Customer Requirements
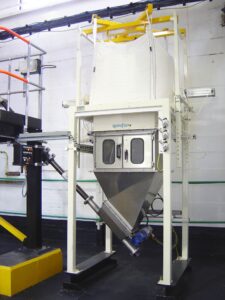
Innospec is a global chemicals company with 1,000 employees in 23 countries. They divide their operations into three distinct business areas: Fuel Specialties, Active Chemicals and Octane Additives.
The Active Chemicals business includes a company based at Ellesmere Port, UK, which produces chemicals used in the manufacture of personal care products. These products are for the European market and needed a manufacturing plant that replicated their US plant.
– The main ingredient of the product is delivered in bulk bags.
– For each batch, several bags are charged into the process reactor together with a catalyst from 55lb/ 25kg bags.
– The UK plant was built on a tight budget so the Aero Mechanical Conveyor used in the US was put under particular scrutiny.
– The plant at Innospec is designated a European gas zone 2 / dust zone 22 hazardous area. Being competent with European ATEX/DSEAR hazardous area regulations, Spiroflow had no difficulty in meeting Innospec’s requirements.
Spiroflow Solutions
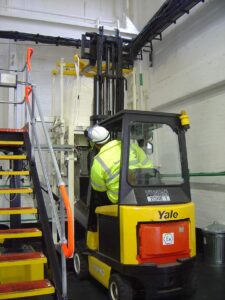
We supplied a Bulk Bag Unloader with integral Flexible Screw Conveyor as the means of charging the reactor.
– The 55lb/ 25kg bags of catalyst are manually added through the access doors.
– The bags sit on a support dish and the outlet spout passes through a flexible membrane – this forms a dust-tight seal.
– The bag neck is pulled down via the doors in the dust-tight cabinet.
– With the doors closed pneumatic spout closure bars pinch the bag spout above the tie point.
– The interlocked doors are opened and the operator can untie the spout.
– The cabinet doors are then re-closed, the spout closure bars are opened and product flows into the collection hopper below without dust escaping.
– Given that the reactor reaches temperatures of 570°F/ 300°C the flexible connection is simply disconnected and reconnected as required so that the reactor inlet can be closed by a pressure tight hatch once the reactor has been charged.
-The main control panel is mounted remotely outside of the building with a zone rated local control panel adjacent to the Unloader.
Why Choose Flexible Screw Conveyors?
Bill Swift, Corporate Projects Manager commented, “We are well satisfied with our Spiroflow Bulk Bag Unloader and the Flexible Screw Conveyor, it has proven to be very efficient.” He was convinced after spending the day at our UK test facility watching the Flexible Screw Conveyors at work.