Customer Requirements
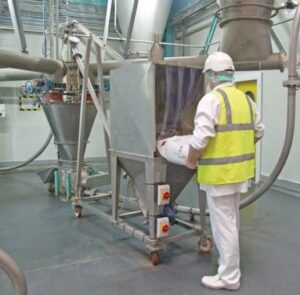
This chocolate producer’s facility was built to produce several thousand tons of bulk milk chocolate in liquid form and operates 24/7, based on seasonal demand.
1) When demand for a dark chocolate alternative arose, the company met it by manually carrying 55lb/ 25kg bags of cocoa from a storage area and up two flights of stairs to the mixer.
2) This grueling process was repeated up to 30 times a day.
3) The Operations Manager saw that cocoa could be introduced into the hopper of a pneumatic conveying system.
4) This could deliver the chocolate powder and sugar from the main storage silos to the dosing feeder above the mixture.
5) The collection hopper, located close to where the ingredients were stored, could pneumatically convey the cocoa powder up two stories to the mixer in a matter of seconds.
6) They also needed a way to load cocoa into the collection hopper, where the inlet was just over 6.5ft/ 2m above floor level.
Spiroflow Solution
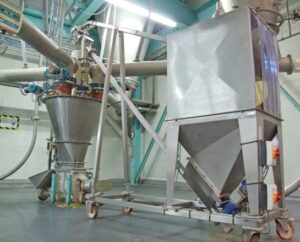
We tested the ingredients in their test center and found that the best solution was a mobile Flexible Screw Conveyor with a Proscrew Spiral.
– The Proscrew is the ideal choice for cohesive products that are difficult to convey because they give maximum push with minimal contact between the spiral and the conveying tube.
– A side mounted sack spigot was attached to an integral bag tip station allowing emptied bags to be easily discarded after use.
– For days when only milk chocolate is produced, the conveyor and tip station, mounted on a mobile frame, is easily moved out of the way when not in use.
– After each dark chocolate run, the conveyor is purged with sugar to ensure no cocoa revenue remains.
The customer later commented how impressed they were with the quality of the conveyor and how easy it has been to keep clean since its installation in July 2008. They looked at other suppliers but found that Spiroflow offered the highest quality solution.