In various industries, reducing material breakage with a tube conveyor system is of paramount importance. This holds especially true in the food processing sector, where the fragility of materials can result in significant adverse consequences. In this blog post, we’ll delve into the common causes of material breakage and explore the effectiveness of tube conveyor systems in mitigating or eliminating these issues.
Why Does Material Integrity Matter?
Material integrity plays a crucial role in ensuring product quality and operational efficiency. Material breakage, defined as the division of material particles into multiple pieces due to stress, poses a significant challenge throughout various stages of production.
Whether materials are sliding on a conveyor surface, be it a tube, flat surface, or any other, there is a risk of material abrasion and potential breakage. However, despite the critical nature of preserving material integrity during conveyance, a staggering 29% of industrial facilities identify material breakage as one of their top three daily challenges.
While certain operations like grinding or mixing deliberately fragmented materials into smaller pieces to streamline processing, these processes serve a specific purpose in enhancing production value. In contrast, unintended material breakage typically results in a reduction in product value. In industries like food processing, even minor instances of breakage can lead to product loss, sanitation concerns, and decreased operational efficiency.
Critical Scenarios for Material Integrity Preservation
Preserving material integrity is particularly important in the following cases:
- When the material is easily degraded, such as in the case of friable materials, fragile materials, or materials otherwise prone to damage.
- When the consistency of blends or mixes must be preserved. This is vital for snack foods, breakfast cereals, tea blends, and other products that require an even combination of ingredients.
- When product dusting is a concern, some materials create more dust than others when they are broken. It can lead to respiratory issues for workers, equipment malfunctions, and other dust hazards, including dust explosions.
In short, breakage costs money – whether it’s wasted product, downtime for repairs, or poor quality products that need to be reworked or scrapped. The ultimate goal of every production facility, especially if they’re dealing with specialty materials or blends/mixes, should be to find ways to reduce or eliminate material breakage altogether. But to do that, we need to first understand what causes it.
Why Does Material Break?
The main reason why material breaks during conveying is due to impact. Here are the types of impact:
Free-Fall Impact
When fragile material is dropped, thrown, or otherwise falls from a high point, it’s likely to break. Free-fall impact commonly occurs when a material is transferred between different conveyor technologies when fed into the conveyor or discharged from it.
Collision Impact
Collision impact happens when two pieces of material collide on conveyor belt solutions – for example, two particles hit each other in mid-flight. It also occurs when a particle collides with a stationary element, such as a conveyor wall, conveyor belts, pipe, or other conveyor components.
This type of breakage is commonly seen in a flexible screw conveyor and pneumatic conveying system. The particles travel at high speeds as they move through the system (especially in pneumatic conveyors), and when they collide with an object, it can cause them to break.
Other Potential Causes of Breakage
There are other causes of material breakage, and these include:
- Excessive vibration,
- High temperatures,
- Chemical erosion,
- Electrostatic discharge,
- Moisture damage.
While all of these factors can contribute to material breakage, collision impact is the most common cause. In the next section, we’ll take a look at how tube
Ways to Mitigate Material Breakage
Here are some practical strategies for preventing material breakage:
- Opt for vibratory feeders – Choose vibratory feeders over rotary airlocks or screw feeders. Vibratory feeders are effective in reducing breakage at the inlet without the need for rotary shafts or blades found in rotary airlocks.
- Ensure smooth speed transitions – Minimize sudden impacts that can cause material breakage by smoothly transitioning conveyor speeds. Gradual speed changes, whether acceleration or deceleration, help mitigate this risk.
- Employ gentle curves – Beware of the impact of curved sections in the conveyor solutions. These curves can slow down material flow and increase contact with the surface, elevating the likelihood of breakage. Avoid sharp curves or utilize low-friction materials on the surface to reduce contact.
- Monitor environmental conditions – Maintain environmental conditions within the recommended ranges to reduce material degradation. Regularly monitoring temperature and humidity in your facility helps safeguard against material breakage.
Next, we’ll delve into the specific benefits of tube conveyors in reducing or eliminating material breakage.
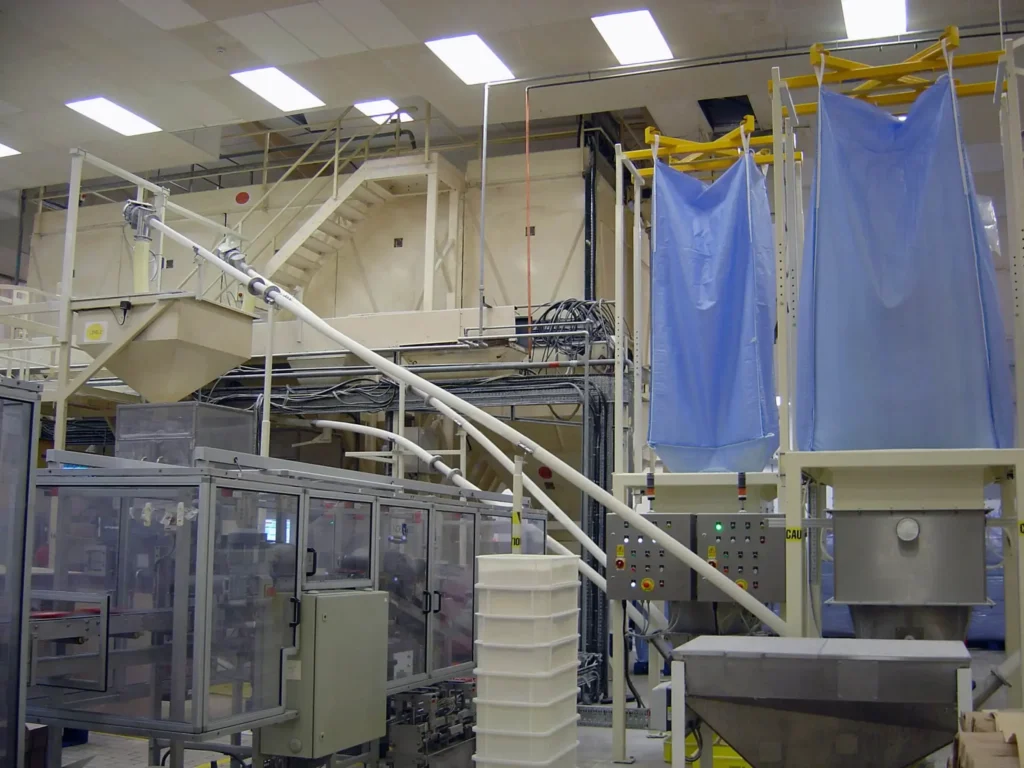
Explore All the Powers of Tubular Conveyors
A subtle yet often overlooked solution for reducing or entirely eliminating material breakage lies in employing gentle industrial conveyor systems. Such a system relies on low-speed, high-volume movement to gently guide materials along the conveyor line, minimizing contact points, preventing impacts, and ultimately preventing breakage.
Tubular conveyors offer a unique solution to this challenge. These systems consist of enclosed loops, unlike the traditional belt conveyor system. Tubular systems are designed to seamlessly transport materials through a facility. Materials are introduced into the first tube and then gradually and smoothly transferred to subsequent sections, continuing until they reach the end of the conveyor.
The mechanism responsible for material movement involves circular solid discs evenly spaced along a cable that stretches the length of the tube. Enclosed within, these discs gently nudge the material forward. The discs are connected to a gearbox, which, in turn, connects to a motor. The motor’s speed controls the discs and, consequently, the material’s pace.
Minimizing the Breakage
The beauty of tubular conveyors is the absence of abrupt changes in direction or speed. With the discs in constant motion, there’s virtually no opportunity for material breakage.
Beyond breakage prevention, tubular conveyors are well-suited for minimizing material degradation. They can be tailored to operate at low speeds, which reduces the likelihood of excessive vibration and exposure to high temperatures. Moreover, these conveyors are often constructed from materials like stainless steel, eliminating concerns related to chemical erosion or electrostatic discharge.
Environmental Control for Material Preservation and Optimal Performance
Although the traditional conveyor belt system has its pros, the enclosed nature of tubular conveyors also lends itself to better control of environmental conditions, particularly temperature and humidity. This feature further contributes to minimizing material degradation.
Furthermore, tubular drag and disc conveyors offer extensive customization options. This enables you to configure the system to follow a path that minimizes contact points and reduces the risk of collision impact. This adaptability ensures that the conveyor aligns precisely with your specific needs and material handling goals.
Tubular Cable vs. Chain Disc Systems
When choosing between tubular cable and chain disc systems to minimize material breakage, it’s essential to consider material integrity and cleanliness.
Cable disc systems hold a clear edge in preserving material integrity. The nylon-sealed cables and discs are less likely to entangle materials, reducing the risk of breakage. In contrast, chain conveyors with exposed links can catch and tear materials.
Moreover, cable and disc conveyors are more sanitary and easier to clean due to their smooth surfaces, while chain and disc conveyors have crevices where contaminants can accumulate. In terms of maintenance, cable and disc tube conveyors are also a preferable option.
Of course, if you’re seeking both material preservation and ease of maintenance, seamlessly integrated conveyor belt systems provided by reputable belt conveyor manufacturers are a preferable choice, ensuring smooth operations and lower maintenance needs.
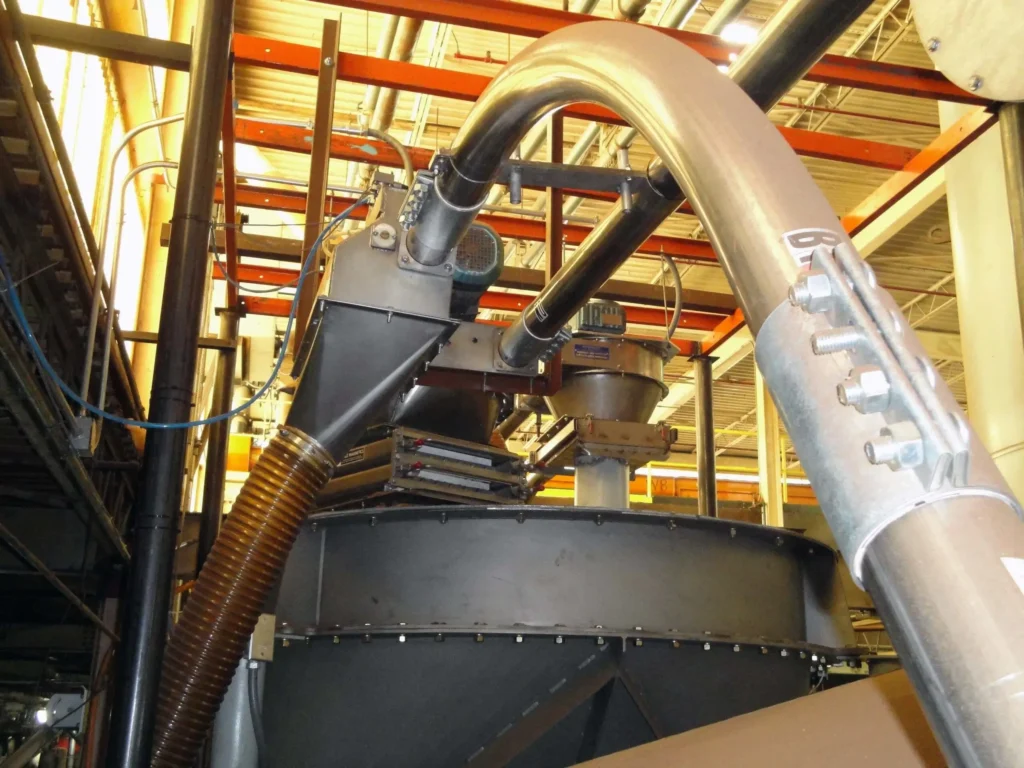
Spiroflow Ensures Reduced Material Breakage With Its Tube Conveyor System
Protecting the integrity of your material is important to the quality of your product. In the food processing industry, this means preventing material breakage, which can be done in many ways, but the Spiroflow tubular material handling system is one of the most effective.
Spiroflow, one of the most reputable conveyor systems manufacturers, has equipment with gentle conveying methods and low-speed, high-volume movement. That way, you can move your material along without many contact points while still minimizing the chances of breakage. You can also minimize material degradation, ensuring that your product is of the highest quality.
If you’re looking for a conveyor system to help keep your material intact, don’t hesitate to contact us today. Our engineers will work with you to create a custom system that meets your specific needs.