Access Security Products, headquartered in Oakville, Ontario, since 1992, specializes in producing safes, vaults, and security equipment that are resistant to burglary and fire. They are known for employing a top-tier powder-handling solution technology, which has been instrumental in ensuring superior quality in the dissemination of their products across North America and other regions. Their customer base is diverse, encompassing governmental bodies, financial organizations, and dealers of security equipment.
The Rising Need for a Powder Handling Solution
A proprietary cement mixture found in the walls of the company’s safes and vaults renders them almost impenetrable to both thieves and fire. This castable material has extremely high compressive strength for maximum burglary resistance. In the production environment, however, the cement presents some material handling challenges. It is highly hygroscopic, which means that it readily absorbs and adsorbs water, has poor flow properties, and bridges readily.
Handling and Storage Challenges
A twenty-ton container of cement comes from Europe about once a month. It is packed into twenty 2,000-lb lined bulk bags for single-loop, single-trip operations. The bags are dumped into a silo that is large enough for outdoor storage. At its arrival, the material is quite compacted.
Given its hygroscopic characteristics, the entire load must be emptied into the silo as quickly as possible to minimize moisture capture. The company’s goal was to empty a single bulk bag in 30 minutes and all 20 bulk bags within 10 hours. They needed a robust and reliable material-handling solution to do so.
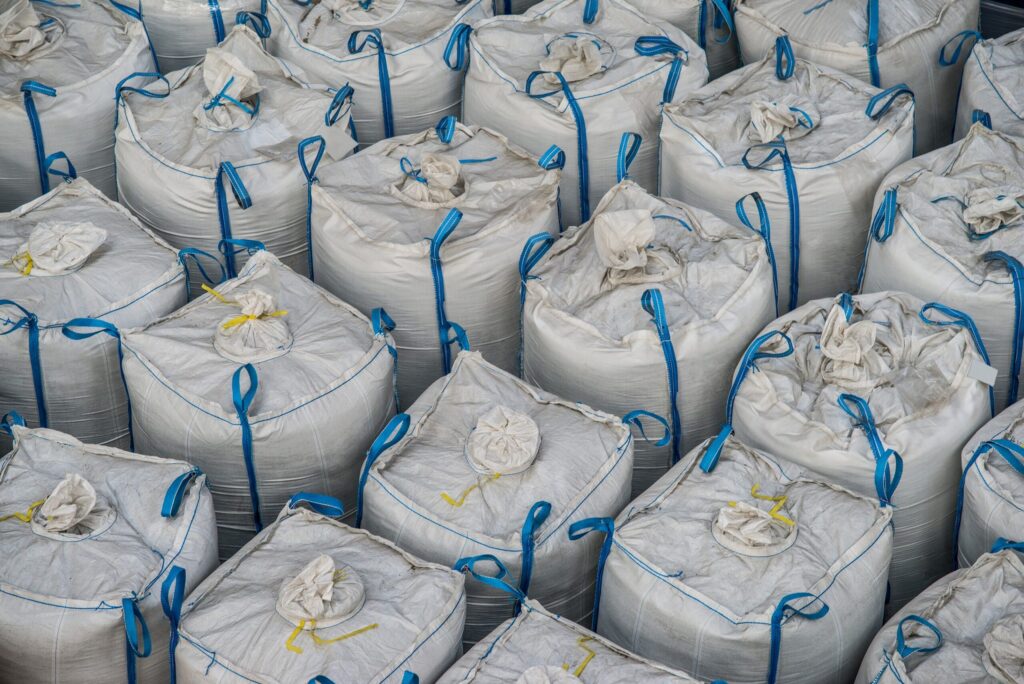
Challenges with the Initial Pneumatic Conveying System
In the very recent past, Access Security had installed a $40,000 pneumatic conveying system that unfortunately did not work as specified. Cement material accumulated within the conveying tube, plugging it up and rendering the conveyor inoperable. These repeated malfunctions led to significant operational difficulties for the company.
Transition to an Alternative Handling Method
Following numerous struggles, Access Security finally scrapped the equipment and went looking for a conveying solution that could move the cement material successfully. It was a problem. The company ended up going without a material handling system for about a year. During that time, it had to empty bulk bags directly into the storage silo with a crane – an expensive and labor-intensive process.
Requirements for a New Conveying System
Access Security needed a “closed” system that reliably conveyed cement without material build-up or excessive equipment wear. Bulk bag unloading takes place inside the warehouse, with product conveyed outside the building through the roof and into a large, outdoor storage silo about 40 feet away from the building. This had to happen reliably and consistently amidst weather extremes typical to Ontario.
A dust-free solution would minimize material exposure to moisture and provide employees with a clean and safe work environment. The system would successfully discharge a 2,000 lb. single-loop, lined, single-trip bulk bag within 30 minutes or less. Appropriate discharge aids for side massage, bottom massage, and agitation were to encourage material flow and minimize product loss.
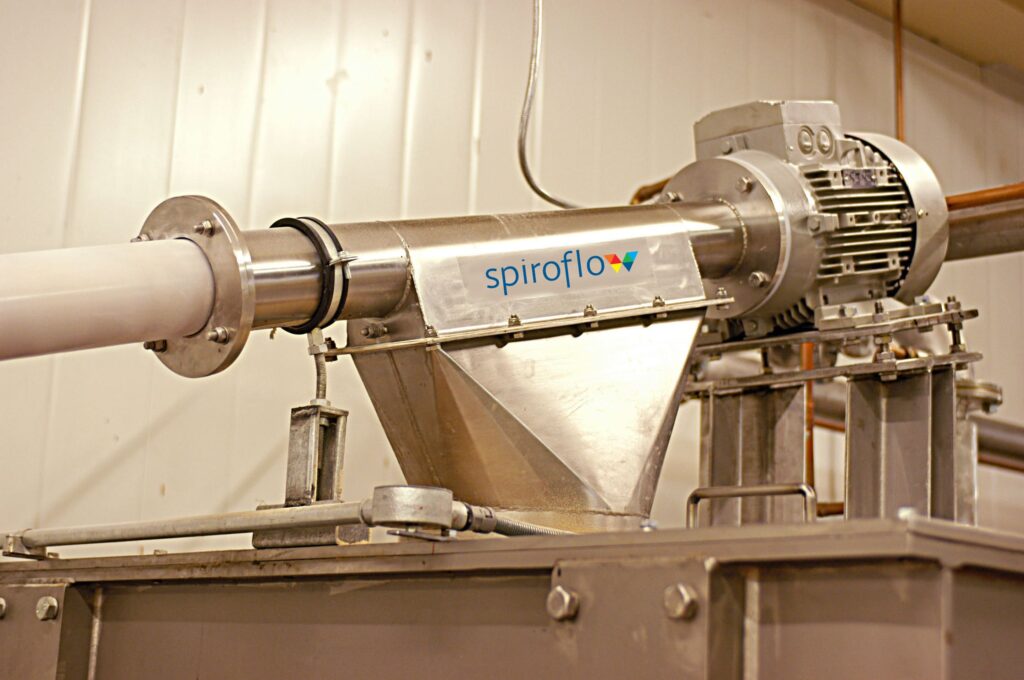
Initial Testing and Validation by Spiroflow Systems
Given the cement’s particular material characteristics and Access Security’s already considerable frustration, Spiroflow Systems experts recommended the cement product be tested in the company’s test lab. “Having our cement powder thoroughly tested was a vital step in the process,” Peter Gauthier, Access Security’s president, says. “It gave us confidence that Spiroflow’s recommended solution would work as specified.” Spiroflow Systems guarantees any material-handling solution tested in its lab, which “also gave us peace of mind,” added Gauthier.
Spiroflow Systems’ Customized Material Handling Solution
The Spiroflow Systems’ solution included a T4 Single Trip Bulk Bag Discharger in combination with Flexible Screw conveyors and Aero Mechanical Conveyors. The discharger has a pneumatic bag piercing knife to cut open the bottom of each single-trip bulk bag. For the best dust management during discharge, it also features a dust-evacuation frame with a dust-seal barrier made of rubber inside the support dish. To promote material flow, the discharger has vibration and four-corner massage. Additionally, by breaking up compressed material at the bottom of the bulk bag, the pneumatic bag-cutting knife promotes material flow.
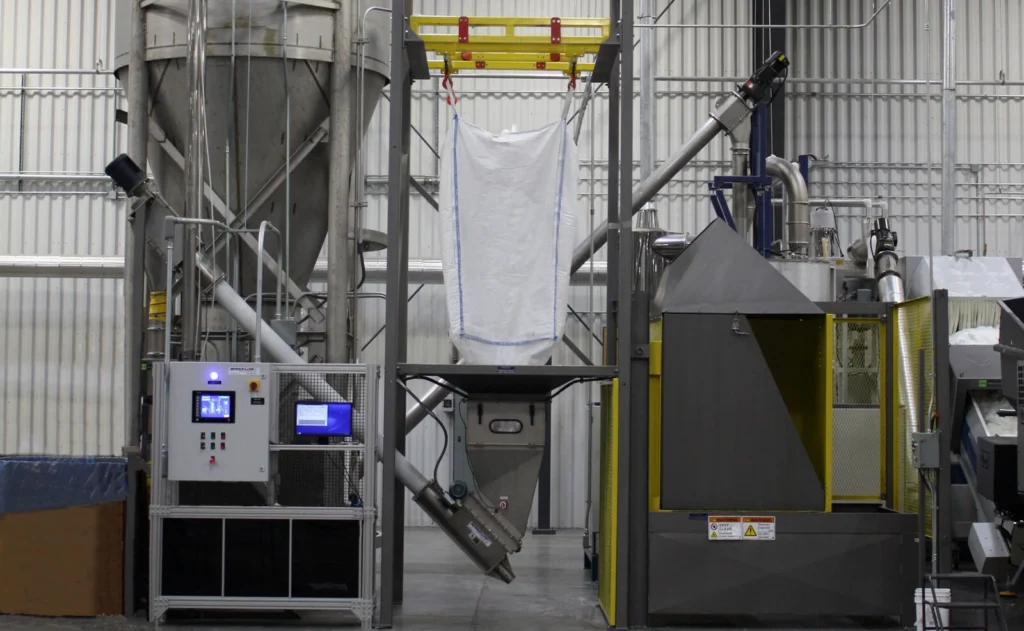
Implementation of Dual Flexible Screw Conveyors
Dual Flexible Screw Conveyors, only two feet in length and positioned at a 45° angle, are fitted to the bottom of the bulk bag discharger. The “screws” moving the material out of the discharge hopper have a beveled profile, ideal for conveying poor-flowing material. Their semi-rigid construction enables steep conveying angles without bends.
Integration of Aero Mechanical Conveyors (AMC)
The dual Flexible Screw Conveyors deliver cement material coming out of the bulk bag discharger onto a vertical Spiroflow Aero Mechanical Conveyor (AMC). The AMC is four inches in diameter, 21’ long, and positioned vertically. A second Aero Mechanical Conveyor, 40’ long and positioned at a 33° incline, moves the cement material from the vertical AMC, through the roof, and outside the building into the outdoor storage silo. Controls are included for the variable-frequency drives for the Flexible Screw Conveyors, the agitator motors, Aero Mechanical Conveyors, the low-level hopper probes, four-corner massage and vibration.
Maintenance and Operational Success
Spiroflow recommended that ASP completely clean the equipment after each container of material is conveyed into the outdoor storage silo. This prevents any potential material build-up from interfering with equipment operation. In operation, ASP reports that the material handling system works “beautifully,” based on reliability and an operating rate twice that required – and without material build-up.
The closed system keeps the cement material dry and contained, minimizing product waste and ensuring a clean, safe employee environment. “Spiroflow equipment handles our cement powder quite well and actually empties each bulk bag in only 15 minutes,” concludes Gauthier. “Our goal was to empty each 20-ton container in 10 hours and we have cut that time in half.” See this case study in Processing Magazine’s March 2014 Bulk Supplement.
Elevate Your Business with Spiroflow’s Conveyor Solutions
Are you looking for reliable and innovative conveyor solutions for your business? Whether you need a flexible screw conveyor, a sophisticated belt conveyor system, or any industrial conveyor systems, Spiroflow has the expertise and technology to meet your needs. As a leading conveyor systems manufacturer, Spiroflow is dedicated to providing you with conveyor belt systems that optimize your operations and enhance efficiency. Don’t let material handling challenges slow down your business. Contact Spiroflow today to discover how our conveyor technologies and custom solutions can revolutionize your material handling processes.