System Solutions
At Spiroflow, we’re all about innovation and delivering top-notch system solutions that include conveyor technologies, food processing systems, loss-in-weight chemical dosing systems, and gain-in-weight bulk bag filling systems. We understand that our customers’ needs are constantly changing, so we make sure we’re always ahead of the curve with the latest conveyor solutions.
Our wide range of products is designed to meet the diverse needs of processors who often require more than just a single piece of equipment. Our experienced engineers are experts at picking the right machinery and integrating it seamlessly into your existing setup, ensuring that your operations run smoothly and efficiently.
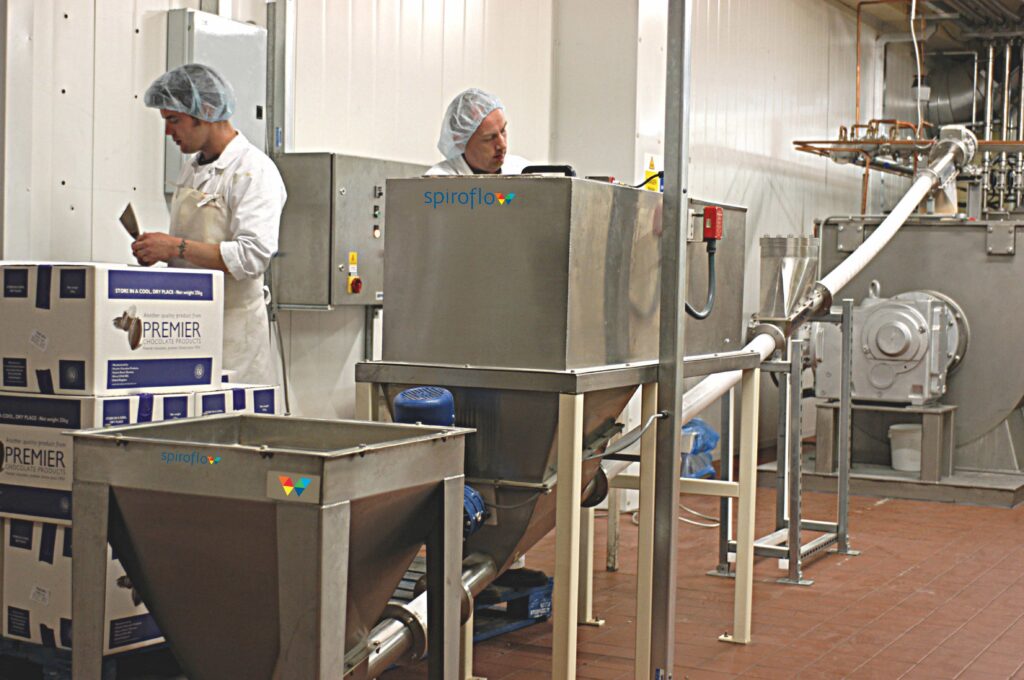
Food Processing Systems
Our tailor-made system expertly blends bread crumbs and seasonings for chicken nuggets. It starts with a bulk bag discharger and a flexible screw conveyor that transport premixed seasonings to a surge hopper. This hopper then supplies the seasonings to a precise loss-in-weight feeder, which moves them to a horizontal flexible screw conveyor.
Next, a large hopper feeds bread crumbs to another loss-in-weight feeder, linking to a slightly bigger flexible screw conveyor. This setup merges the seasonings and bread crumbs in a continuous mixing process.
The blend then travels to a hopper, followed by vertical lifting through an aero-mechanical conveyor to another flexible screw conveyor (not shown here). Finally, the mixture heads to a bulk bag filler or packaging machine.
Loss-in-weight Chemical Dosing Systems
The loss-in-weight chemical dosing system was designed by Spiroflow engineers for a top battery manufacturer. They were looking for conveyor systems manufacturers that could elevate their operations. This system combines specific amounts of carbon black, graphite, and two types of EMD.
The conveyor belt system we engineered involves two bulk bag dischargers directing EMD into a hopper, while bag dump stations with glove boxes and flexible screw conveyors add carbon black and graphite. After blending these ingredients, an aero mechanical conveyor transports the mix to another mixer to verify batch sizes in the loss-in-weight process. Next, a horizontal flexible screw conveyor moves the dry mix to a final mixer for liquid addition.
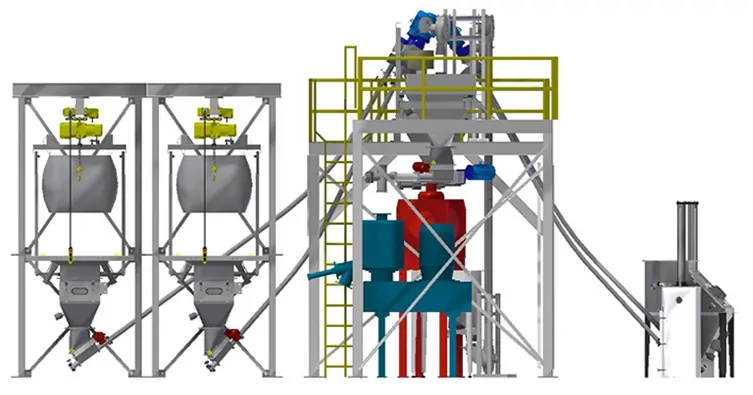
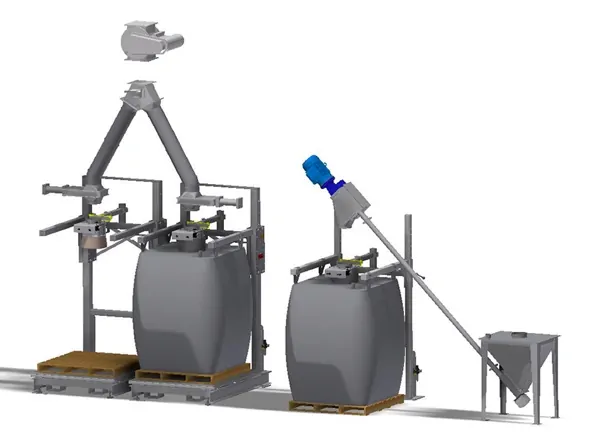
Gain-in-weight Bulk Bag Filling Systems
This setup, designed for a prominent carpet manufacturer, involves three bulk bag fillers for handling PVC flour dust. Above the fillers, a rotary airlock, diverter valve, and slide gate control the flow of PVC flour dust to a dual, gain-in-weight filling station. This station allows for efficient filling and quick bag changes, enhancing operator productivity.
An additional bulk bag filler manages PVC flour dust collected through a plant-wide dust collection system. It uses a flexible screw conveyor within a hopper, sourcing material from an external setup (not shown).
Invest in Our System Solutions and Elevate Your Operations
Spiroflow stands out as a leader in providing easy-to-use, effective belt conveyor system solutions and other equipment. We specialize in creating complete conveyor belt solutions that fit the specific needs of our clients. From food processing to chemical dosing and bulk bag filling, our systems are all about smart design and reliability.
At the core are our industrial conveyor systems, including both conveyor belt systems and wider industrial setups. These systems are crucial for smoothly blending ingredients in food production or handling precise measurements in chemical processes.
As one of the leading belt conveyor manufacturers, we know how important strong and reliable conveyor belts are for keeping operations running without a hitch. That’s why we focus on building durable, high-quality conveyor belt systems that you can depend on. Our filling and unloading solutions can automate your processes and elevate your operations while minimizing product damage and loss. With Spiroflow, you’re getting more than just a product. You’re gaining a partner committed to innovating and improving, ensuring that our solutions always meet the high standards our clients expect.
Need Assistance? Contact us today, we’ll return a response ASAP