C Series Bulk Bag Fillers
System OVerview
Overview of the C-Series Bulk Bag Fillers
Manufacturers worldwide rely on bulk bags for the packaging, storage, and transportation of materials. Spiroflow’s line of bulk bag-filling equipment and fillers is designed to enhance the safety, ease, control, containment, and cost-effectiveness of the bulk bag-filling process.
Spiroflow’s C-series bulk bag fillers offer a solution to the challenge of filling bulk bags. With options allowing simple volumetric filling, all the way to automated fill by weight capabilities.
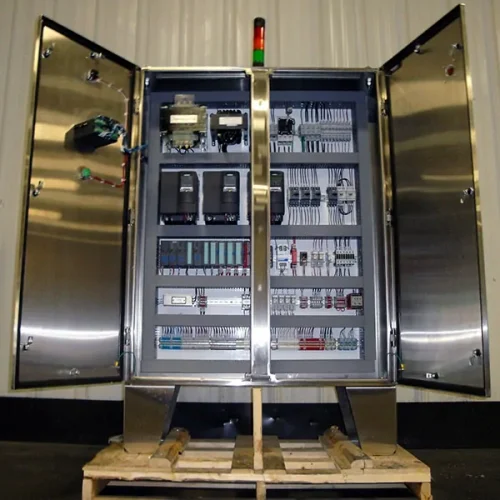
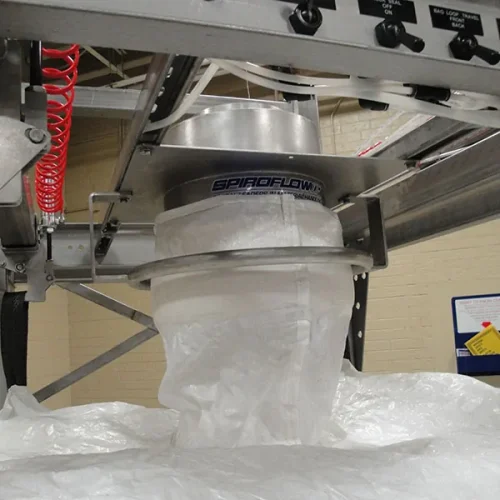
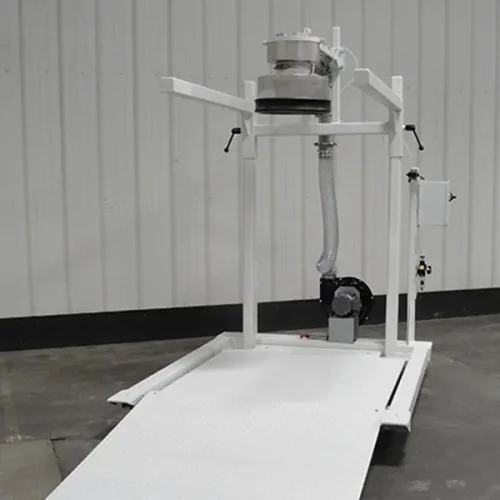
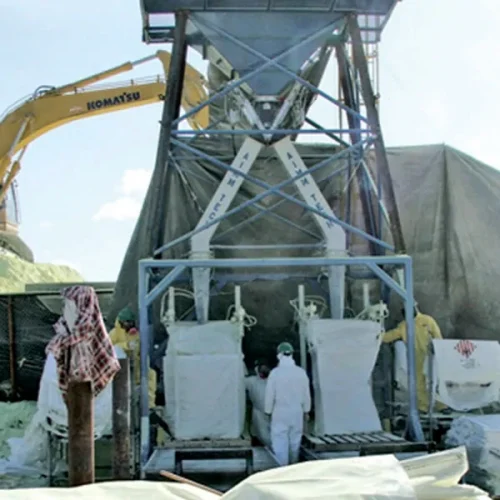
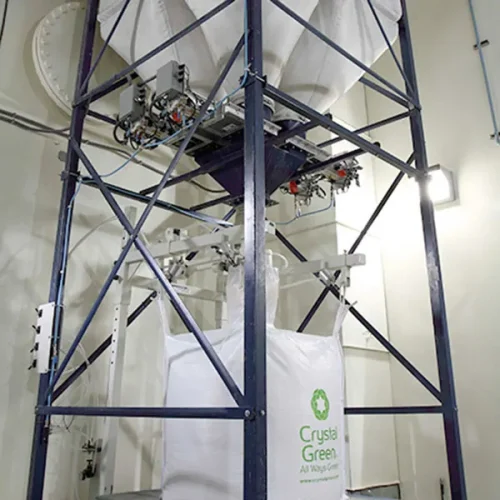
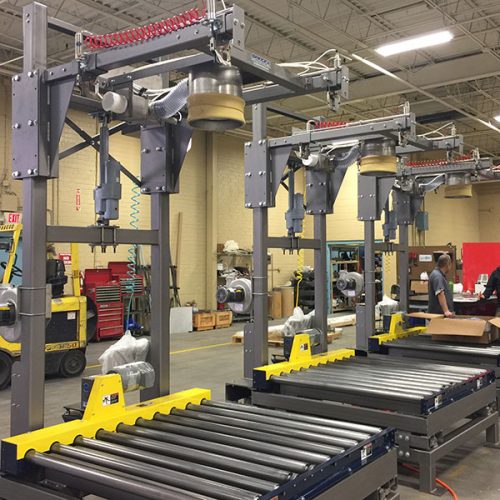
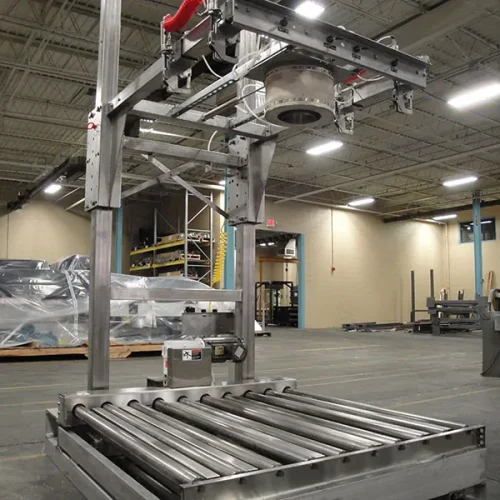
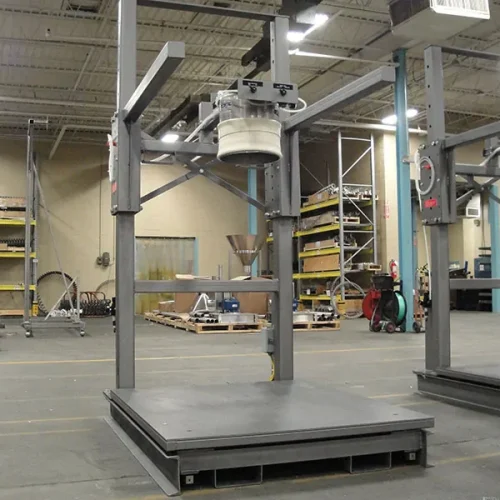
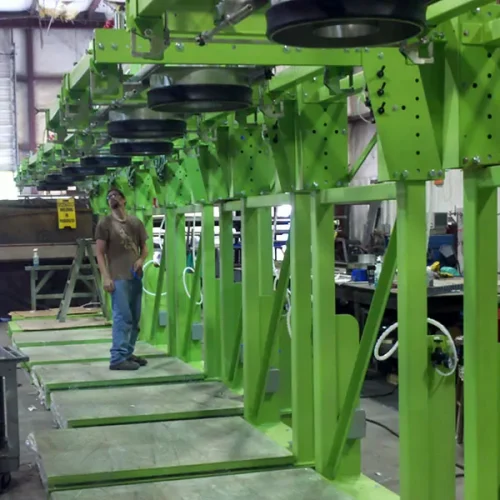
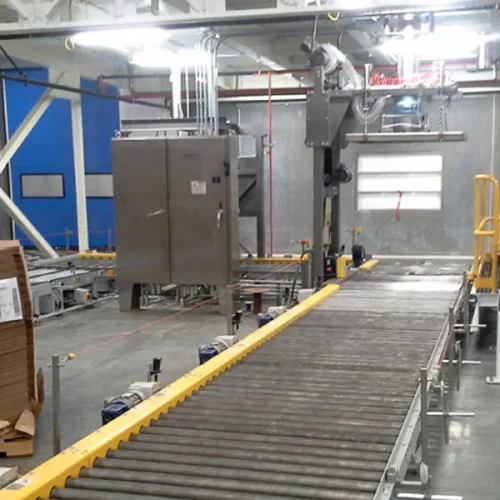
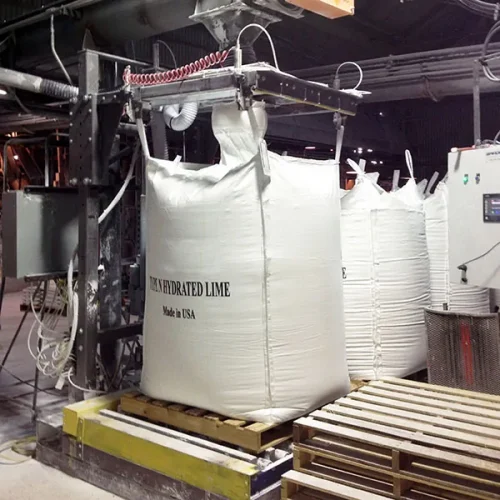
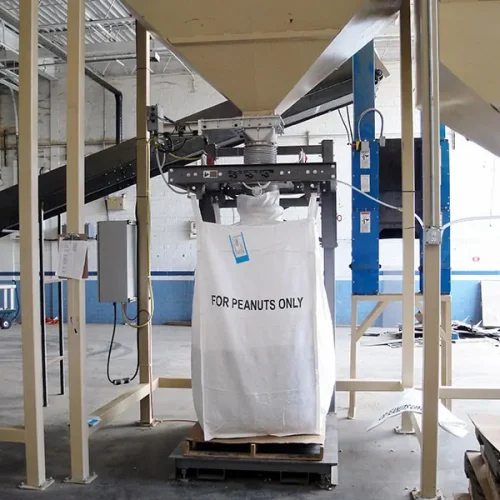
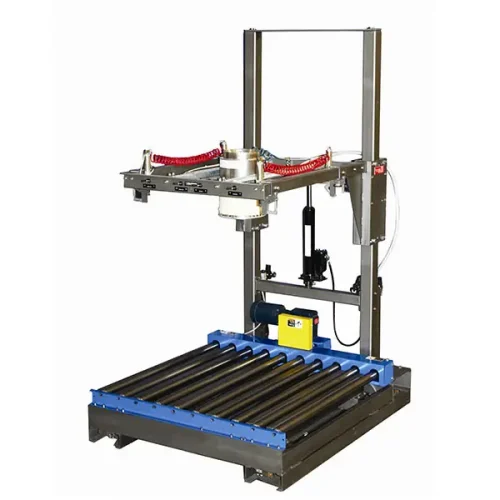
Explore All the Features of the Spiroflow C Series Bulk Bag Fillers
- Dust-free
- Total Containment
- NTEP Certified Load Cells & Controllers
- Forklift Bag Removal
- Pallet Truck Bag Removal
- Conveyor Bag Removal
- Low Headroom
- IBCs & Boxes/Octabins capability
- Semi-automated Filling Systems
- Nitrogen purging (optional)
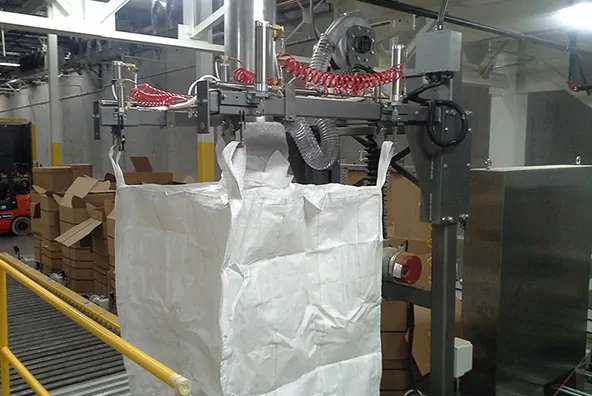
BULK BAG FILLER OPERATION SEQUENCE
The basic operational sequence unfolds as follows:
- Place the bag loops of empty bulk bags over the support arms or bag support hooks.
- Attach the bag spout or liner over the inflatable neck seal.
- Inflate the neck seal to secure the bag spout or liner.
- Inflate the bag or liner with air (optional).
- Commence filling by weight or volume.
- Apply vibration (optional).
- Remove the filled bag by stopping material flow, tying off the inlet spout, and removing the bag from the filler.
KEY FACTORS FOR SELECTING A
BULK BAG FILLING SOLUTION
Spiroflow’s bulk bag fillers are optionable for specific use cases. Below are questions to consider to help Spiroflow’s team pick the right filling solution.
To determine the appropriate bag style and size at this stage, it is advisable to consult both the bag manufacturer and Spiroflow. The bag should be optimized in terms of volume for safe storage and transportation. Spiroflow has achieved impressive results with Ameriglobe’s Fusion Baffle Bag, which is made without sewing and, in most cases, does not necessitate a liner.
To effectively control dust during the filling process, we employ an inflatable neck seal. All our filling heads are equipped with an inner product flow and an outer annulus for dust evacuation, as well as a dust port for connecting to additional dust collection equipment.
Spiroflow’s bulk bag filling equipment can be automated utilizing ease of bag rigging and conveyor takeaway options. Allowing operators to work more efficiently while bags are being filled and removed.
In cases where the environment poses an explosion risk, it is advisable to consider static dissipative or groundable bags along with a suitable static monitoring device.
Spiroflow’s bulk bag fillers can be optioned with a nitrogen purging system. To allow oxygen to be removed from the bag and extended product’s shelf life.
For very fine products, it is likely necessary to use a bag liner to prevent leakage or moisture ingress. However, there are various alternatives available, such as coated bags or specialized bag seams. Spiroflow’s bulk bag fillers utilize bag inflation options to ensure proper inflation of the liner to prevent creasing and subsequent discharge issues.
Spiroflow offers vibration on our bulk bag fillers to de-aerate light materials. Creating a tightly packed and stable bag. For even more challenging products, Spiroflow’s CTE system specializes in the de-aerating of bulk bags filled with light materials.
Spiroflow offers multiple options to increase the automation of the filling process. Such as automatic loop release and retracting support hooks to aid the operator in bag rigging. As well as, roller conveyors to bring in pallets and takeaway filled bags.
Spiroflow provides a range of options for filling rigid bins, drums, and boxes/octabins.
MODELS & SPECIFICATIONS
Our C Series gain-in-weight bulk bag fillers are available in a variety of configurations. Our models are as follows:
- Carbon/mild steel or stainless steel materials for construction
- Two post design – Two vertical tubes welded to a steel base plate,
- Filling nozzle and frame,
When filling by weight four (4) load cells mounted on a lower steel frame (200% overload capacity with 100% section capacity), NTEP rated & 5,000 Div. standard.
- Height – 110″/280cm,
- Width – 59″/150 cm + 14″/36 cm for control panel,
- Depth – 59″/150 cm.
*Filler height dependent on bag height
- 80 psi/5.5 bar @ 30 CFM (850 l/cycle) for inflatable neck seal & bag inflation options.
- Plant Voltage: 230/460/480/575
- Control Voltage: 24 V DC/120 AC
- Fill Nozzle with dust vent.
- The filling nozzle design includes an inner open-ended cylinder with a second concentric cylinder (one end closed by an annulus) attached to it, to allow air to escape during bag filling.
- The product passes through the center cylinder into the bulk bag while displaced air & dust are routed through the outer chamber and through a dust sock to a dust collection (by customer) connection.
- Optional pneumatic neck seal creates a seal between the fill nozzle and bag inlet spout.
CONFIGURATIONS
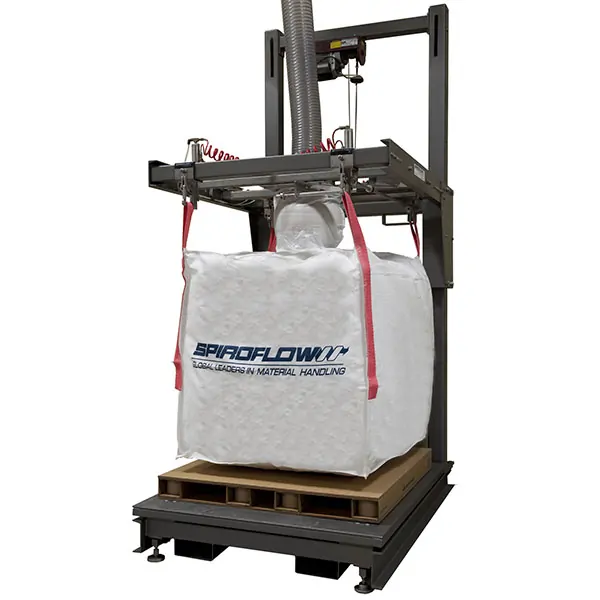
The C1-2 Gain-In-Weight bulk bag filler has a flat filling base with load cells under the filler feet for filling by weight applications.

The C1-2LL ‘low loading’ bulk bag filler uses an entrance ramp to allow fille bags to be removed by a pallet jack in low headroom areas.
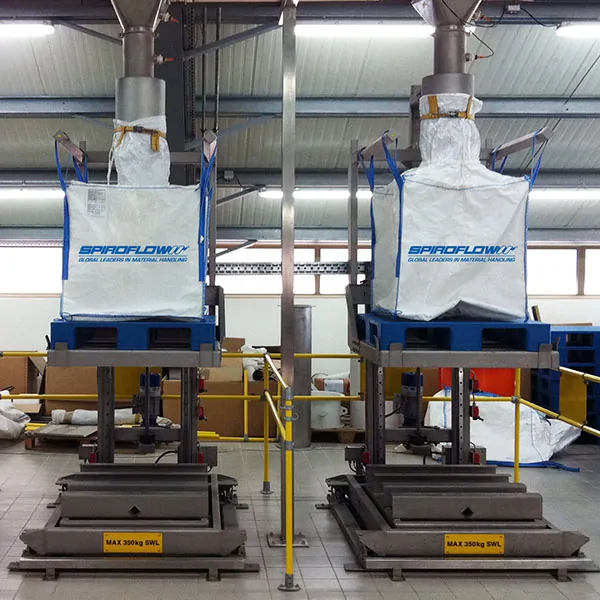
The C1-2RF ‘rise & fall’ bulk bag fillers are designed to minimize product breakage of friable materials, such as whole nuts.
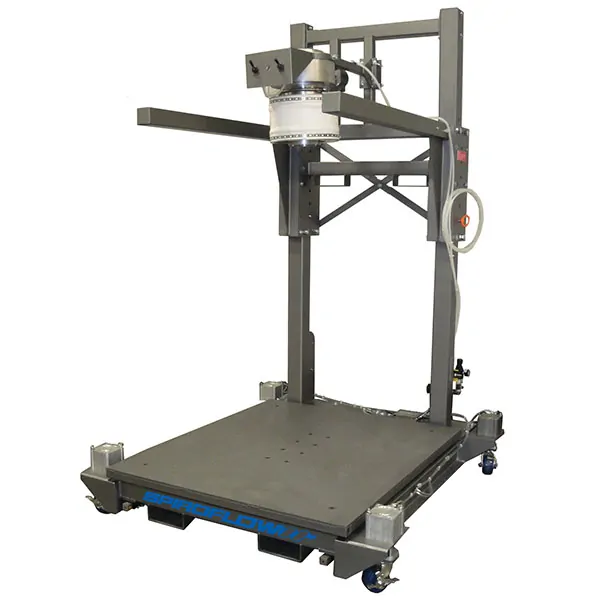
Mobile C1-2 filler uses caster wheels for mobility. and pneumatic lift cylinders to isolate load cells during bag filling.
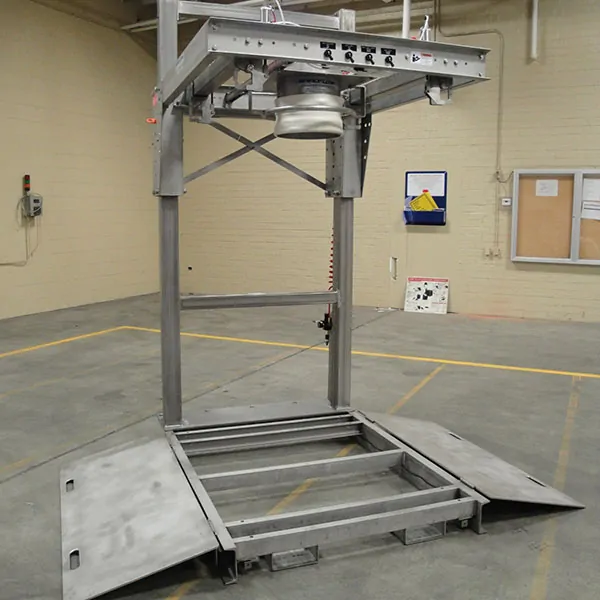
Spiroflow's bulk bag fillers can be designed with custom bases depending on the application.
BULK BAG FILLER OPTIONAL FEATURES
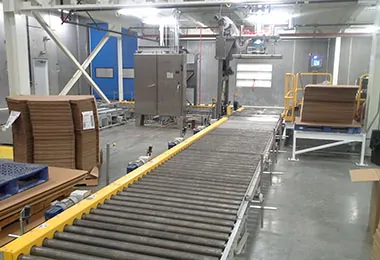
Roller Conveyors for Easy Bag Removal
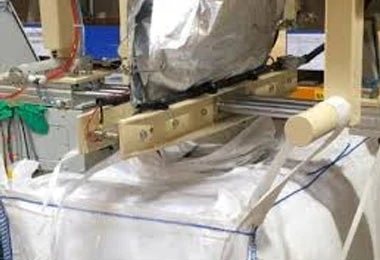
Nitrogen Purging and Heat Sealing
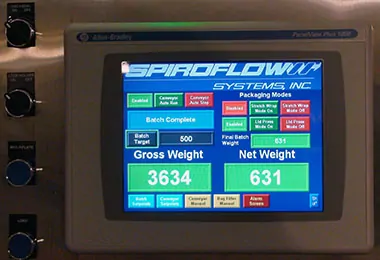
Full Management Data on Weight Controller
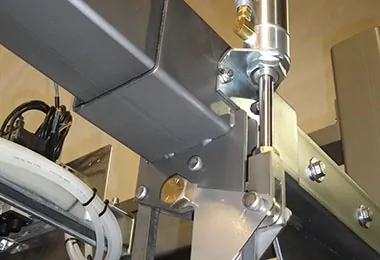
Automatic Bag Loop Release
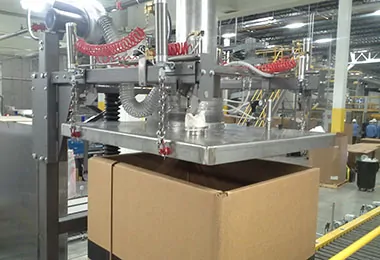
Box Filling Adaptor
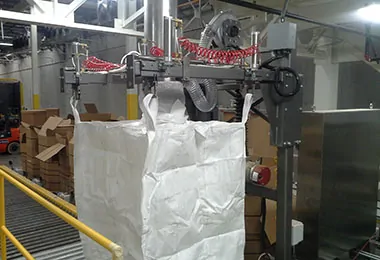
Automatic Height Adjustment
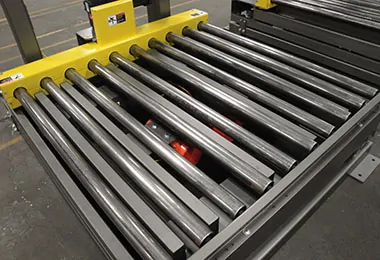
Roller conveyor Base with Vibration
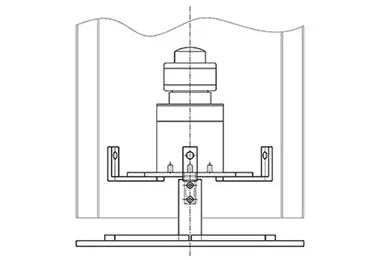
Spinning Head
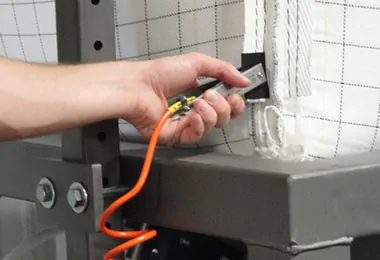
Static Grounding
There Is a Wide Range of Applications
Spiroflow’s bulk bag fillers are utilized in a variety of industries: Pharmaceutical, food, plastics, agriculture to name a few.
LARGE SCALE APPLICATIONS
Spiroflow bulk bag fillers were utilized in alaska to fill 27,000 bulk bags with 36,000 tons of material.
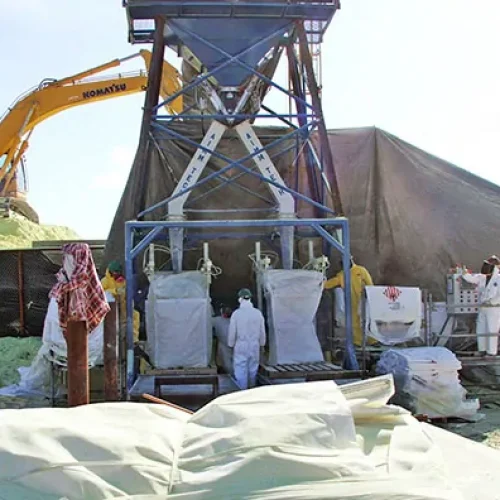
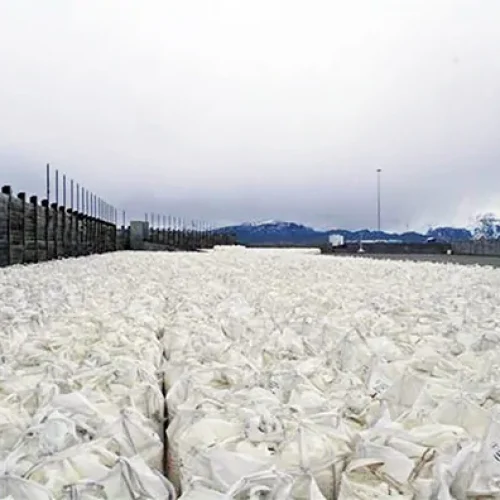
AUTOMATED FILLING APPLICATIONS
Optional automated filling features allow the bags to be filled quickly and efficiently. Reducing operator input and allowing improved employee safety and time utilization.
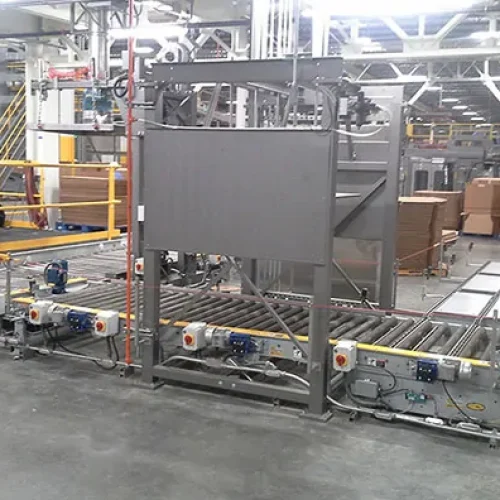
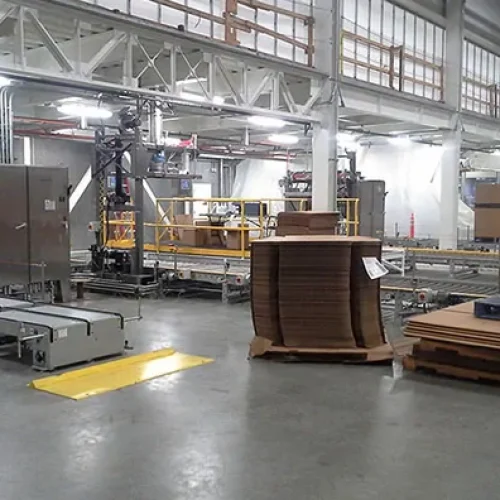
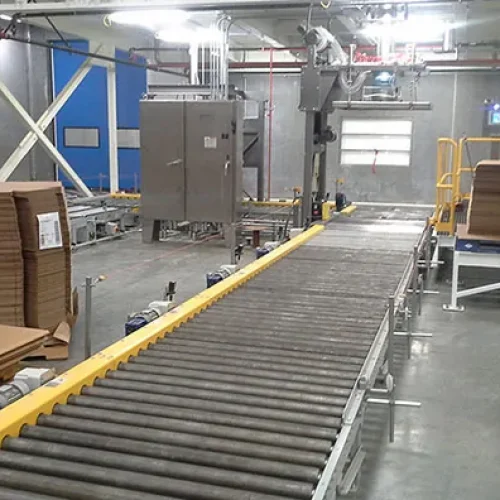
A semi-automated filling system gives large volume users the benefit of continuous operation without having to stop and unload each bag or gaylord. Pallets are automatically fed to the filling rig and the bags are looped onto pneumatically operated hooks. Once filling is completed, the loops are automatically released and the bag is then moved along the line by a powered take-off conveyor.