T3 Loss-in-weight Bulk Bag Unloader
System OVerview
In the world of industrial powder handling, efficiency, precision, and reliability are crucial. The T3 loss-in-weight bulk bag unloader is a confident solution, designed to elevate and streamline your bulk material handling processes. Whether you’re dealing with powders, granules, or other dry bulk materials, the T3 unloader can handle it with exceptional precision and efficiency.
The T3 Loss-in-Weight Bulk Bag Unloader utilizes load cells to allow precise control over product dispensing from the bag. That control can be adjusted for specific batch quantities or seamlessly integrated into your plant’s processing control for non-stop batch production.
The T3 Loss-in-Weight Bulk Bag Unloader builds upon the proven and tested features of our Universal T2 model by incorporating a bag support dish placed on four load cells. Spiroflow’s load cell placement under the support dish protects the cells from forklift and operator damage. Additionally, if needed, the integral transfer flexible screw conveyor can be suspended from the weighed frame, creating a fully self-contained discharge and loss-in-weight dispensing unit. Explore the efficiency and accuracy of our T3 Unloader for your bulk material handling needs.
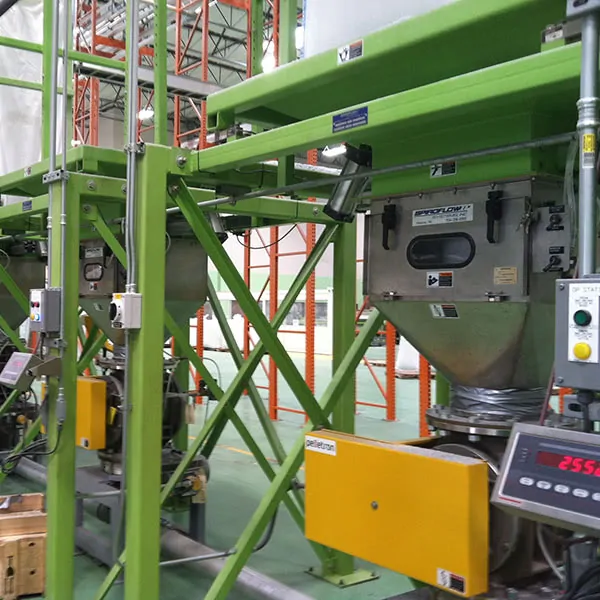
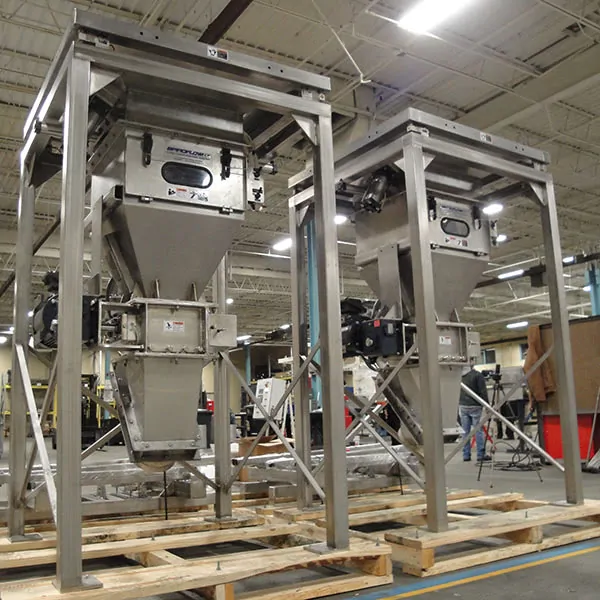
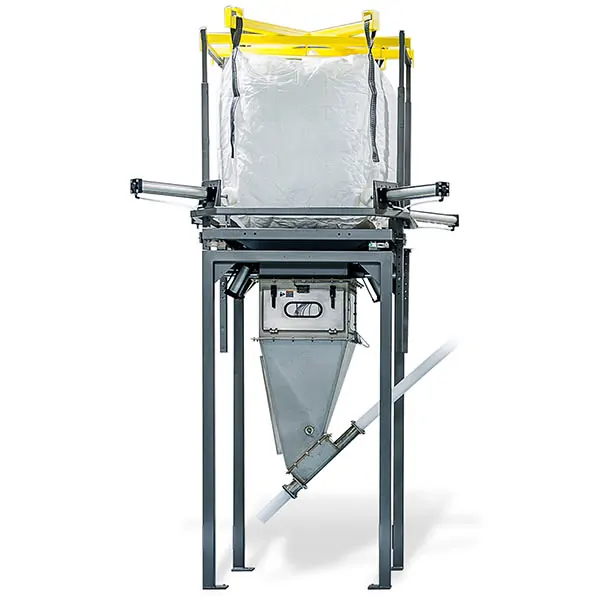
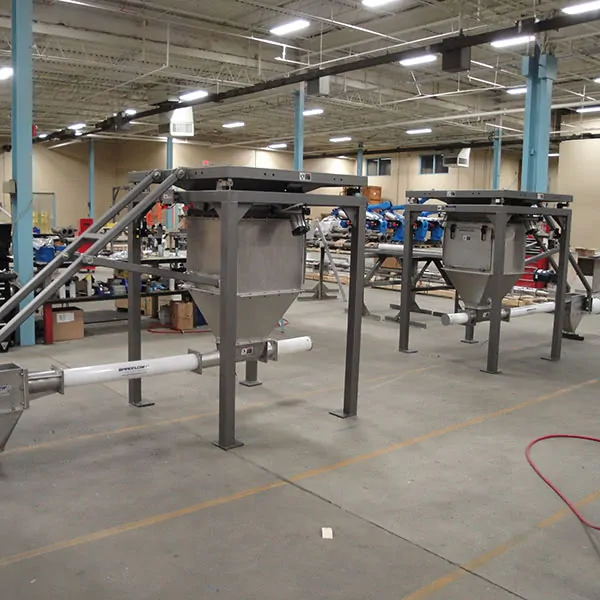
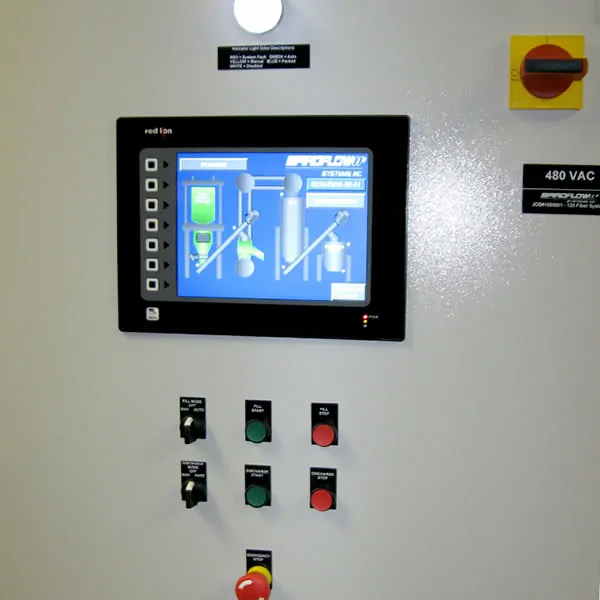
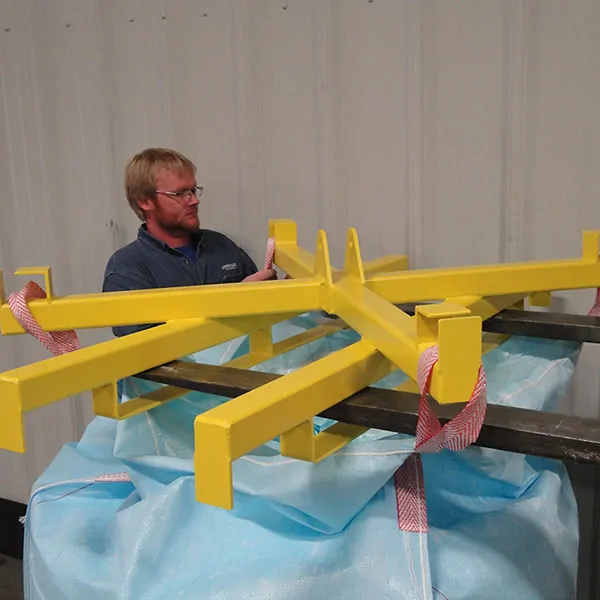
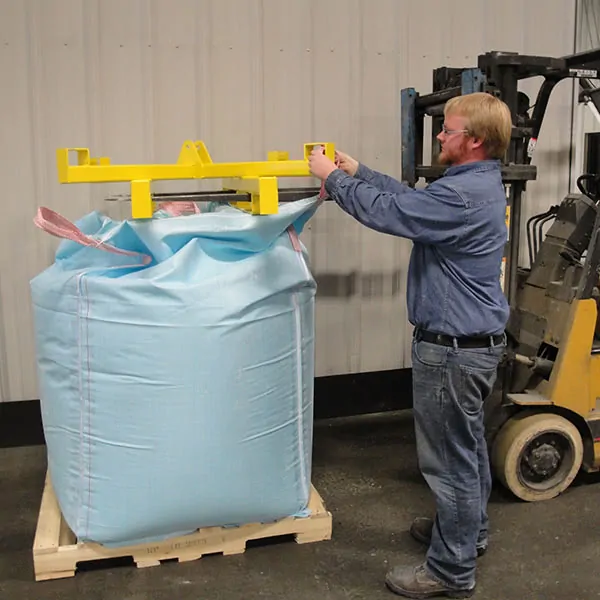
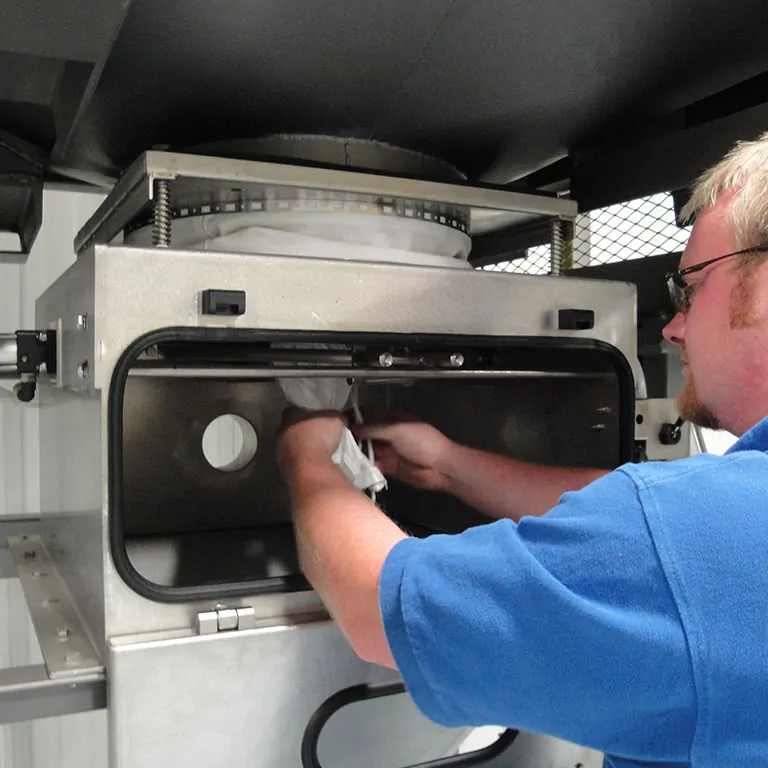
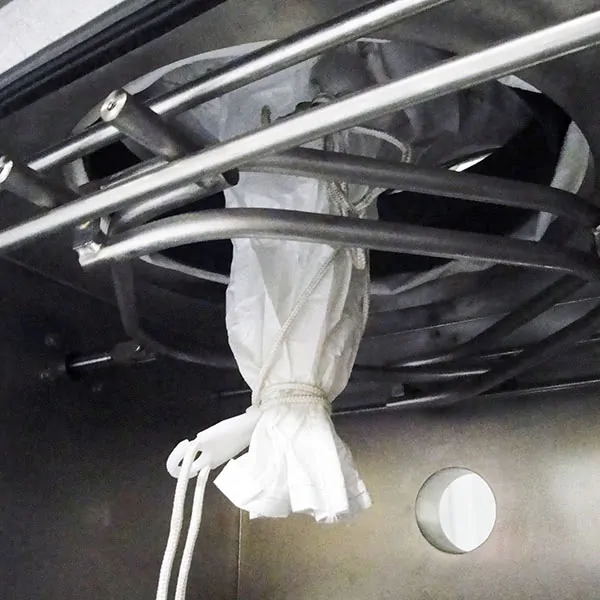

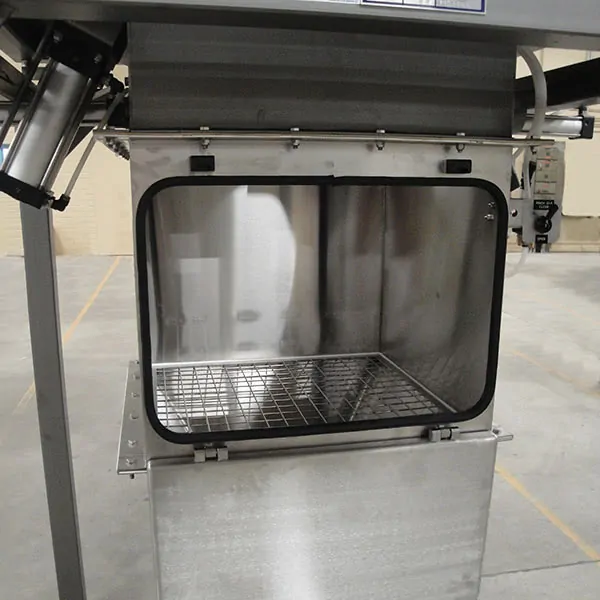
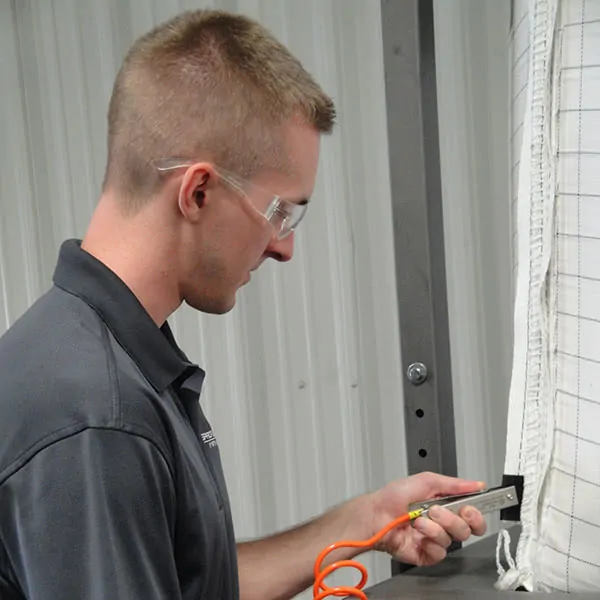
Features
- Dust-free
- All Bag Types
- Total Containment
- Controlled Dosing
- Batch or Continuous Weight Control
- Wide Range of Models & Accessories
HOW IT WORKS & BENEFITS
The T3 Loss-in-Weight Bulk Bag Unloader is your solution for precise weight-based unloading. It’s constructed with sturdy welded components, featuring a bag support dish designed to accommodate most bulk bags with bottom-spout. The bag’s spout passes through the center of the dish for easy access. Our innovative design places the four load cells and summing box in a protected high position on the frame, away from potential harm, water, and dirt. This ensures both safety and durability. Additionally, our bulk bag unloading system offers various control options to suit your needs, and the chute discharge is custom-tailored for your specific application.
Experience the reliability and versatility of the T3 Loss-in-Weight Bulk Bag Unloader for your weight-sensitive unloading requirements.
Operating our T3 bulk bag unloaders is straightforward and user-friendly. Here’s how it works: First, prepare the bulk bag by fitting it with the Bag Lifting Frame. Then, use a forklift to position the loaded bulk bag into place, where it rests on the Side Tensioning Frame with its weight compressing the springs, firmly supported by the Support Dish. The bottom spout is easily accessed with the bag securely in place. Open the access door, untie the bag spout, and commence unloading.
As the bulk bag empties, the side frame’s springs maintain constant tension on the bag to ensure complete material transfer. The discharged material flows smoothly into the chute. Once the bag is empty, simply re-tie the bottom bag spout, and you’re ready to remove both the bag and the lifting frame. Our T3 bulk bag unloaders simplify material handling, making it a seamless process for your operations.
Discover the Features
When it comes to efficient and versatile bulk material handling, our T3 bulk bag unloaders stand out. Here are some key features that set them apart:
- Batch or continuous weight control – Our unloaders offer the flexibility of batch or continuous weight control. The strategically placed load cells at the mid-section eliminate the risk of damage by forklifts and prevent dirt and debris accumulation, compared to units with load cells at the base.
- Recipe management system – Seamlessly manage your material handling with our recipe management system, ensuring precision and consistency.
- Bag tensioner – Ensures complete emptying of the bag, minimizing material waste.
- Integral conveyor or feeder – Choose the option that best suits your needs – an integral conveyor system or feeder – for efficient material transfer.
- Full dust control – Maintain a clean and safe work environment with our full dust control system.
- Designed for poor flowing materials – Our unloaders are engineered to handle even the most challenging materials, ensuring a smooth discharge process.
- Suitable for all bulk bag types and sizes – Whether you’re working with small or large bulk bags, our T3 bulk bag unloaders can handle it. They’re suitable for bags up to 6.5 feet (2 meters) in height and weighing up to 2 tons (1.8 tonnes).
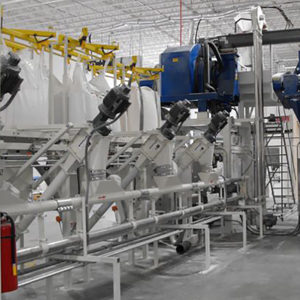
Using a forklift, the bulk bag is gently placed onto the bulk bag support frame. On this frame, spring-loaded arms slowly lift and maintain tension on the bag as it discharges its contents.
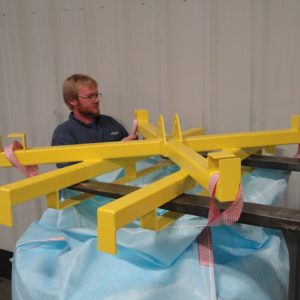
The bag loops are securely fastened to a bag lifting frame, and if there's a liner, it's firmly clamped in place for added stability and control.
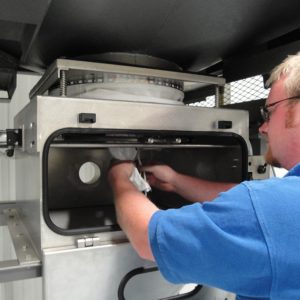
The integral chute's access door makes untying a hassle-free process. Additionally, our patented spout closure bars guarantee that the bag remains securely sealed until the discharge process is initiated, protecting operators during bag untying from falling material.

Pneumatic massage paddles aid in material discharge. Breaking up friable lumps and moving material towards the outlet spout of the bulk bag.
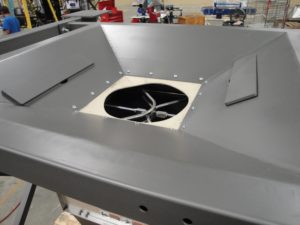
Spiroflow's rubber membrane dust seal contains any dust within the untie chamber and downstream process. Pneumatically actuated spout closure bars pinch the outlet spout during untying. Bottom massage paddles press into the bag to move material towards the outlet spout.
SPECIAL APPLICATIONS
While we offer a wide range of bulk bag unloaders, we also create custom equipment tailored to our customer’s unique needs. Here are some examples of our more unique designs:
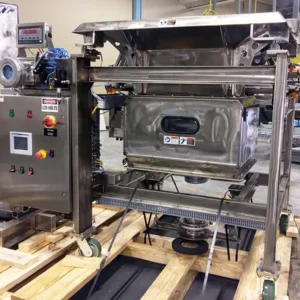
This explosion-proof T3 Loss-in-Weight Bulk Bag Unloader, ready for shipment, is built with stainless steel and boasts several custom-designed features.
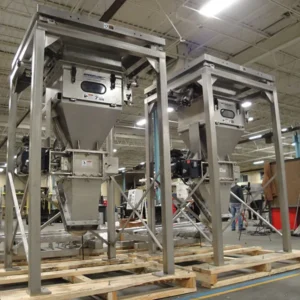
These exceptionally tall T3 Loss-in-Weight Bulk Bag Unloaders are set for shipping. Spiroflow can tailor bulk bag unloaders to meet any height requirement, ensuring flexibility to suit your specific needs.
COMPONENTS & OPTIONS
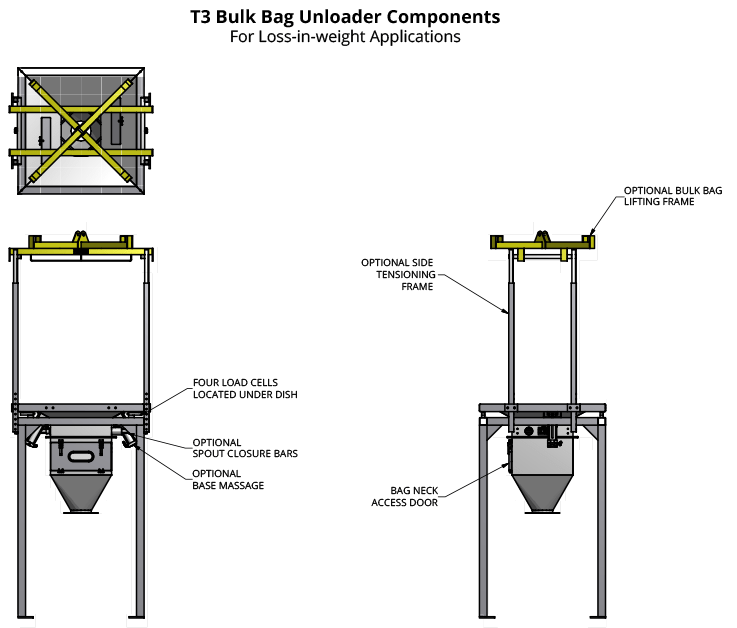
MODELS & SPECIFICATIONS
We offer a range of bulk bag unloader designs, including the T3 model. These models come with a variety of features that can be mixed and matched to suit your specific application requirements. We also specialize in building custom designs. Below, you’ll find a list of our basic models. Your Spiroflow Sales Engineer will assess your needs and recommend the ideal configuration to get the job done.
SPECIFICATIONS
STANDARD MATERIALS OF CONSTRUCTION
- Carbon/mild steel is standard.
- Optional 304 or 316 stainless steel is available.
PNEUMATIC REQUIREMENTS
- Side Massage: 80 PSI (5.5 Bar) at 2 CFM (56.6 L)/Cycle
- Corner Massage: 80 PSI (5.5 Bar) at 4 CFM (113.3 L)/Cycle
- Bottom/Dish Massage: 80 PSI (5.5 Bar) at 1 CFM (28 L)/Cycle
- Spout Closure Bars: 80 PSI (5.5 Bar) at 1 CFM (28 L)/Cycle
- Chute/Hopper Vibrator: 80 PSI (5.5 Bar) at 3 CFM (85 L)/Cycle
- Dust Collector: 80 PSI (5.5 Bar) at 35 CFM (991 L)/Cycle
ELECTRICAL REQUIREMENTS
- Optional Chute/Hopper Vibrator: 0.13 hp (.1 kW)
- Optional Hopper Agitator: 0.33 hp (.25 kW)
- Optional NEMA 4/ATEX Panel with ON/OFF Switch for Vibrator or Agitator: 0.33 hp (.25 kW)
- Optional Dust Collector: 1.5 hp (1.1 kW)
- Optional Level Probe: 24V DC
DUST CONTROL/AIR DISPLACEMENT
- Dust Extraction Port Optional Integrated
- Dust Collector: NEMA 4, TEFC (Stainless Steel Only)
- Optional Integrated Dust Collector: XP (Stainless Steel Only)
- Optional Free-Standing Dust Collector: NEMA 4, TEFC (Stainless Steel Only)
CONTROLS
Our T3 bulk bag unloaders offer control options with or without a VFD. You can also get motor starter controls for operating a dish vibrator, hopper agitator, or dust collector. And if you need full loss-in-weight, weight display, or batching controls, those are available too. Just share your control requirements with your sales engineer for detailed specifications.