SUGAR CONVEYING CHALLENGES: GRANULATED VS. POWDERED SUGAR
Powdered sugar is highly flammable and explosive. Sugar conveying system design should work to eliminate this risk. In fact, due to recent industrial accidents, government regulatory bodies like OSHA (Occupational Safety and Health Administration) and NFPA (National Fire Protection Association) have issued heightened regulations governing the handling of sugar. In addition, these agencies have labeled sugar processing facilities high risk.
Furthermore, powdered sugar tends to pack and cake as it is conveyed. Flow aids should be considered as part of the conveying system to help with discharging.
Granulated sugar, on the other hand, is abrasive. The sugar conveying system design should be able to withstand the wear of the sugar against its sides.
Like powdered sugar, granulated sugar is highly combustible, potentially explosive and will ignite at high temperatures. Conveyor design should prevent dust emissions and static buildup, and eliminate possible sources of ignition.
Finally, granulated sugar is a hygroscopic material, meaning it easily absorbs moisture. Conveyor system flow aids are usually necessary to ensure complete discharge of the sugar from the conveying system.
IDEAL SUGAR CONVEYORS AND CONVEYING SOLUTIONS
Aeromechanical Conveyors
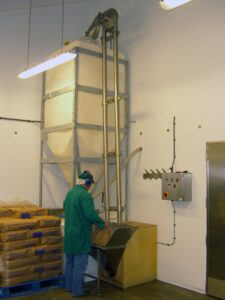
The totally-enclosed aeromechanical conveyor is an ideal choice for conveying large volumes of both powdered and granulated sugar. Any dust created during conveying is contained within the conveyor, reducing the risk of explosions caused by static build up and sugar dust clouds.
In addition to being airtight, it runs quietly and with minimal energy.
Aeromechanical conveyors can be easily disassembled for regular, quick cleaning. This is essential for sugar, which is both prone to caking and build-up and often food product-bound.
Flexible Screw Conveyors
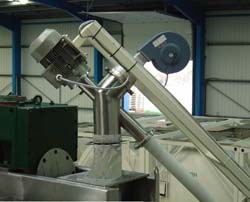
The flexible screw conveyor (FSC) is ideal for conveying batches of sugar.
The flexible screw works well with combustible materials as it is always full of product, preventing an explosive atmosphere. A flexible screw conveyor can come with a reverse bung, drop out tray and quick release flanges for best-in-class hygiene and cleaning and will help avoid cross-contamination when changing batches. Watch our video about hygienic flexible screw conveying and how it could benefit your sugar conveying process.
Additionally, the flexible screw’s spiral constantly remixes sugar as it conveys to maintain product integrity. Some over-the-counter health products are mixtures of very fine active components mixed with a coarse grade of sugar. To ensure every sachet is the same, many health product packing lines use FSCs as the final conveying technology so that every packet contains the same formulation.
Flexible screw conveyors conveying sugar should be constructed from materials that can stand up to the abrasion. Heavy-duty spirals are available and, in extreme cases, double wind spirals can be used. We often recommend stainless steel or rubber Rhinoveyor tubing as more wear resistant options over the standard UHMWPE tube. An undersized screw can also be placed in a conveyor to reduce tube wear. This allows more clearance between the spiral and tube allowing the material to act as a buffer between the two.
Support For Your Sugar Conveying System
Interested in how we can help reduce manual handling and increase the efficiency of your sugar conveying and processing system? Contact our Spiroflow engineers today.