Dust containment for bulk bagging is a primary concern for many customers when conveying their products. The consequences of not addressing this issue can be severe, ranging from fire and explosion hazards to unexpected downtime and difficulties in cleaning.
Implementing effective dust containment measures can improve manual handling efficiency and reduce the amount of product lost to the air. Check out how our industrial conveyor systems and other solutions helped a pharmaceutical company eliminate dust and streamline material handling.
Dust is a Health and Safety Issue
Dust is a serious health and safety issue in the workplace. Employees exposed to dust can experience immediate effects such as eye irritation, headaches, coughing, and sneezing. Prolonged exposure to poor indoor air quality can also lead to serious long-term health effects and lower employee performance, resulting in prolonged absences. Using dust-tight conveying and bulk bagging equipment is crucial in improving air quality, especially for products prone to dusting challenges.
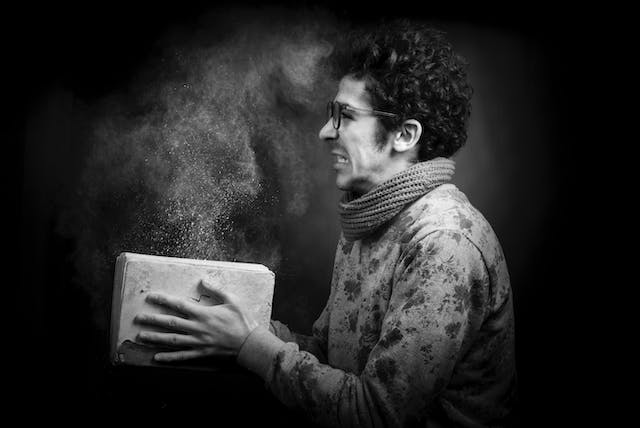
What Causes Dust Containment Issues?
Dust containment is a critical consideration in industrial processes, especially when handling bulk materials. Proper dust management not only ensures a clean and safe working environment but also complies with health and safety regulations. Understanding the causes of dust containment issues is the first step toward implementing effective control measures. Below are key factors contributing to dust containment challenges:
- Bulk bags must be designed specifically for dust containment to prevent dust emissions. Without proper containment, particles can escape through the bag’s fabric, creating the appearance of smoke.
- The release of the outlet spout during the start of product flow can cause dust emissions. Spiroflow’s bulk bag unloader must handle the sudden rush of material during the closed phase to prevent the updraft of dust-laden air. Proper extraction is essential to prevent dust release into the atmosphere.
- Your bulk bag unloader must maintain dust extraction during the entire discharge cycle. You want to ensure no movement compromises the seal required for proper dust containment.
- Dust can still be present in an ’empty’ bulk bag. If the outlet spout is not re-tied, dust-laden air will escape into the plant area during disposal. Be careful when handling the empty bag to prevent folding or compressing, which can release dust-laden air. Use a suitable Standard Operating Procedure, and consider using purpose-built bulk bag folders to make the process dust-free. Your bulk bag unloader should support your SOP.
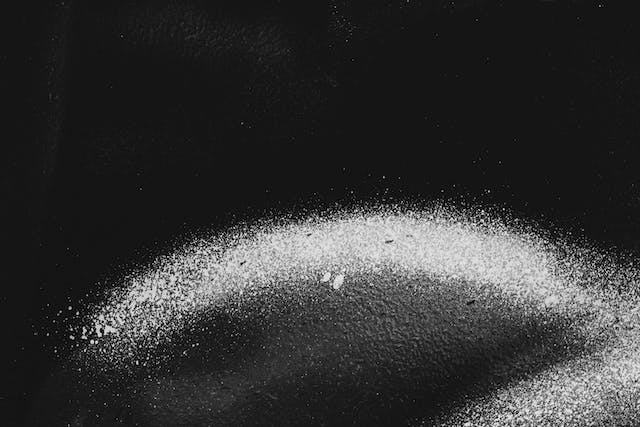
How Can We Overcome These Dust Containment Issues?
Implementing effective dust control measures in industrial environments is crucial for maintaining a clean and safe workspace. This is particularly important in processes involving the handling and unloading of bulk materials, where the risk of dust emissions is high. To ensure maximum dust containment and compliance with health and safety regulations, several key strategies can be adopted.
Material Testing
To ensure that the unloader suits your application, ask the supplier to test your item on the machinery, specifically focusing on dust control and containment capabilities. Learn more about Spiroflow’s testing facilities.
Design of Bulk Bags
Selecting bulk bags correctly is essential for containing dust during the unloading process. Liners made of polyethylene or coated fabric can avoid sorting products, and inlet-spouted bags should used for dusty materials.
Complete Dust Collecting
Unloaders for bulk bags can be built with ports to connect to a factory-wide system for the discharge of dusty materials, or they can be built with integrated dust collection systems. Learn more about dust control.
Dust Bag Seating
Unwanted material dusting may occur when a filled bulk bag is installed in the unloader’s frame. Dusting can be considerably reduced with the unloader’s base equipped with a dust-tight docking seal. Learn more about how we design our dust bags with a docking seal.
Tensioning of Bulk Bags
To empty every bag completely and avoid residual material causing dusting and spilling when taking out the bags, the liner and bulk bag must be tensioned correctly.
Closed Access Area
Approximately 50% of spills and dusting happen when the spout is being untied. Dusting problems can be reduced and spills can be contained by enclosing access to the spout area and maintaining a modest negative pressure. When applying the glove box layout, dangerous materials should be taken into account.
Docking of Sanitary Spouts
Good spout docking configurations ensure total containment of the product and efficient stretching of the bag. Such a design solution can be used with or without an access chamber.
“Empty” Bulk Bag Elimination
To avoid dusting, the spout must be securely tied off before the bag is removed. The surroundings can be free of suspended dust by utilizing a “bag collapsing” feature that uses a dust collector to release the bag. Learn more about how we installed a bulk bag unloader for an adhesives company to help reduce dust emissions.
Optimization of Downstream Processes
It’s critical to provide the operator with enough time to complete every step of the bag-emptying procedure. Throughout the process, strategically placed time buffers can reduce downtime and enable dust-free operation.
Dust Containment for Bulk Bagging
We are conveyor systems manufacturers that provide various dust control options for our conveyor belt solutions and other equipment. This includes dust-tight mechanical conveyors such as the Cablevey tubular drag conveyor belt system, aero-mechanical conveyor, and our innovative flexible screw conveyor. Our mechanical conveyor comparison chart can help you choose the best conveyor for your product, or you can contact us to discuss your needs and other conveyor technologies.