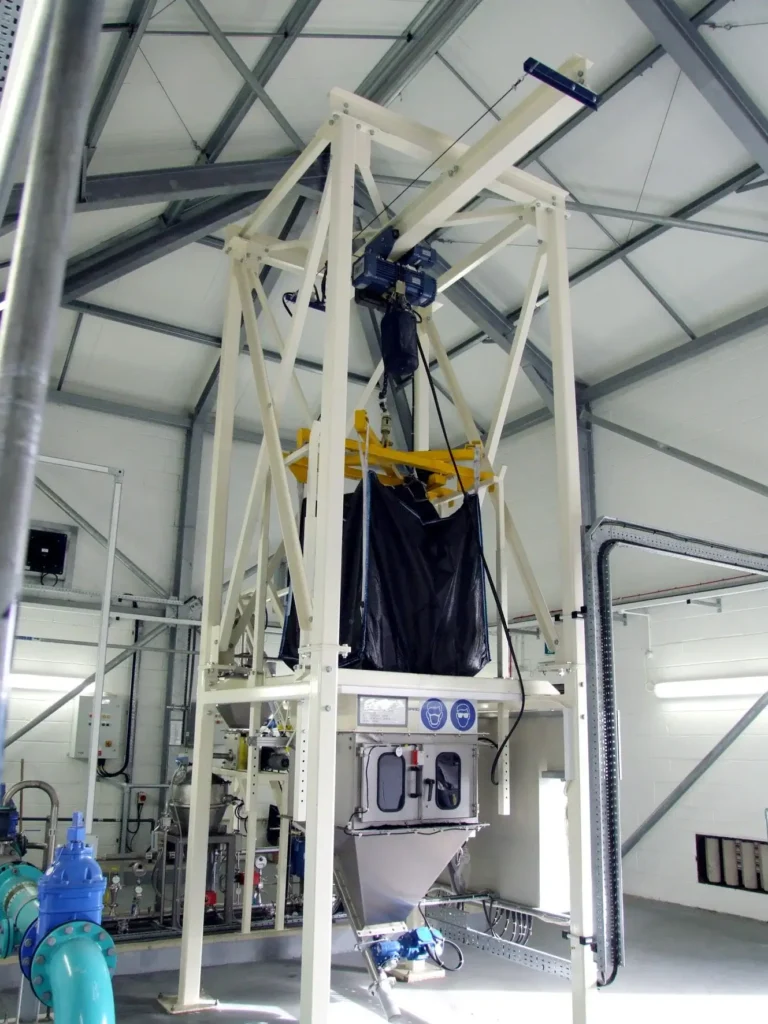
Nahtlose Produktverteilung mit flexiblen Förderlösungen
Im Mittelpunkt des Betriebs spielen die fortschrittlichen Förderlösungen von Spiroflow eine entscheidende Rolle bei der Rationalisierung des Materialtransfers zu den Verpackungslinien. Diese Systeme sind Entworfen mit Blick auf Flexibilität und Präzision, um sicherzustellen, dass Produkte effizient und effektiv an ihre Bestimmungsorte transportiert werden. So geht's Flexibler Schneckenförderer von Spiroflow verbessert den Prozess:
- Nutzen Sie zwei flexible Spiroflow-Schneckenförderer von jedem Entlader, um eine gründliche Verteilung auf vier Verpackungslinien zu gewährleisten.
- Förderbänder sind in Länge und Winkel verstellbar. Dies ermöglicht einen vielseitigen Aufbau.
- Sie verfügen über Füllstandssonden zur präzisen Kontrolle von Durchfluss und Volumen und gewährleisten so eine gleichbleibende Produktionsqualität.
Unser Anspruch ist Qualität und Effizienz
Die Entscheidung für eine Partnerschaft mit Spiroflow wurde durch den erfolgreichen Einsatz ihrer Geräte bei der Verarbeitung von Zucker beeinflusst. Auch die positiven Ergebnisse von Tests durchgeführt, um das System für SMASH anzupassen hat diesen Deal besiegelt.
Diese Anpassung, gepaart mit selbst entwickelten Steuerungssystemen, unterstreicht Spiroflows Engagement, optimale Fördertechnologien für industrielle Anwendungen bereitzustellen. Das Ergebnis ist ein System, das nicht nur die Erwartungen von Premier Foods erfüllt, sondern auch erhebliche Verbesserungen bietet in Einsparungen bei Produktqualität, Arbeitsaufwand und Betriebsmitteln. All dies unterstreicht, wie wertvoll eine Investition in erstklassige Förderbandhersteller und -technologien ist.
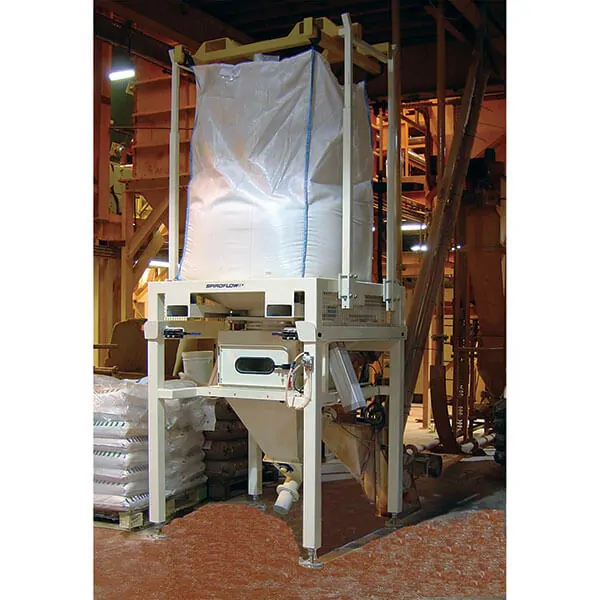
Steigern Sie Ihre Produktionseffizienz mit Spiroflow-Förderlösungen
Wenn Sie Ihre Produktion ebenfalls steigern möchten, wenden Sie sich gerne an Spiroflow. Unser Team ist bereit, Sie zu versorgen mit individuelle Lösungen, die auf Ihre Bedürfnisse zugeschnitten sind, indem wir unsere fortschrittlichen Förder- und Entladetechnologien nutzen. Egal, ob Sie die Effizienz zu steigern, die Produktqualität zu verbessern oder die Kosten zu senken, unsere Hersteller von Fördersystemen verfügen über das nötige Know-how, um dies zu ermöglichen. Lassen Sie sich durch Ihre Produktionsherausforderungen nicht aufhalten. Kontaktieren Sie Spiroflow und machen Sie noch heute den ersten Schritt zur Optimierung Ihres Materialhandhabungsprozesses.