Customer Requirements
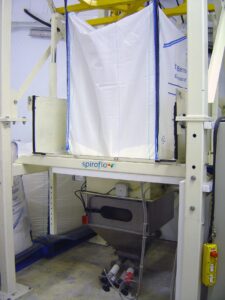
A leading dairy company producing an anhydrous milk fat blend with sugar for ice cream, chocolate and other confectionery applications, had a need to unload sugar from 1,000 bulk bags and then transfer the sugar to a blending area.
Spiroflow Solution
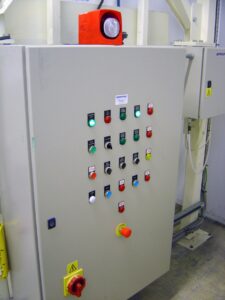
– Granulated sugar is received in 2,200lb/ 1000kg bulk bags.
– The Bulk Bag Unloader is housed within a sugar storage area.
– Bulk bags are placed in front of the unloader by pallet truck.
– The bag loops are attached to a lifting frame at floor level and then the bulk bag is raised into place onto the unloader via a traveling hoist mounted on an integral runway beam.
– The bulk bag sits on a flexible membrane which acts as a seal and two pneumatically operated, opposing pinch bars located within the discharge hopper clamp the neck of the bulk bag.
– This allows the neck to be untied in complete safety through an interlocked access floor in the side of the hopper.
– Once this access door is locked shut the pinch bars can be released to allow the sugar to unload into the hopper.
– Since the sugar is free flowing, no mechanical assistance is needed to aid the complete discharge of the bulk bags.
– It is dust-free – essential to meet this customer’s high hygiene standards.
– Sugar is transferred from the Bulk Bag Unloader hopper up to two load cell mounted dispensing heads with two Spiroflow Flexible Screw Conveyors, each 55’/ 17m long.
– The two conveyors operate independently to replenish their associated dispensing head hoppers as soon as the dispensing cycle is completed.
– The conveyors are driven by inverters allowing a combination of fast fill as well as trickle feed to ensure that each dispenser hopper is filled to the target weight.
– The system is designed to go into “hold” mode each time a bulk bag is emptied and level indicators within the discharger hopper cause an alarm to sound when this is about to happen.
– This enables a replacement to be readied in time for a swift change over – then the control system restarts the conveyors automatically to complete any interrupted batch.
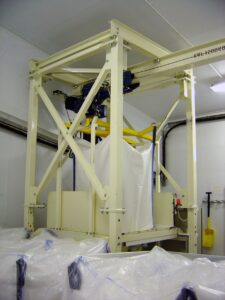