T2 Bulk Bag Unloader By Volume
System OVerview
Our T2 bulk bag unloader by volume operates on a volume basis and can enable controlled release.
The T2 unloader offers a durable and cost effective solution to unloading bulk bags. An enclosed untie chamber with dust filtration port contains equipment while discharging. Spiroflow offers additional safety and massage options to tailor the T2 unloader to customer’s requirements.
Spiroflow’s expertise in powder handling, allow us to suggest the most effective transfer methods for your material. The Type 2 is capable of being integrated with any of Spiroflow’s conveyance equipment, and/or our customer’s existing equipment.
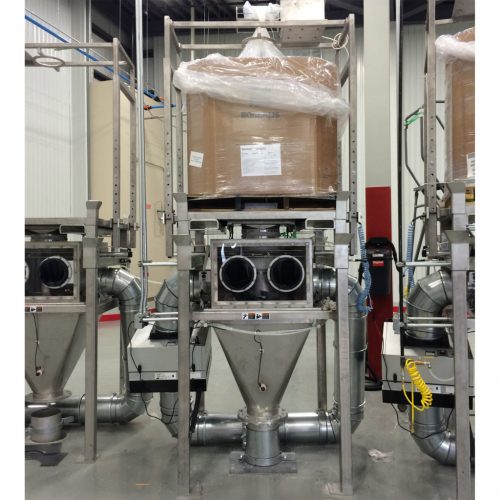
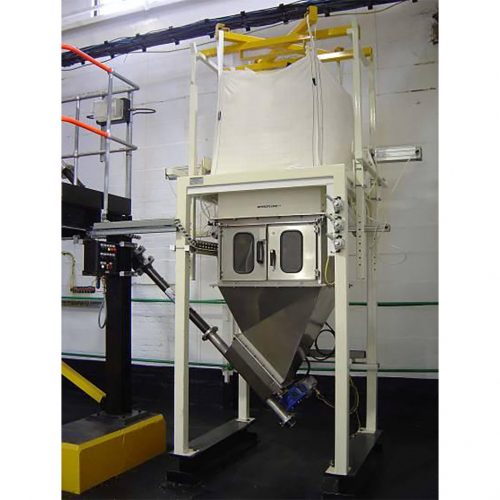
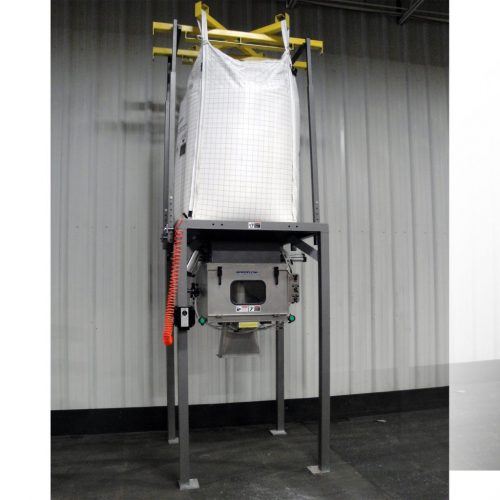
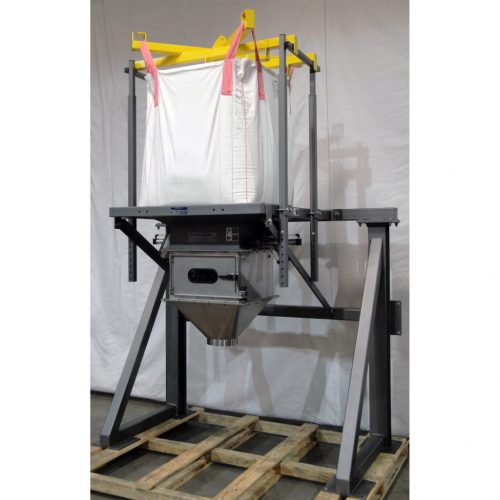
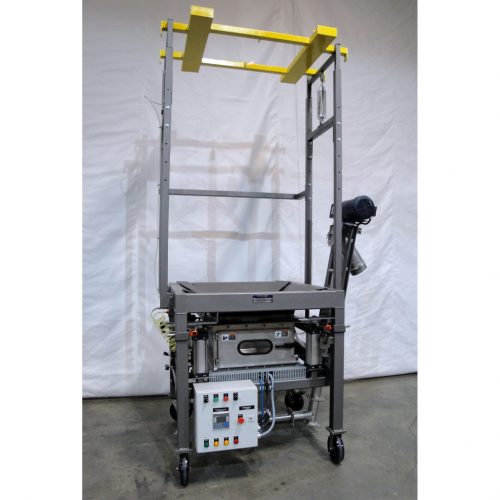
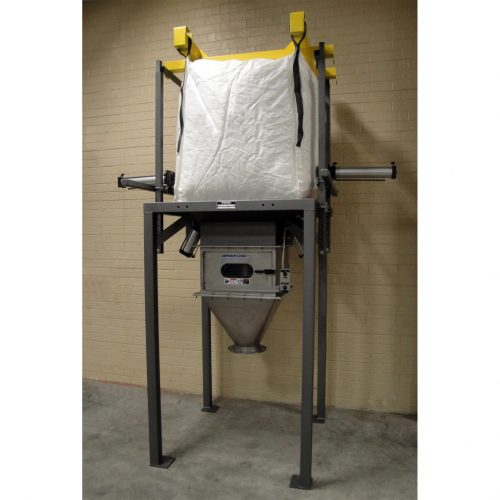

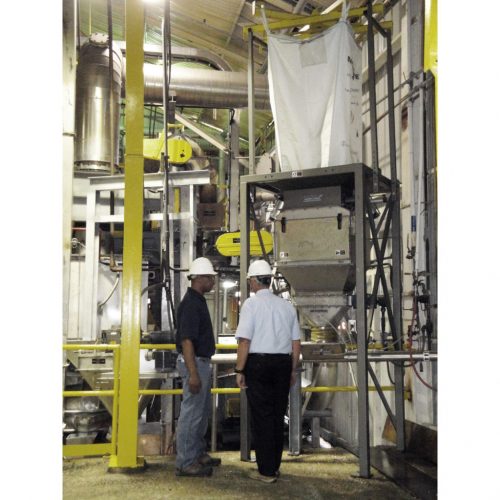
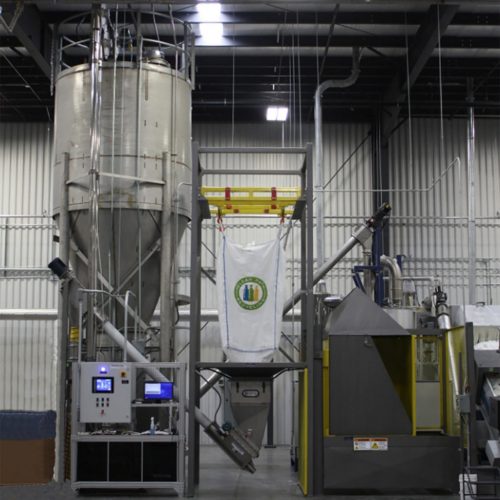
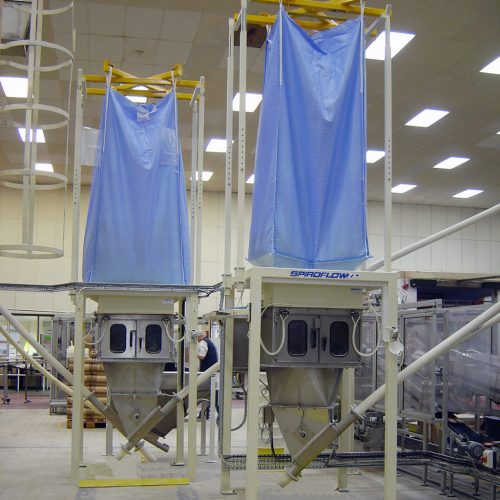
Features
- Discharge without dust.
- Engineered for discharging materials with challenging flow properties.
- Compatible with various bulk bag styles, supporting weights up to 2 tonnes (4,400 lb).
- Options for mobility.
- Incorporated bag tensioning feature guarantees complete evacuation of bag contents, eliminating waste and spillage.
- Automated content transfer through a built-in removal conveyor.
- Extensive selection of designs and additional components.
HOW IT WORKS & BENEFITS
The T2 universal bulk bag unloader specializes in volume-based unloading. This unloader features a support dish constructed to fit most bottom-spout bulk bags. The spout of the bag extends through the center of the dish, allowing easy access. A dust-free seal is created by the bulk bag against the support dish.
The Type 2 universal unloader offers a variety of design choices for enhanced flexibility and user convenience. Its discharge chute is designed to suit the requirements of each application.
The T2 bulk bag unloaders are designed for simplicity and ease of use. Here’s the basic operation process:
- Attach the bulk bag to the lifting frame.
- Use a forklift to elevate the bag and position it onto the side tensioning frame.
- The bag’s weight compresses the springs, positioning the bottom of the bag on the support dish.
- The bag spout needs to be pulled into the untie chamber.
- Then the door closed and spout closure bars engaged to prevent material from falling on an operators arms when untying.
- Then the operator goes in and unties the bag spout. Closes the door and disengages the spout closure bars to allow product to begin flowing.
- The springs on the tensioning frame push the bag upwards and the material exits and the weight of the bag decreases. Allowing the bag to completely empty of material
- Material falls into the chute, moving via the integrated conveyor to the next process step.
- After emptying, retie the bottom spout and remove both the lifting frame and the bag.
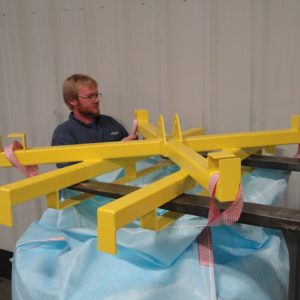
The loops of the bag are attached to a bag lifting frame and the liner clamped.

The spring tension would be relieved as the bag loses weight
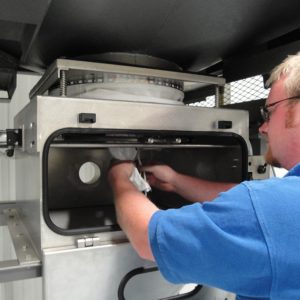
Integral chute has an access door for easy bag untying. Patented spout closure bars ensure the bag remains tightly closed until the discharging process starts.
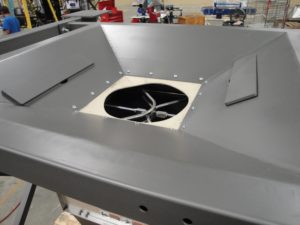
Pneumatically operated massage system, adjustable in position for optimum effectiveness, ensures a consistent flow of difficult products.
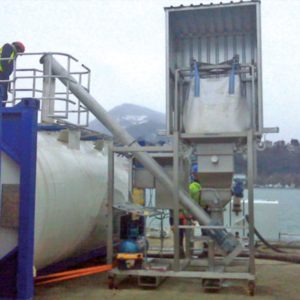
An integral conveyor transfers bag contents directly to your process or, in this case, a tanker.
SPECIAL APPLICATIONS
While there is a wide array of bulk bag unloaders in our offer, we frequently create customized equipment tailored to our customers’ requirements. Some of the examples of the more unique designs include the following:
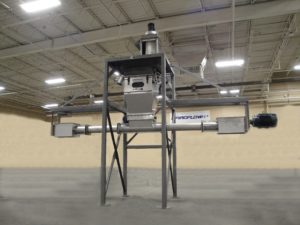
This specialized bulk bag unloader features a horizontal screw conveyor capable of directing material to either of its two outlets. Additionally, the unit is equipped with an integrated dust collector, hopper vibration, and a bottom bag massage system for enhanced functionality.
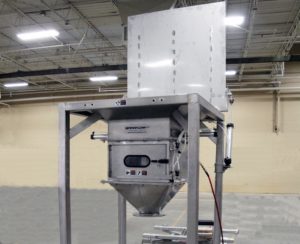
This tailor-made bulk bag unloader is equipped with a uniquely designed lid, operated pneumatically for enhanced functionality.
COMPONENTS & OPTIONS
MODELS & SPECIFICATIONS
Our T2 bulk bag unloader is just one among the diverse offer of bulk bag unloader and discharger models we provide. We commonly blend and adapt the features of our different models to meet the unique requirements of specific applications. Additionally, we frequently craft bespoke designs. Below is an overview of our fundamental models. A Spiroflow Sales Engineer will evaluate your specific needs and suggest the most suitable configuration for your task.
SPECIFICATIONS
The T2 Bulk Bag Unloader specializes in volume-based material unloading. Its construction is entirely welded, featuring a support dish compatible with any bottom-spout bag. The spout of the bag extends through the center of the dish for easy access. The bulk bag creates a dust-free seal with the support dish. Constructed with a robust 3-inch (80mm) square steel tube frame, it’s directly welded to the support dish. The discharge chute is tailored to the specific application.
As with all our bulk bag unloaders, this model offers a variety of design options to ensure optimal versatility and user-friendliness.
STANDARD MATERIALS OF CONSTRUCTION
The standard material used is carbon/mild steel.
Options for 304 or 316 stainless steel are also available.
PNEUMATIC REQUIREMENTS
Side Massage: 80 PSI (5.5 Bar) at 2 CFM (56.6 L)/Cycle
Corner Massage: 80 PSI (5.5 Bar) at 4 CFM (113.3 L)/Cycle
Bottom/Dish Massage: 80 PSI (5.5 Bar) at 1 CFM (28 L)/Cycle
Spout Closure Bars: 80 PSI (5.5 Bar) at 1 CFM (28 L)/Cycle
Note: If run continuously 8 L/min @ 5.5 bar
Chute/Hopper Vibrator: 80 PSI (5.5 Bar) at 3 CFM (85 L)/Cycle
Dust Collector: 80 PSI (5.5 Bar) at 35 CFM (991 L)/Cycle
ELECTRICAL REQUIREMENTS
- Optional Chute/Hopper Vibrator: 0.13 hp (.1 kW)
- Optional Hopper Agitator: 0.33 hp (.25 kW)
- Optional NEMA 4/ATEX Panel withON/OFF Switch for Vibrator or Agitator: 0.33 hp (.25 kW)
- Optional Dust Collector: 1.5 hp (1.1 kW)
- Optional Level Probe 24V DC
DUST CONTROL/AIR DISPLACEMENT
- Dust Extraction Port
- Optional Integrated Dust Collector: NEMA 4, TEFC (Stainless Steel Only)
- Optional Integrated Dust Collector: XP (Stainless Steel Only)
- Optional Free-Standing Dust Collector: NEMA 4, TEFC (Stainless Steel Only)
CONTROLS
Our T2 bulk bag unloaders are available with control options, either with or without a Variable Frequency Drive (VFD). Additionally, we offer controls for motor starters to operate a hopper agitator, dish vibrator, or dust collector. For detailed specifications, please discuss your control needs with a sales engineer.