T5 Low Headroom Unloader
System OVerview
Spiroflow’s Type 5 bulk bag unloader is designed for low headroom locations. Designed to allow discharging of bulk bags in areas with a low ceiling height, or locations with a low lift forklift.
The Type 5 Unloader utilizes a split frame design to allow bulk bag rigging on the ground before lifting the bag on to the lower untie frame. Processors with batching operations may choose to have several bag upper frames for use with one discharge station, allowing them to partially empty, re-tie and store bulk bags.
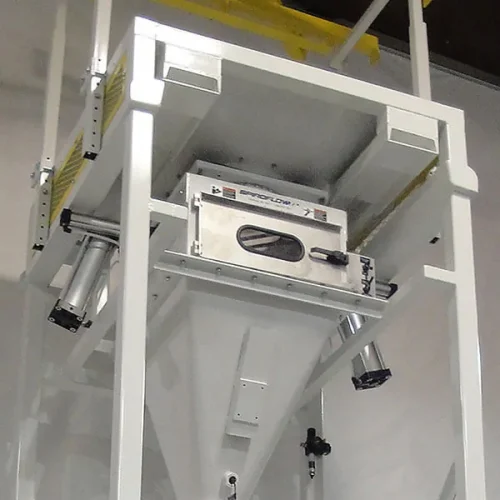
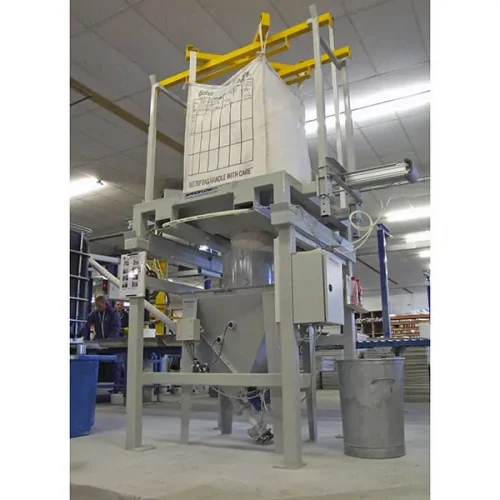
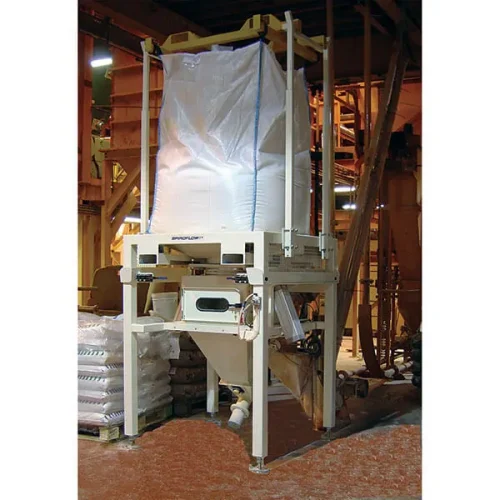
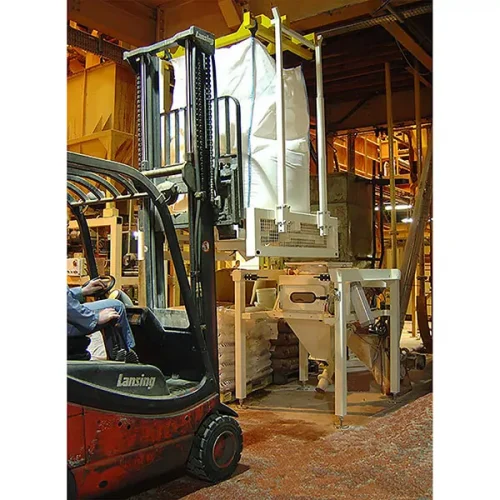
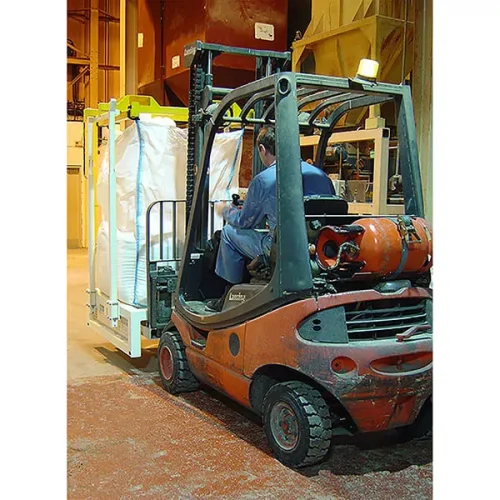
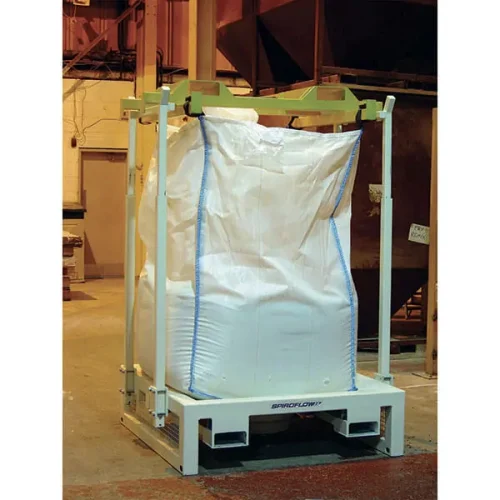
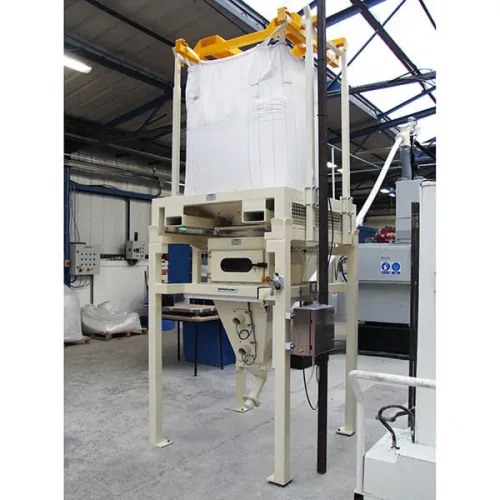
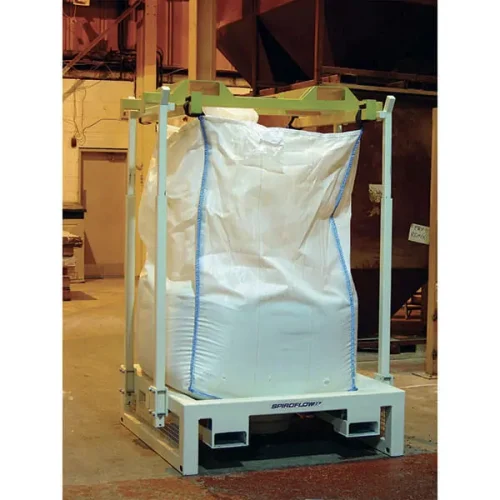
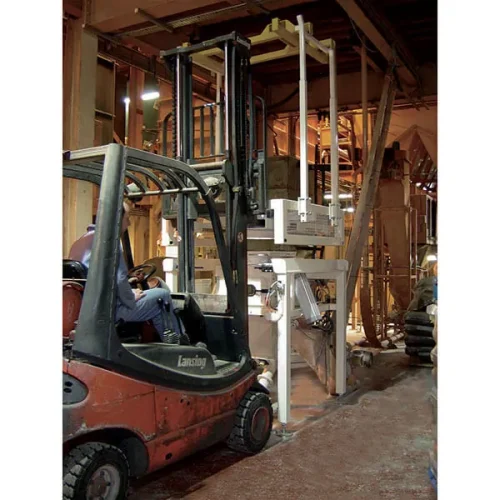

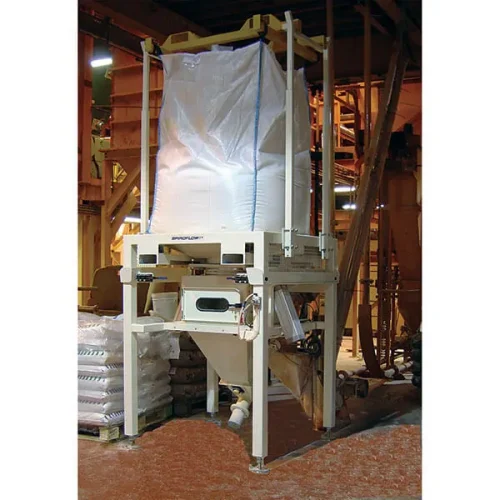
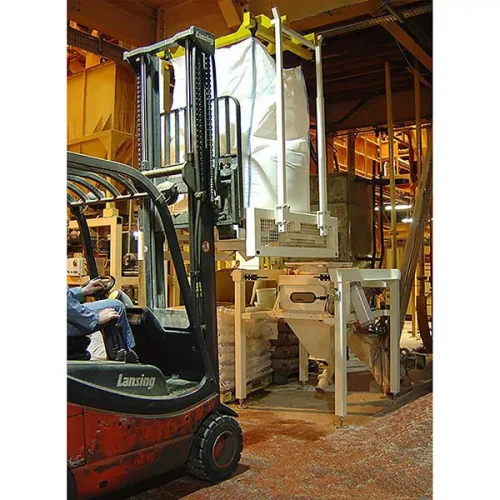
Features
- Removable top frame
- Dust-tight spring-loaded docking seal
- Bag tensioner insures total emptying
- Integral conveyor or feeder
- Dust control
HOW IT WORKS & BENEFITS
The T5 Low Headroom Bulk Bag Unloader is used in areas with restricted headroom.
The bulk bag is loaded onto the bag support dish upper frame while the dish is at ground level & then lifted onto the lower discharge frame with a forklift.
This design is used where there is limited overhead clearance.
The bag discharge lower frame is designed with large channels designed to receive the bag support dish upper frame.
The support dish upper frame includes a dust seal to prevent dusting during material unloading.
The discharge of the chute is custom made to fit the application.
The process steps are as follows:
- A bulk bag of product is fitted with the Bag Lifting Frame.
- The operator will lift the bulk bag into place with a forklift into the bag support upper frame assembly.
- The Lifting Frame rests on the Side Tensioning Frame.
- The weight of the bag compresses the springs & the bottom of the bulk bag rests on the Support Dish.
- The operator will use the forklift to lift the entire upper framework from below the bulk bag & position it into the lower discharge frame.
- With the weight of the bag safely supported, the operator can now freely access the bottom spout of the bag.
- The operator opens the access door & unties the bag spout.
- As the bag empties, the springs in the side frame will keep a constant tension on the bag ensuring complete emptying of its contents.
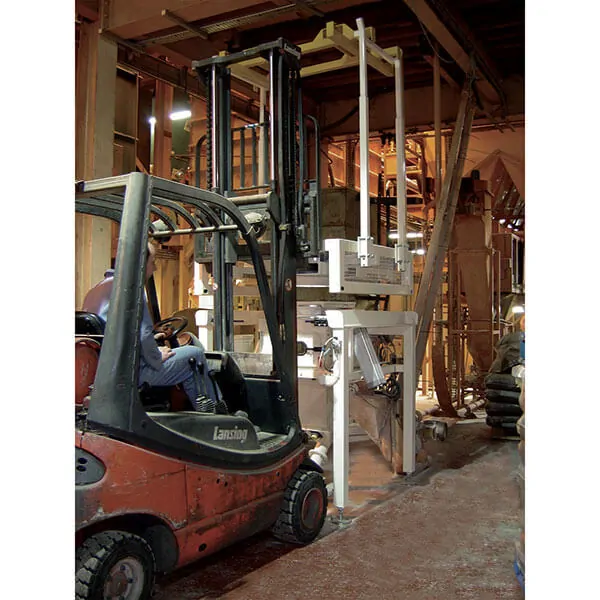
STEP 1: Lift Off Top Section

STEP 2: Position Bulk Bag & Attach Lifting Frame
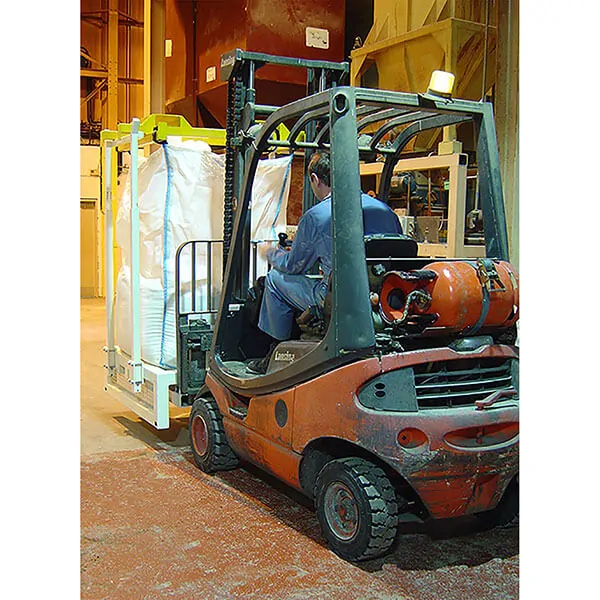
STEP 3: Move the Top Frame into the Unloader
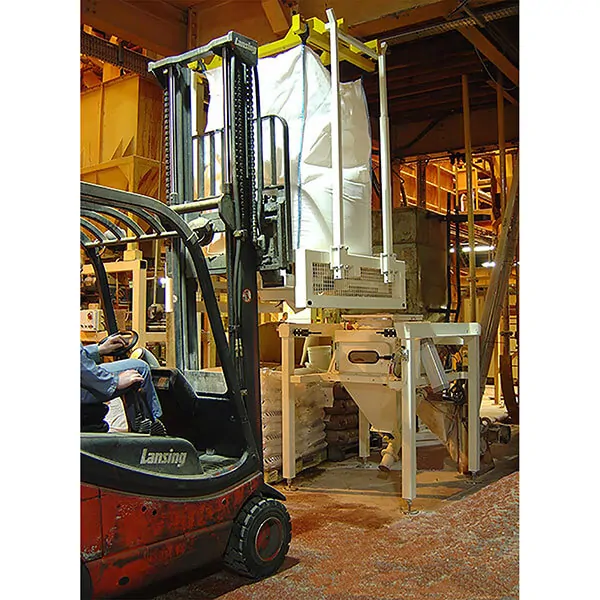
STEP 4: Move the Top Frame into Position
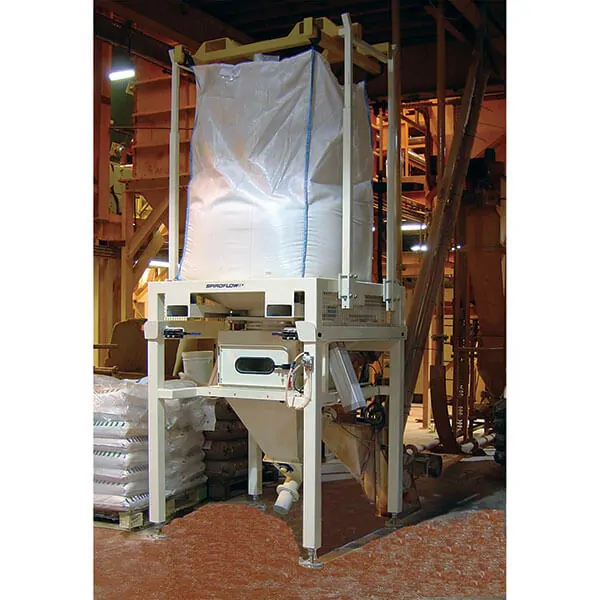
The bulk bag is ready to empty.
MODELS & SPECIFICATIONS
SPECIFICATIONS
The T5 Low Headroom Bulk Bag Unloader is used in areas with limited overhead clearance.
Utilizing a split frame design the Type 5 unloader allows operators to load the bulk bag onto the bag support upper frame at ground level. Then lift it into place on the discharge lower frame.
STANDARD MATERIALS OF CONSTRUCTION
- Carbon/mild steel is standard.
- Optional 304 or 316 stainless steel is available.
PNEUMATIC REQUIREMENTS
- Side Massage: 80 PSI (5.5 Bar) at 2 CFM (56.6 L)/Cycle
- Corner Massage: 80 PSI (5.5 Bar) at 4 CFM (113.3 L)/Cycle
- Bottom/Dish Massage: 80 PSI (5.5 Bar) at 1 CFM (28 L)/Cycle
- Spout Closure Bars: 80 PSI (5.5 Bar) at 1 CFM (28 L)/Cycle
- Chute/Hopper Vibrator: 80 PSI (5.5 Bar) at 3 CFM (85 L)/Cycle
- Dust Collector: 80 PSI (5.5 Bar) at 35 CFM (991 L)/Cycle
ELECTRICAL REQUIREMENTS
- Optional Chute/Hopper Vibrator: 0.13 hp (.1 kW)
- Optional Hopper Agitator: 0.33 hp (.25 kW)
- Optional NEMA 4/ATEX Panel with ON/OFF Switch for Vibrator or Agitator: 0.33 hp (.25 kW)
- Optional Dust Collector: 1.5 hp (1.1 kW)
- Optional Level Probe: 24V DC
DUST CONTROL/AIR DISPLACEMENT
- Dust Extraction Port Optional Integrated
- Dust Collector: NEMA 4, TEFC (Stainless Steel Only)
- Optional Integrated Dust Collector: XP (Stainless Steel Only)
- Optional Free-Standing Dust Collector: NEMA 4, TEFC (Stainless Steel Only)