Un Spiroflow convoyeur aéromécanique, fourni par Spiroflow Systems Inc., une société partenaire, joue un rôle clé en garantissant un transfert fluide et sans grumeaux de la poudre acrylique fine dans un mélangeur cylindrique substantiel. Ce processus est crucial dans la fabrication de la peinture thermoplastique Fluorex™ chez Soliant LLC, située à Lancaster, en Caroline du Sud, aux États-Unis.
Introduction à Fluorex™ et Soliant
Fluorex™ offre une option supérieure par rapport aux méthodes conventionnelles de peinture et de placage, se distinguant par sa durabilité améliorée, son prix abordable et son respect de l'environnement. La gamme Soliant de films et revêtements décoratifs thermoplastiques, disponible dans une gamme de plus de 140 couleurs, trouve application dans divers secteurs tels que l'automobile, la marine, l'architecture, la signalisation, les appareils électroménagers, l'électronique, les télécommunications, etc. Plus précisément dans le domaine automobile, le film de Soliant est appliqué à 20 modèles distincts de voitures et de camions.
Défis avant le système Spiroflow
Avant d'acquérir les technologies de convoyeur Spiroflow au début des années 2000, le personnel de Soliant s'occupait du déplacement physique de fûts de 125 kg chargés d'acrylique. poudre de résine à une balance pour incorporation au mélange. Après avoir déterminé le poids, les employés transféreraient manuellement environ 700 grammes de poudre de ces fûts dans le récipient de mélange, démarrant ainsi le processus de production de Fluorex™. Le rôle de la balance était essentiel pour garantir que la quantité précise de poudre nécessaire pour chaque mélange de peinture spécifique était ajoutée. Dans le récipient, cette poudre était ensuite mélangée pour obtenir une consistance similaire à celle de la mayonnaise.
De plus, avant ce transfert, il s'agissait nécessaire pour que le personnel examine manuellement le contenu de chaque fût, en brisant les grumeaux ou la poudre adhésive. Cette approche manuelle entraînait des vitesses variables et cohérences entre différentes applications.
Nécessité d'un contrôle de qualité amélioré
En moyenne, chaque procédure prenait environ 25 minutes par travailleur, ce qui représente près d'une heure de travail pour chaque tâche. Mark Beard, ingénieur en développement de produits chez Soliant, a souligné : « Le le processus manuel était laborieux et il manquait du contrôle de qualité nécessaire. Il a ajouté : « Un système fiable et automatisé était essentiel pour garantir une qualité constante d'un lot à l'autre et pour assurer l'uniformité de la vitesse et du flux des matériaux. »
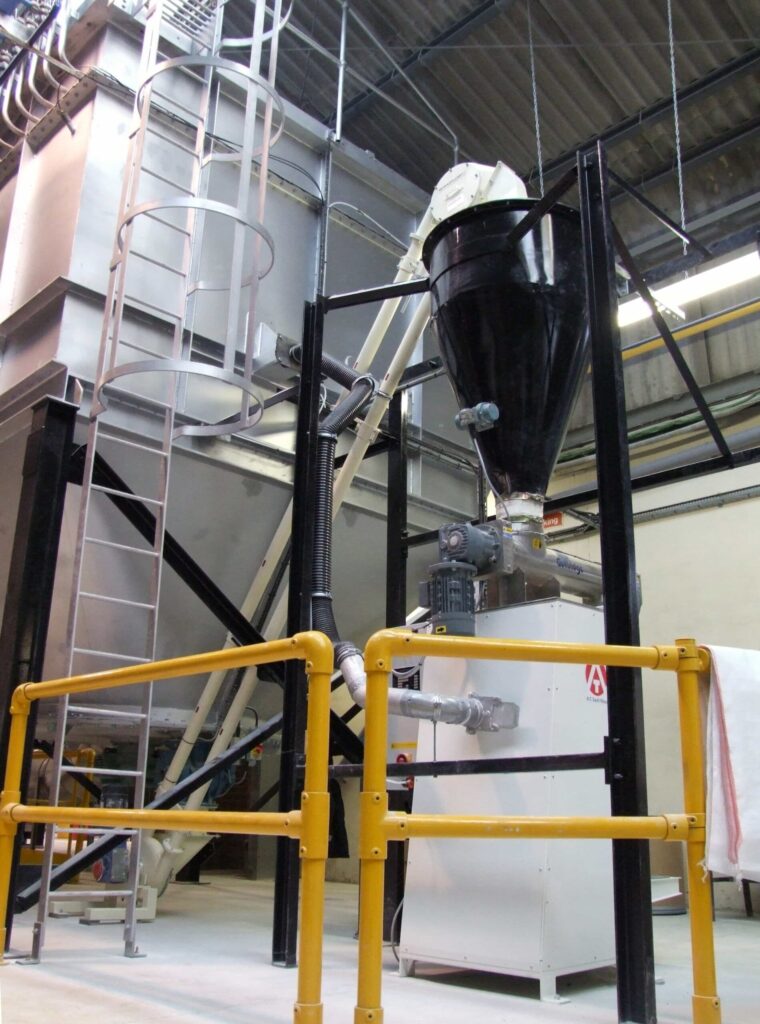
Découverte et sélection de Spiroflow
Après avoir mené ses recherches, Beard a proposé l'utilisation du Spiroflow portable convoyeur aéromécanique, une décision influencée par une annonce qu'il a trouvée dans une publication spécialisée. Beard a fait remarquer : « Au départ, nous ignorions l'expertise de Spiroflow malgré leur proximité avec nous. » Il a ajouté : « Notre visite à leur usine a été révélatrice. Voir leurs connaissances et leurs compétences, surtout après qu'ils ont fait la démonstration de leurs équipements utilisant notre poudre spécifique, nous ont assuré de leur adéquation à nos besoins.
Description du système Spiroflow
Spécialement adapté aux exigences de Soliant, notre équipe a conçu un système de convoyeur et de distribution en acier inoxydable. Ce système comprend un convoyeur aéromécanique incliné de 2,25 mètres de long en ligne droite, complété par une trémie de basculement de sacs à son point de départ. Chaque partie de ces systèmes de convoyeurs industriels Spiroflow est monté sur un châssis mobile, équipé de deux roulettes fixes et de deux roulettes rotatives. Ces roulettes facilitent la maniabilité sans effort et sont équipées de freins verrouillables pour assurer une sécurité optimale.
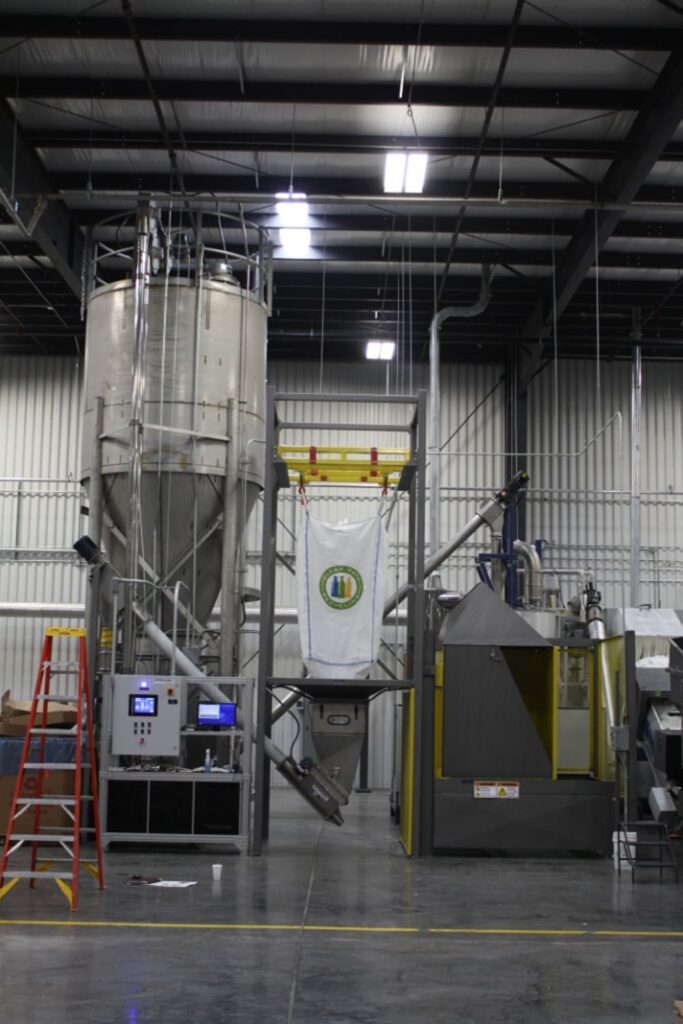
Intégration dans le processus de Soliant
Lorsqu'il est temps d'intégrer les matériaux dans le mélangeur, le convoyeur mobile est placé avec précision sur une plate-forme de pesée carrée de 1,25 mètre, encastrée dans le sol pour s'aligner avec le niveau de l'usine. Après avoir positionné le convoyeur sur cette plateforme, son poids est remis à zéro, permettant le chargement précis de la quantité requise de poudre acrylique dans la trémie d'alimentation du convoyeur. La poudre est ensuite versée dans la trémie en passant à travers un rideau de bandes de plastique situé à l'avant de la hotte anti-poussière aérienne.
Cette hotte anti-poussière est reliée à un système d'extraction de poussière, garantissant un fonctionnement propre, respectueux de l'environnement et sans poussière. Une grille placée au sommet de la trémie aide à décomposer les amas de matériaux, résolvant ainsi un problème majeur rencontré avec la méthode précédente. Le flux de matière de la trémie vers le convoyeur est régulé par une vanne rotative. De plus, six coussinets vibrants pneumatiques sont judicieusement disposés autour de la trémie, favorisant un flux constant et ininterrompu de poudre dans la vanne rotative à la sortie de la trémie, évitant ainsi tout blocage.
Aspects techniques du système de convoyeur
Les solutions de bandes transporteuses sont dotées de tubes d'un diamètre de 80 mm et sont réglées à un angle de 45 degrés pour le fonctionnement. Un moteur pneumatique, standard dans les environnements dangereux, alimente à la fois le convoyeur et la vanne rotative. À des fins de maintenance, un panneau d'accès verrouillable est installé pour faciliter le nettoyage des composants internes du convoyeur, et un panneau transparent dans l'un des tubes permet aux opérateurs d'évaluer quand un nettoyage est nécessaire.
Ces systèmes de bande transporteuse sont constitués de plusieurs disques en polyuréthane, régulièrement espacés et attachés à un câble métallique, se déplaçant dans des tubes d'acier parallèles dans une boucle continue à grande vitesse. À chaque extrémité, la corde s'enroule autour de pignons conçus sur mesure. Un pignon entraîne la corde et les disques, tandis que l'autre maintient la tension de la corde. En maintenant une vitesse constante et élevée de l'ensemble câble et disque, les bandes transporteuses génèrent un flux d'air qui fluidise et transporte efficacement le produit vers le récipient de mélange, où la poudre est ensuite évacuée par centrifugation. Ce mode de transport est économe en énergie, réduit l’usure de la production, et permet des taux de production variables, de élevé à faible.
Impact et avantages
Beard affirme que le problème de la poudre adhésive grumeleuse a été efficacement résolu, ce qui a permis une opération pratiquement sans stress. Il a exprimé sa satisfaction en déclarant : « Cet équipement est pour nous un atout fiable et de haute qualité. » Il a ajouté : « Le transfert dans le navire est uniforme et la fiabilité du système est remarquable. Ce qui nécessitait auparavant plus d'une heure de travail manuel est désormais réalisé en moins de 20 minutes, grâce à l'automatisation complète, et cela exige peu ou pas de surveillance.”
Maintenance et support pour le convoyeur aéromécanique
Beard a mentionné que le système ne nécessite presque aucun entretien. Il a noté que depuis plus de cinq ans depuis son installation, le seul entretien régulier a consisté à ajuster le tension de la corde et effectuer des tâches de nettoyage. Il a également félicité l'équipe après-vente Spiroflow pour son soutien exceptionnel. Si vous recherchez un système de bande transporteuse fiable et nécessitant peu d’entretien, pensez à Spiroflow pour vos besoins. Notre équipe d'experts est prête à fournir des solutions de premier ordre et un soutien continu. Contactez Spiroflow aujourd’hui pour améliorer vos opérations grâce à nos solutions de convoyeurs innovantes.