When deciding between pneumatic vacuum conveyors vs. aero mechanical conveyors, understanding their unique features is paramount. These two industrial conveyor systems vary significantly in operation, efficiency, and suitability for different materials. By delving into their distinctions, from conveying mechanisms to energy consumption, you can make an informed choice to enhance your material handling operations.
Pneumatic Vacuum Conveyors vs. Aero Mechanical Conveyors – Which Ones Are the Best?
Are you looking to see which conveyor solutions are the best, pneumatic vacuum conveyors vs. aero mechanical conveyors (AMCs)? Spiroflow has been at the forefront of the bulk material handling industry for more than 48 years, selling both types of conveyor technologies. We’ll cover how each type of conveyor works, their similarities and differences, and how to determine which one is the best choice for a particular process.
Which Is Which – The Basic Characteristics of Both Industrial Conveyor Systems
Understanding the fundamental features of industrial conveyor systems is essential for selecting the most suitable option for your material handling needs. Let’s delve into the unique characteristics of two prominent systems – pneumatic vacuum conveyors and aero mechanical conveyors. By exploring their advantages and operational mechanisms, you’ll gain valuable insights into optimizing material transport efficiency and cost-effectiveness.
Pneumatic Vacuum Conveyors – Efficient Material Movement With Air Suspension
In pneumatic or vacuum conveyors, materials are transported in a suspended stream of gas, typically air. Controlled solids-to-air ratios, coupled with vacuum pump-generated differential air pressure, propel materials through the conveying tube. This system offers simplicity and hygiene, making it suitable for various applications, even across challenging routes.
Aero Mechanical Conveyors – Mechanical Efficiency With Reduced Capital Costs
Aero mechanical conveyors function as ‘mechanical’ pneumatic conveyors, offering advantages over vacuum conveyors with lower capital costs. They operate without the need for filtration equipment, aerating the product through rapid conveyor movement. With approximately 80% air and 20% material in each pocket, they efficiently convey materials while ensuring dust-free and clean handling, ideal for diverse applications in various industries.
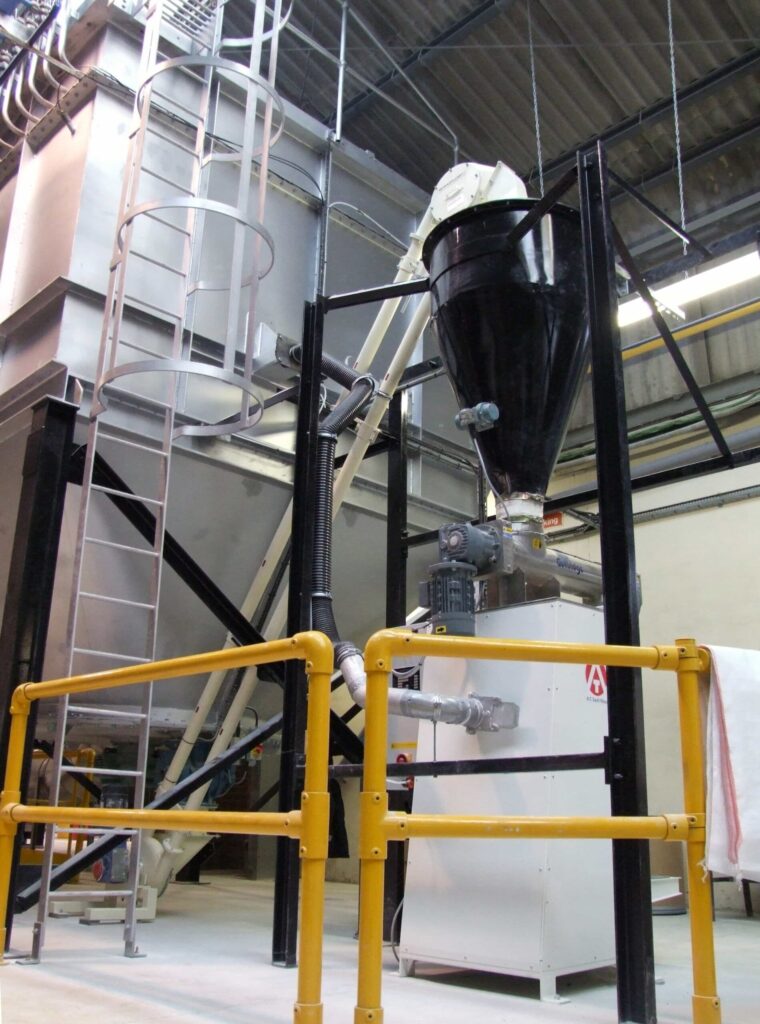
One of the Main Differences Between These Two Systems – DART Device for Aero Mechanical Conveyors
The incorporation of a DART Automatic Rope Tensioning device can prevent unnecessary maintenance issues, especially during the initial breaking-in period or critical 24/7 operation. Proper tensioning of the rope assembly is vital for smooth operation.
With resources stretched thin or conveyors in inaccessible locations, regular inspection and maintenance may not be feasible. Spiroflow offers the DART on AMCs, ensuring well-maintained conveyors run smoothly for up to 15 years before requiring spare parts.
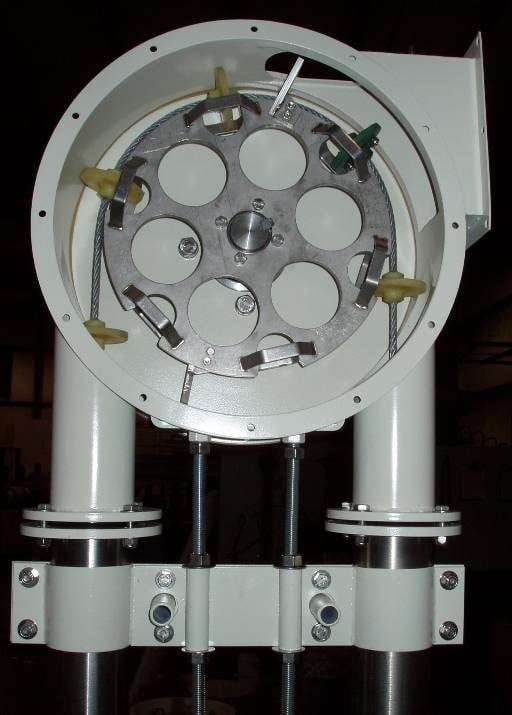
Additional Questions to Ask Yourself Before Deciding Which Type of Conveyor Will Work Best for Your Needs
Before deciding on the ideal conveyor type for your requirements, it’s essential to ask further questions. Each aspect can significantly impact your operations, efficiency, and overall costs. Let’s delve into some key additional considerations to ensure you make an informed choice for your facility’s needs.
Is Power Consumption a Priority?
AMCs can transport materials at speeds ranging from 400 to 1,840 cubic feet per hour, contingent on the tube diameter. Achieving these rates involves employing a drive motor with a power range of 2 to 7.5 HP, facilitated by a gearbox. In contrast, pneumatic conveyors necessitate a 20 to 40 HP blower to match the conveyance rates attained by AMCs.
Is Noise a Factor?
Pneumatic conveyors are much louder than AMCs, which operate below 85 dB. Pneumatic conveyors must be remotely installed or have mufflers, which adds to the cost of the system. These additional requirements pose challenges and considerations for facilities aiming to mitigate noise pollution while maintaining efficient material handling operations.
Does Your Process Require Multiple Inlets or Outlets?
For vacuum conveyors with multiple outlets, each outlet requires its own receiver, pressurized air supply for filter cleaning, and feed control valve and diverter valves. Additionally, extra piping is needed to connect each outlet to its respective usage point. This setup also involves venting the motive air and installing filters, valves, diverters, and additional piping to direct the product to each usage point, especially in pressure systems.
These components collectively contribute to the complexity and cost of the system, necessitating careful planning and installation considerations. Multiple inlets and outlets can easily be integrated with AMCs. When multiple outlets are used, we recommend that the conveyor operate at half speed. This ensures that the material exits the conveyor properly. A tube valve at each outlet provides a smooth path for the ingredient to pass through.
What About Venting?
One of the major advantages of an AMC is that it’s a balanced system. Ambient air is drawn into the conveyor along with the material. The material is discharged at the outlet of the conveyor. The displaced air is drawn back into the conveyor, creating a balanced system. There are no special venting or filtering requirements because there is no pressurization at the discharge point.
Spiroflow Has a Team of Engineers That Can Help You Decide Which Conveyor Solutions Are the Best Fit for You
Spiroflow boasts a dedicated team of engineers and expert conveyor manufacturers ready to assist you in determining the optimal conveyor solutions tailored to your specific needs. With the intricacies of each operation varying, it’s crucial to engage with professionals who understand the nuances of material handling.
Our company has teams of experienced conveyor systems manufacturers located in both the United States and the United Kingdom – we are here to offer expert guidance and support. Don’t hesitate to reach out to us for further inquiries or assistance in finding the perfect conveyor solution for your facility. Contact us today to unlock unparalleled expertise and streamline your material handling processes!
FAQ
What Are the Differences in Power Consumption Between Pneumatic Vacuum Conveyors and Aero Mechanical Conveyors?
Pneumatic vacuum conveyors typically require larger blowers, ranging from 20 to 40 HP, to match the conveyance rates attained by AMCs, which typically operate with motors ranging from 2 to 7.5 HP. This significant difference in power consumption should be carefully considered based on your energy efficiency goals and operational requirements.
How Do Noise Levels Compare Between Pneumatic Vacuum Conveyors and Aero Mechanical Conveyors?
Pneumatic conveyors are generally much louder than AMCs, operating above 85 dB. Additional measures such as mufflers or remote installations are often required to mitigate noise pollution, adding complexity and cost to the system. In contrast, AMCs operate below this threshold, offering quieter operation without the need for additional noise-reducing measures.
What Factors Should Be Considered When Handling Multiple Inlets or Outlets in Conveyor Systems?
For processes requiring multiple inlets or outlets, pneumatic vacuum conveyors with multiple outlets demand additional components like receivers, valves, and piping, increasing system complexity and cost. In contrast, aero mechanical conveyors offer a more straightforward integration of multiple outlets, minimizing complexity and potential points of failure.
How Do Pneumatic Vacuum Conveyors and Aero Mechanical Conveyors Address Air Venting?
Aero mechanical conveyors feature a balanced system where ambient air is drawn in along with the material, simplifying venting needs. Pneumatic vacuum conveyors, on the other hand, require special venting setups due to pressurization at the discharge point, adding complexity to the system design and maintenance.
How Can Spiroflow Assist in Finding the Right Conveyor Solutions for My Needs?
Spiroflow’s team of engineers and conveyor manufacturers is dedicated to helping you find the optimal solution for your material handling needs. With decades of experience, our experts can provide tailored guidance and support to ensure your conveyor choice aligns perfectly with your facility’s requirements. Reach out to us anytime for personalized assistance in streamlining your material handling processes.