CTE Bulk Bag Fillers
System OVerview
Spiroflow’s CTE Bulk Bag Filler utilizes patented cone table densification to improve bag fill and throughput. With a hanging weight load cell design for accurate filled bag weights. The CTE quickly and efficiently fills bulk bags with material.
Ideal for highly aerated materials, the CTE’s filling and densification process produces full and stable bags. Allowing bag stacking, as well as overall bag height reduction. This leads to less wasted bag space and a reduction in the number of bags needed.
Available automation options allow for the most bags per hour rate out of our bulk bag filler line.

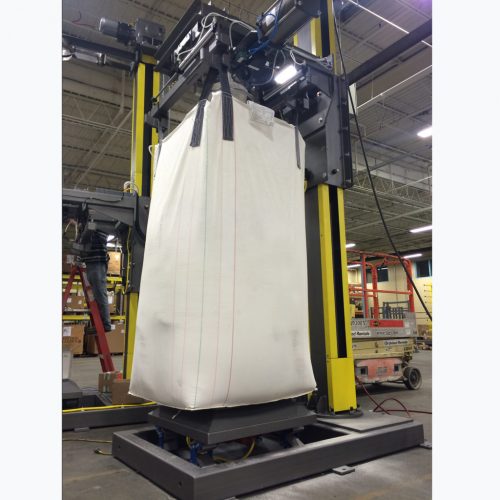
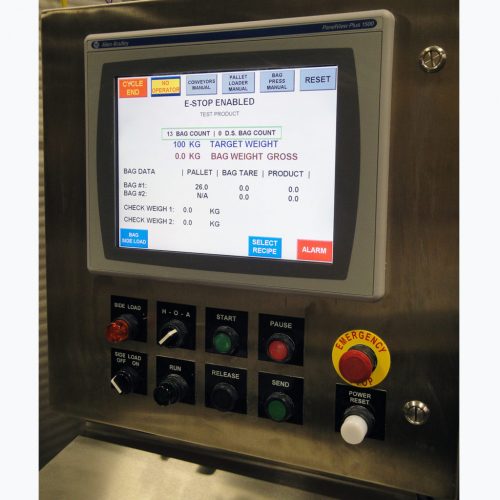
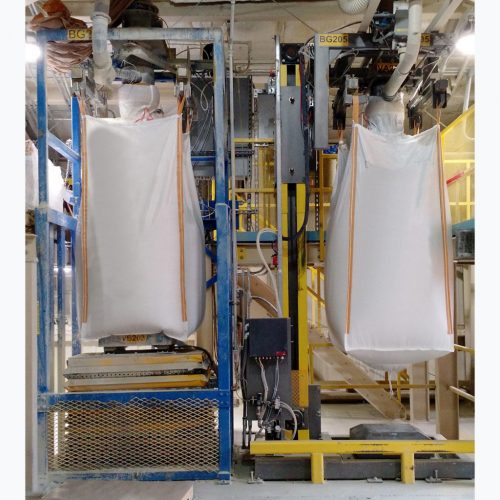
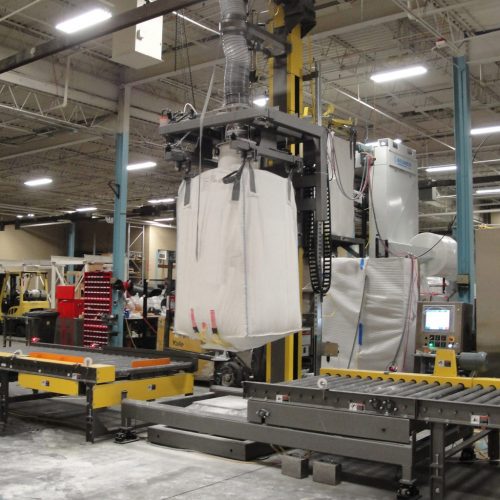
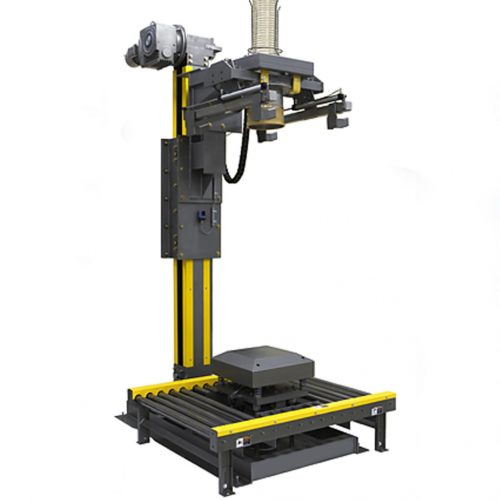
Features
- Cone Table Densification for Superior Bag Stability
- Exceptional Bag Stacking Capabilities
- Precise Weighing Accuracy
- Leading the Industry in Fast Bagging – Over 35 Bags/Hour!
- Compatible with Various Bag Types
- Optional Automation Features
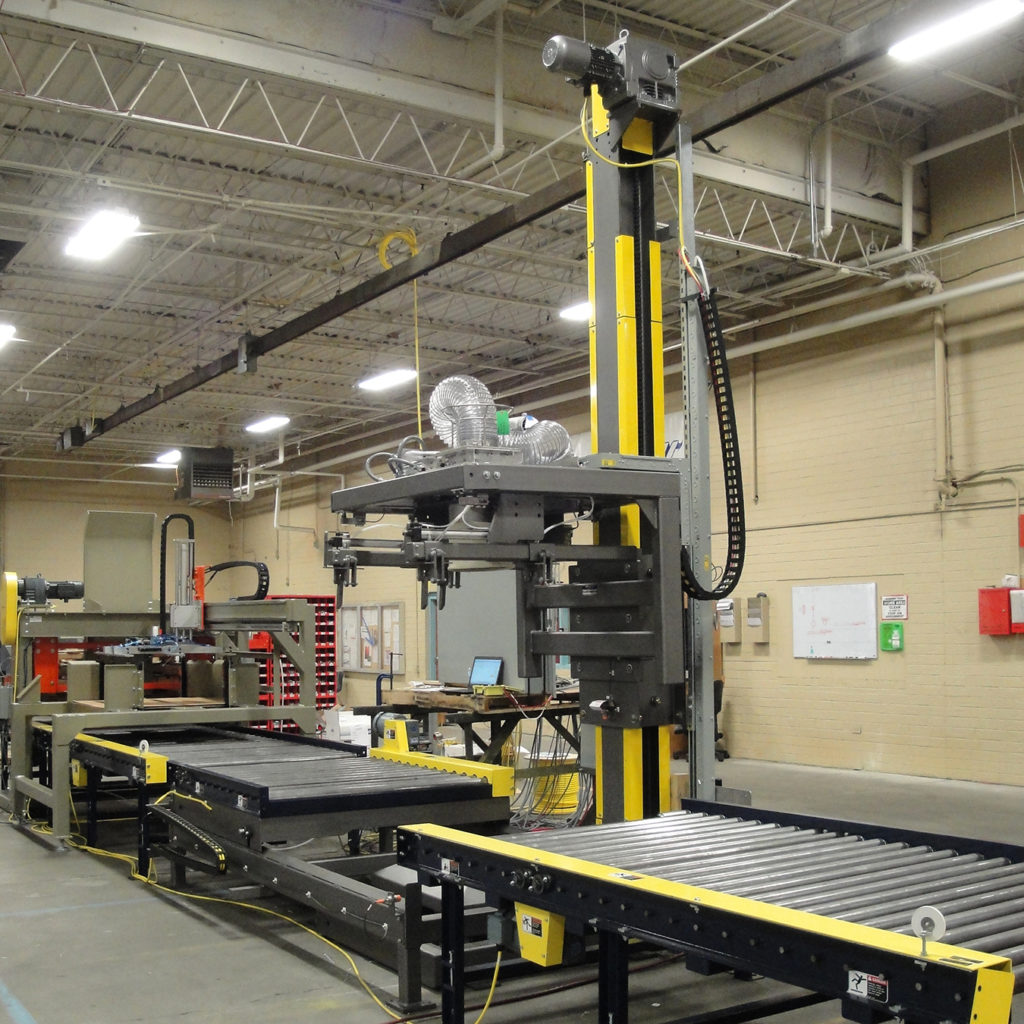
The CTE Bulk Bag Filler features patented cone table densification ideal for powders, granules or pellets that are easily aerated and/or difficult to compact. When the bulk bag is properly stretched and the material is deaerated with a flattened angle of repose, the result is a safe and stable bag.
The CTE allows bags to be stacked after filling. This reduces storage and transportation costs by reducing storage and shipping footprints with stacked bags.
The CTE Bulk Bag Filler utilizes hang weighing and delivers repeatable best-in-class weighing accuracy.
The CTE Bulk Bag Filler can deliver unmatched bulk bagging rates of 30-35 bags/hr. with weighing and more than 40 bags/hr. with pre-weighing! Maximum bagging rates are achieved by optioning the filler with roller conveyors for automated removal of filled bags.
The CTE is capable of filling multiple styles and sizes of bulk bags. The movable mast can be sized for the height of bulk bag being used.
How The CTE Bulk Bag Filler Works
Spiroflow’s cone table densifier effectively removes air from light materials. Utilizing a truncated pyramid design mounted on electro-mechanical vibrators to densify material throughout the filling cycle.
The CTE’s hanging bag design allows for quick and efficient bag filling. The bag is raised and lowered on to the densification table throughout the filling process. Forcing material to fill out the corners of the bulk bag and provide a full and stable bag at the end of the process.
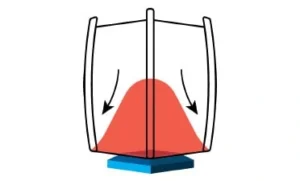
1. Build a stable base
The cone table’s shape directs the product to the bottom corners of the bag to create a stable foundation.
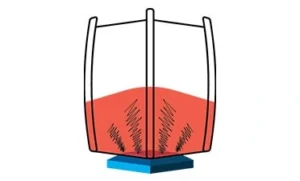
2. Transfer maximum energy
The cone table makes direct contact with the bag, resulting in maximum vibration energy transfer.
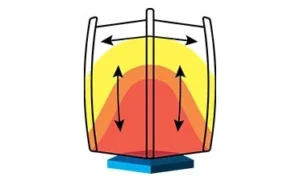
3. Stretch the bulk bag
During the filling cycle of a bulk bag, approximately half of the time is spent with the bag suspended by its loops, not touching the cone table. In this phase, the bulk bag expands, enhancing its volumetric capacity and aiding in stabilizing the bag. A bulk bag that is both stretched and densified maintains its shape better and can accommodate a greater quantity of product.
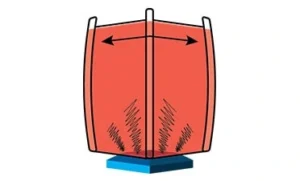
4. Removes the angle of repose
Almost any dry bulk solid has an angle of repose, which is the angle formed by the peak of material produced when pouring a dry bulk solid. To produce a flat-topped bag, the horizontal top of the cone table pushes up a column of product every time it comes in contact with the bag. When the cone table is removed from contact with the bag, the angle of repose is flattened.
YOUR REQUIREMENTS
When handling a bulk bag, you can either use the pallet or the bag loops. Using the pallet is ideal for transport or when moving the bag with a forklift, providing stability for heavier loads. Alternatively, handling by the bag loops is effective during the filling or emptying processes, allowing for precise positioning with equipment like hoists or cranes.
At this stage, you should consult both the bag manufacturer and Spiroflow to determine the proper bag style and size. The bag needs to optimize its volume for safe storage and transport. Spiroflow has seen outstanding results with Ameriglobe’s Fusion Baffle Bag, which is manufactured without sewing and, in most cases, does not require a liner.
An inflatable neck seal effectively contains the dust during filling. All our filling heads have an inner product flow and an outer annulus for dust evacuation. A dust extraction port is also included.
If filling by volume, options such as pallet dispensers, automatic bag loop release, bag take-off, and accumulation conveyors should be considered. These can be added at a future date to standard Spiroflow bulk bag-filling equipment.
If the area poses an explosion risk, static dissipative or groundable bags may be recommended together with a suitable static monitoring device.
Nitrogen purging is an option. Traditionally, when bag filling, the bag would be inflated with air before filling commences, but nitrogen can be used instead to increase product shelf life.
If the product is very fine, you will probably prevent leakage or moisture ingress. However, various alternatives can be used, such as coated bags or special bag seams. The liner must be inflated correctly to avoid creasing and subsequent discharge problems.
Vibration at the base of the unit deaerates and compacts the product to optimize the bag volume and form a safe and stable load. The CTE bulk bag filler uses our patented Cone Table densification for highly aerated powders.
Automatic loop release is available, but height adjustment is not offered on the CS Base Filler. The C-Series & CTE bulk bag fillers offer height adjustment. Yes, automatic loop release of filled bags is a useful labor-saving option for pallet-loaded bags. Powered height adjustment is also recommended if different-sized bulk bags are being filled in order to speed up the filling process.
Yes. Spiroflow supplies a range of options for filling rigid bins, drums, boxes, or octabins.
APPLICATIONS
Complete Bulk Bag Filling Systems and Semi-Automated Filling Systems
This is where we truly excel. We take care of everything from concept to commissioning.
Our semi-automated bag-filling system, ideal for high-volume users, enables continuous operation without manual unloading of each bag or gaylord box. Pallets are automatically positioned for filling, with bags attached to pneumatically operated hooks. After filling, the bags are released and conveyed along the line by a powered conveyor.
The featured setup includes a dual semi-automated CTE bulk bag filling system comprising two CTE fillers, a slip sheet dispenser, an operator platform, automated bag removal conveyors, and gravity roller conveyors. This efficient arrangement integrates advanced conveyor technologies and industrial conveyor systems for streamlined operation.
CONFIGURATIONS
Our CTE bulk bag fillers can operate as stand-alone units or as part of a semi-automated filling system.
MODELS & SPECIFICATIONS
The CTE Bulk Bag Filler can be configured with a variety of components. Based on your application, a Spiroflow engineer will recommend one of three CTE designs.
CONTROLS
Our CTE Bulk Bag Filler can be provided with:
- Gain-in-weight Controls
- Weight Display (no set points)
- Batch Controller
Please share controls requirements with your sales engineer for full specifications.
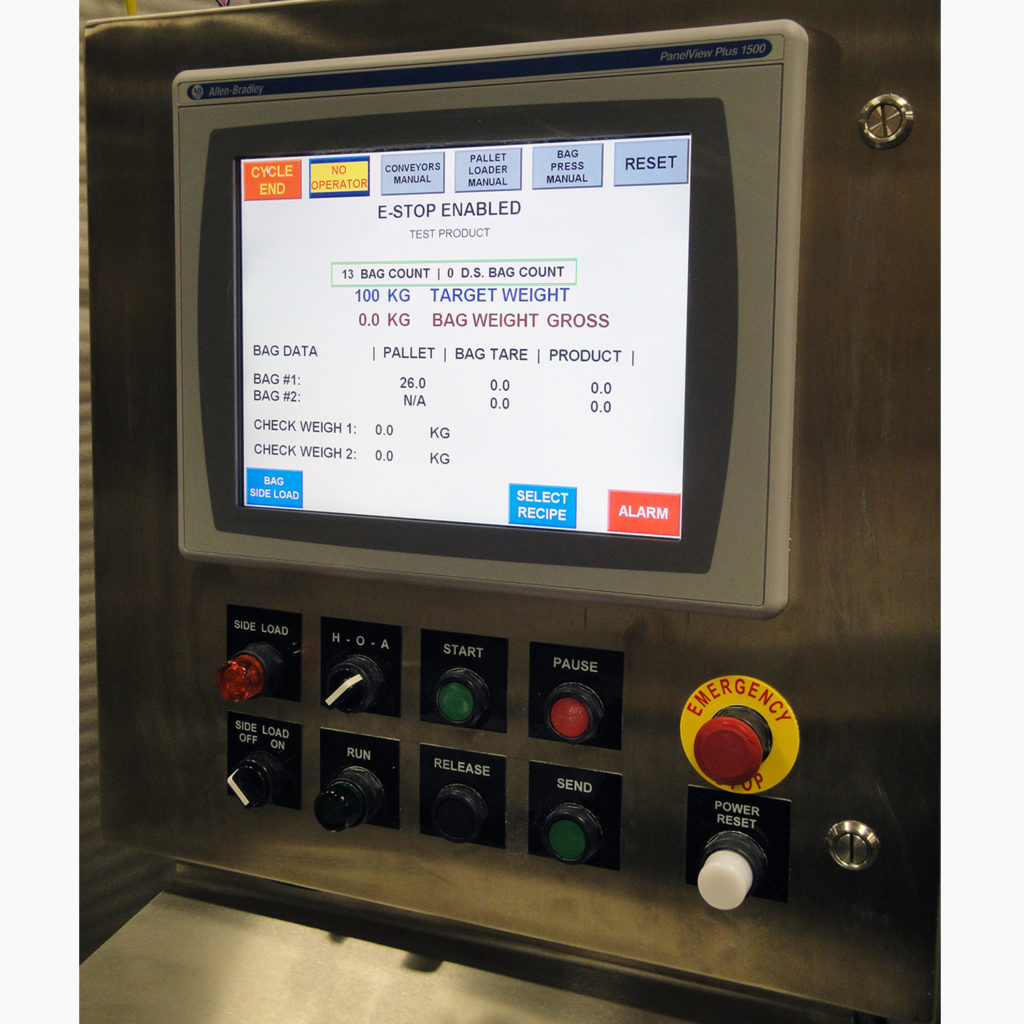