When it comes to selecting bulk material handling equipment, it’s crucial to consider factors such as safety, efficiency, and the specific needs of your operation. The right equipment can significantly streamline your process, ensuring the safe and effective handling of materials.
The Importance of Specialized Suppliers in Coffee Handling
Coffee handling solutions in today’s environment require a considered focus on safety, energy consumption, and reliability. There are a number of companies that offer material handling and conveying systems as merely an accessory for other equipment. Unfortunately, their product and experience often reflect this. Given the potential for problems with all but the free flow of materials, it is essential to select a supplier who specializes in dry bulk material handling.
Selecting a Supplier with Relevant Experience and Expertise
Look for a company that has experience with the products you handle and one that has significant technical expertise to apply their conveyor belt system to the specific requirements of the application. This normally requires an engineered solution, with layout drawings and any necessary custom-designed parts to adapt the system to suit the application and location.
Ensuring Reliable Solutions and Support from Your Supplier
Does the supplier offer a product test? Testing your exact material will ensure that the recommended solution operates as expected, and this step often eliminates surprises at start-up. Does the supplier guarantee their recommended solution and provide installation and post-sales support? Issues can arise during the installation, and you want a supplier committed to quickly and effectively working through these with you.
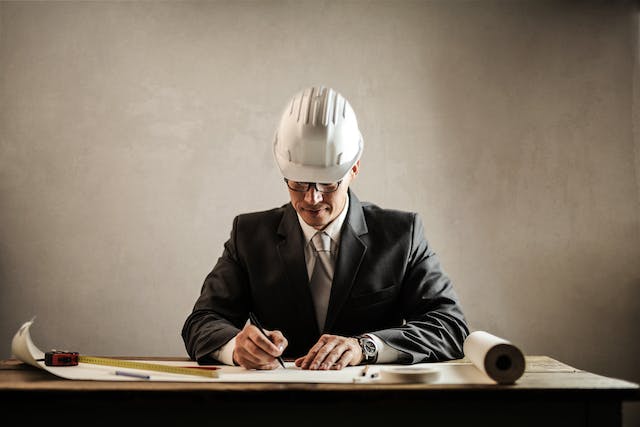
Selecting Bulk Material Handling Equipment and Suppliers
From an equipment perspective, consider a vendor who can supply conveyor belt solutions for moving the coffee between processes with a complete range of conveyors, filling, and discharge systems with high levels of containment. Keep in mind that during the material handling process, whatever the industry, even the most harmless ingredients can become a hazard when they appear as dust in the atmosphere. Homemade fabrications can never match the safety, reliability, and containment offered by specialist conveyor systems manufacturers demanded by today’s industrial practices and current legislation.
Your material handling solution may include silo/hopper/container/bag unloading, process links (conveying between processes or from process to packaging), and container filling (super sack/bulk bag, bag, box, or tote filling).
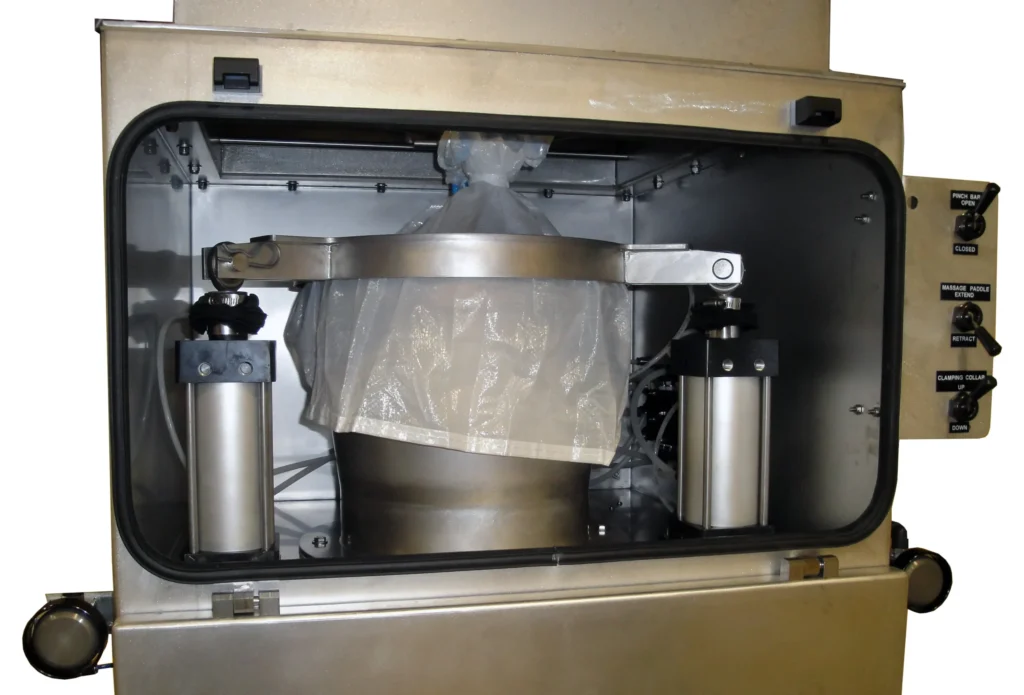
Unloading and Conveying Solutions
Efficiency and accuracy in the transfer of bulk materials are crucial in the coffee handling process. With the variety of containers used to transport raw coffee, the right unloading and conveying solutions are vital. These systems must not only handle the physical transfer of materials but also ensure the integrity and quality of the coffee beans during the process.
Bag or Container Unloading
Raw ingredients can arrive in a variety of bulk containers, from 50 lb. bags to 2,000 lb. super sacks/bulk bags or even drums, boxes, and totes, and need to be transported to the process from these containers. Specialist suppliers offer conveyor solutions to empty and fill these various containers and offer several conveying and controlled feed options suitable for conveying whole green coffee beans, roasted coffee beans, and ground coffee from the containers to the roasting process.
Silo or Hopper Unloading
Depending on the requirement, this can be as simple as a slide gate or butterfly valve with a volumetric feed or as complex as a loss in weight, load cell, and PLC weight-controlled feed using a bin activator. Bin activators use the angle of repose of the material and tilting louver blades with vibration assistance to control product flow in an accurate and controlled feed to the next part of the process. The correct selection of equipment here could eliminate a conveyor or process step.
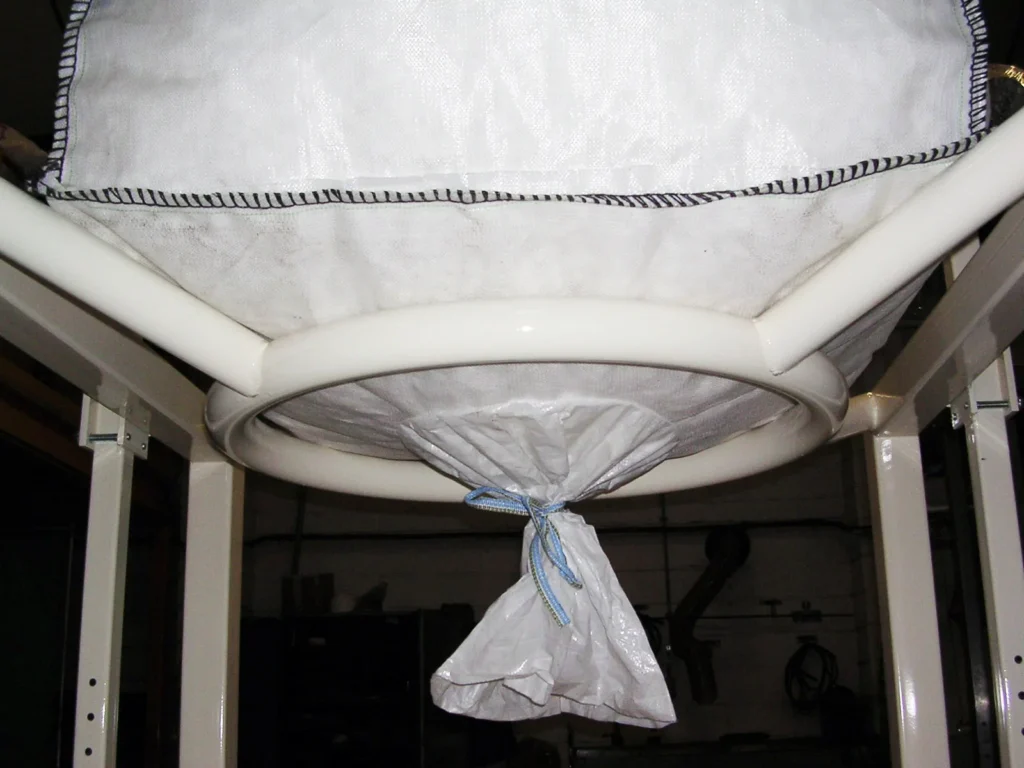
Types of Conveyors for Process Linking
Process link equipment solutions vary based on specific application requirements. Roasters should consider three mechanical conveying methods.
Flexible Screw Conveyors (FSC)
Flexible Screw Conveyors (FSC) provide dust-free, low-energy, low-maintenance, and low-cost conveying solutions. FSCs provide gentle handling and constant remixing of the conveyor contents. Constant mixing is an interesting advantage of this type of conveyor belt system. A center-less auger rotates within a sealed tube, and the speed and helical action of the screw encourage the product in the conveyor to rotate with the screw, with each particle in motion.
This creates a constant tumbling effect that provides a homogenous mix of particles in the conveyor and is essential when feeding pre-mixed ingredients to packaging or process machines. It is also possible to use this type of conveyor as an ingredient mixer if you add an inlet for a second product to it. A controlled feed will then provide a right ingredient mixture. The selection of conveyor size, screw section, and speed are determined during testing.
Aero-Mechanical Conveyors (AMC)
Aero-mechanical conveyors (AMC) are often overlooked but are very efficient for conveying coffee. This type of conveyor provides high conveying capacities and a total batch transfer. The totally enclosed tubular system provides a path for the driven rope and disc assembly to move around the circuit, and the result is a gentle conveying action and a reliable means of transporting coffee from process A to B. A Georgia-based roaster has used AMC for 8 hours per day for 14 years to transfer blends of roasted coffee from a mixer to a packaging machine without any new components.
Tubular Drag Conveying
This conveyor circuit is made up of straight and curved tubes to provide a totally enclosed tubular system that provides a path for a driven rope and disc assembly to move around the circuit. The result is very gentle conveying action. This is more sophisticated than an FSC or AMC and allows for complex circuits with multiple inlet and discharge points. It does not use air as a conveying medium. Instead, it relies on the equally pitched discs along the cable to form equal pockets within the conveying circuit that are suitable for containing coffee in all its forms.
When the rope and disc assembly are in motion (driven by a sprocket,) the coffee fed through an inlet port is contained within the traveling pockets and gently dragged around the circuit until it reaches a discharge outlet in the circuit. This conveyor provides total batch transfer but sacrifices the conveying rate due to a lower operating speed than an AMC. Operating speed is determined by the complexity of the circuit and the distance traveled. Working with a supplier that offers multiple conveying products will ensure that the strengths of each conveying method are objectively considered for your application.
Container Filling
If a roaster doesn’t complete packaging after roasting, they may need to move bulk volumes of coffee and, therefore, require a filling system. These are available with various levels of complexity to suit every budget. Generally, the larger the budget, the more automated the process and this means it will be more efficient.
For example, filling machines are designed with new programmable controllers designed to increase filling accuracy and cycle speed. Automatic gain in weight adjustment monitors compensate for any weight variations with an accuracy of +/-1%. This level of sophistication on fillers is ideal for companies seeking NTEP approval. There are also many custom features available to suit different containers and applications.
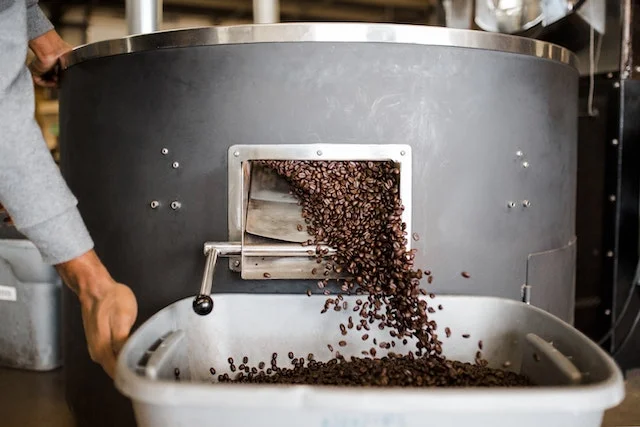
Criteria for Selecting a Reliable Bulk Material Handling Supplier
The most reliable suppliers of bulk material handling equipment will have a wide range of products to choose from when recommending conveyor solutions, can easily customize their equipment for different situations, provide a material test, and have a strong post-sales support track record. In other words, the right supplier will be more than a vendor but a partner with a vested interest in providing a safe, efficient, and reliable solution.
David Hesketh is Vice President of Engineering for Spiroflow Systems, Inc. Hesketh has 26 years of experience in material handling, particularly the design and development of conveyors and bulk handling equipment. He has worked for Spiroflow in the United States and the United Kingdom for 23 years and holds a BSc in Mechanical Engineering from the University of Central Lancashire.
Explore Advanced Solutions with Spiroflow
Interested in enhancing your bulk material handling processes? Connect with Spiroflow and explore a range of innovative conveying and handling solutions tailored to your specific needs. With decades of expertise in the design and development of state-of-the-art industrial conveyor systems and bulk-handling equipment, Spiroflow stands ready to be your partner in achieving efficiency, safety, and reliability. Contact us today to learn more about our products and how we can help optimize your operations. Let’s work together to find the perfect solution for your business.