In managing and controlling dust in your bulk bag filling operation, ensuring product transfer from processing, storage, or conveying systems into packages without productivity loss is crucial. This involves meticulous design choices in bulk bags and the integration of sophisticated bulk bag filling equipment to contain dust effectively, ensuring a seamless transition and minimal environmental impact.
Controlling Dust in Your Bulk Bag Filling Operation – How Do You Ensure Your Filling System Doesn’t Emit Dust?
Packaging any dry bulk solid material involves the transfer of product from the end of the process, storage, or conveying system to the package. At that transition point, depending on the material and other factors, dust emissions can occur. How do you ensure that your bulk bag filling system doesn’t emit dust and become a productivity and profit drain? Controlling dust in your packaging operation involves bulk bag design as well as expert bulk bag filling equipment design.
Bulk Bag Design #1
Unless a bulk bag has been specifically designed to contain the fines present in your product, particles can sift through the bag fabric as the bag is being filled. This looks like smoke escaping from the bag seams or fabric as the product enters the bag.
Depending on the amount of fines present in the product, the particle size, and its shape, coated fabric may be all that is required to contain the dust. However, in some cases, polyethylene liners are required to prevent product sifting.
Bulk Bag Design #2
Bulk bags come in many styles. Most have a top panel where a cylindrical inlet spout is sewn. Others have duffle-style tops that expose the entire top of the bag to the atmosphere. However, it’s important to note that easily aerated products should never be filled into open-top bulk bags.
While there are ‘area extraction’ dust collection systems that are designed to work in relative proximity to a source of dust emissions, they are virtually never consistently effective. That’s why there’s a rule of thumb – use inlet-spouted bags for dusty products.
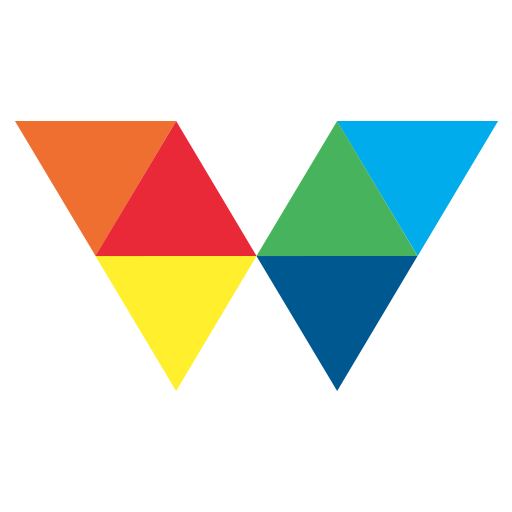
Connecting the Bulk Bag to the Upstream Process
The connection between the bulk bag’s inlet spout and the tube or cylinder through which the product flows must be secure and dust-tight. There are a few workable conveyor solutions where the inlet spout is strapped to the tube with a bungee cord or some variation of a circular clamp.
However, this often results in the inlet spout being bunched up around the tube, thereby creating channels for air and dust to escape. It’s recommended to use a fill tube with an inflatable collar that expands to securely hold the inlet spout and, in so doing, provide a seamless, dust-tight connection.
What Happens to the Air From the Bulk Bag?
Empty bulk bags contain the air in an amount equal to their volume. Your 50 ft3 bulk bag that is now rigged and ready to be filled contains 50 ft3 of air. So, what happens to that air as it’s being filled? For every increment of product volume that enters the bag, an equal volume of air leaves, or is displaced, from the bag. If that air contains dust particles, there is a constant stream of dust-laden air that must find its way out of the bulk bag as it is being filled.
Where Does the Air Go?
Unless your industrial conveyor systems are specifically designed to deal with displaced air, it will escape – but not in a good way. The choices for trapped air are to filter out of the bag or to find an opening in the upstream connections to the atmosphere. To properly contain dust, your bulk bag filler MUST have a twin-tube bulk bag fill head that features an inner cylinder where the product flows into the bag.
It also needs to have an outer concentric cylinder that forms an open ring or annular gap around the inner tube. The outer tube has a dust vent that is connected to a dust collection system that provides the required amount of vacuum to extract the dust-laden, displaced air through the annular gap.
What Happens When the Bag Is Filled?
Your bulk bag is filled to its target weight, and you are ready to disconnect the inlet from the fill tube. Is there anything you should worry about at this point? Unfortunately, a complication can still occur. If your product is an explosion hazard, dust particles may be emitted from the inner surface of the fill tube and the inlet spout as the bag is disengaged.
In this case, a specialized dust containment chamber that encloses the fill tube and inlet spout area can be incorporated. It’s maintained under negative pressure relative to the atmosphere. The operator accesses the interior of the chamber through flexible ‘letter’ slots. As the spout is released from the fill tube and tied by the operator within the chamber, any dust particles emitted are extracted. This provides an extremely high level of dust containment.
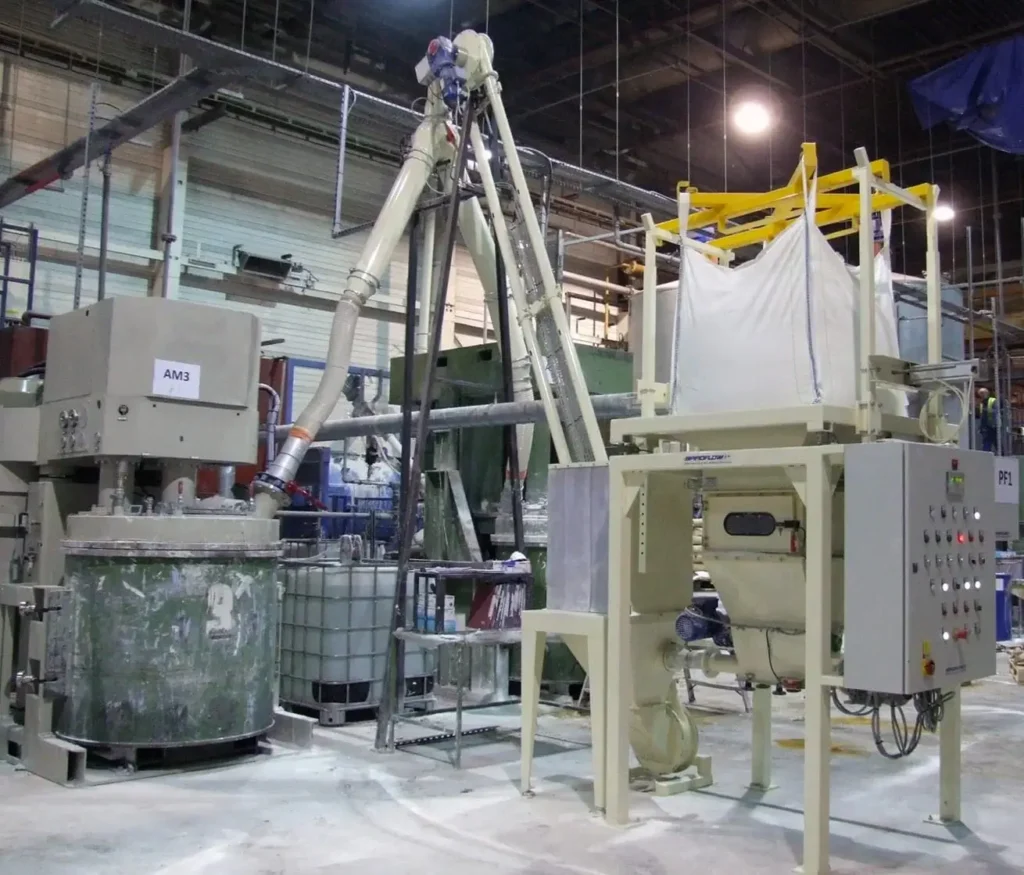
Elevate Your Dust Handling in Bulk Bag Filling Operations With Spiroflow
For over 45 years, Spiroflow has been setting the benchmark in powder handling and dry solids processing, alongside excelling in control systems integration. Our pioneering conveyor technologies, including the revolutionary flexible screw conveyor, conveyor belt system, and a broad spectrum of other mechanical conveyor solutions, have positioned us as industry leaders.
We offer a wide array of products from Aeroflow® aero mechanical and Cablevey® cable drag to Dynaflow® chain drag conveyors, and an extensive Spirofil® range that encompasses everything from bulk bag fillers to custom-designed hoppers.
At Spiroflow, we are committed to engineering solutions that precisely meet your unique challenges, ensuring the safety, efficiency, innovation, and reliability of your process solutions. Contact us today to transcend your handling and processing challenges with our tailor-made, cutting-edge systems. Let us help you achieve unparalleled results with our objective, expert evaluations, and engineered solutions.
FAQ
How Do You Prevent Dust Emissions in Bulk Bag Filling Operations?
To prevent dust emissions, it’s crucial to use bulk bags specifically designed to contain fine particles, potentially using coated fabric or polyethylene liners. Employing bulk bags with inlet spouts rather than open tops is recommended for dusty products to minimize exposure to the atmosphere. Additionally, ensuring a dust-tight connection between the bulk bag’s inlet spout and the product’s conveyance system, preferably using a fill tube with an inflatable collar, is essential for controlling dust emissions effectively.
What Role Does Bulk Bag Design Play in Controlling Dust?
Bulk bag design is pivotal in controlling dust – choosing the right type of bag can significantly reduce dust emissions. Bags with cylindrical inlet spouts or those that use specific fabrics or liners to prevent product sifting are ideal. Open-top bags should be avoided for easily aerated products, and coated fabric or liners are recommended depending on the fines present in the product.
How Is Displaced Air Handled During Bulk Bag Filling?
Displaced air, potentially containing dust particles, must be managed to prevent emissions. The bulk bag filler should feature a dual-tube design with an inner cylinder for product flow and an outer cylinder with a dust vent connected to a dust collection system. This setup allows the vacuum to extract dust-laden air, efficiently managing displaced air and controlling dust.
What Happens When the Bulk Bag Is Filled?
Upon reaching the target weight, disconnecting the bag can pose a risk of dust emission, especially with explosive materials. A dust containment chamber with negative pressure can encase the fill tube and inlet spout area, ensuring any released dust particles are extracted. This method significantly enhances dust containment when disconnecting the filled bag.
Why Choose Spiroflow for Bulk Bag Filling Dust Control?
Spiroflow stands out for our 45-year legacy in powder handling and dry solids processing, offering innovative conveyor technologies and stellar solutions, from bulk bag fillers to custom-designed hoppers. Our commitment to engineering tailored solutions ensures efficient, safe, and reliable operations, making us a top choice for overcoming dust control challenges in bulk bag filling operations.