In the world of modern logistics and material handling, you need to know all about the principles of FIBC bulk bag filling for design and handling. Let’s equip you with the knowledge needed to harness their full potential, allowing you to make informed decisions and optimize your operations.
The principles of FIBC bulk bag filling for design and handling encompass the precise engineering of these flexible containers to ensure the safe and efficient transportation of bulk materials. From selecting the right bag type to understanding proper filing techniques, these principles guide industries in optimizing their material handling processes, minimizing waste, and enhancing overall operational efficiency.
What Are FIBC Bulk Bags, What Are They Used For, and Why Are They Important?
Flexible Intermediate Bulk Containers (FIBCs), also known as bulk bags, big bags, or super sacks, are made of tightly woven strands of polypropylene. It is a flexible fabric designed for storage and transportation.
These woven, flexible bags hold dry, flowable materials, ingredients, and powders across industries including:
- Food and beverage,
- Plastics,
- Pigments,
- Chemicals,
- Pharmaceuticals,
- Grains,
- Construction materials,
- Salt,
- Peanuts,
- Seeds,
- Minerals.
Unlike smaller, dusty 50 lb bags that are now dwindling in popularity, most FIBCs are built to hold at least 2,000 and up to 4,000 lbs of product. These also protect operators with dust control solutions in both the filling and unloading processes.
The reduction in the number of bags needed for filling, storage, and emptying (due to each bag holding more product) and the introduction of a flexible solution (vs. traditional rigid containers) come with a laundry list of benefits.
It’s no surprise that the global FIBC market size is expected to reach $6.4 billion by 2026. As more and more products are supplied in FIBCs, all aspects of the bulk bagging system become increasingly important. This system includes:
Explore the Benefits of FIBC Bulk Bags
If you decide to follow the latest conveyor technologies and move from conveyor belts to tubular drag conveyors, you need to learn all about FIBCs as well. These are growing in popularity as a bulk transportation and storage solution (vs. using traditional smaller bags and rigid boxes or drums) due to the benefits of bulk bags, including:
- Safe and easy handling – Bulk bags are filled at the top and emptied at the bottom vs. tipped over, improving operator safety. Further improving safety are integrated dust collection systems available for bulk bag fillers and workers. Additionally, bulk bags are not moved manually by workers but by forklifts or pallet jacks, minimizing risk for the operator due to there being no direct contact.
- Reduced storage, shipping, and labor costs – Fewer bags mean fewer trucks to ship and fewer bags to move, and stable bags mean operators can stack bags two high on the plant floor, saving on the storage room. Additionally, the bulk bags themselves, once emptied, can be folded and stored at the facility using minimal space, unlike a rigid container like a box or drum.
- Minimum risk of product damage or loss – The polypropylene flexible material is more tear and puncture-resistant vs. rigid containers, which protects the contents from damage or loss from material leaking out of the bag. Additionally, the filling and unloading process for bulk bags reduces the risk of spillage vs. the tipping motion needed to unload rigid containers that must be both filled and unloaded from the top.
Who Uses FIBC Bulk Bags?
FIBC bulk bags serve as a packaging solution for a wide range of companies and organizations, all sharing a common interest in ensuring secure, cost-effective handling while minimizing the risk of damage or loss. This aligns with the benefits outlined earlier.
Here are some examples of the types of companies that utilize FIBC bulk bags:
Product Manufacturers and Suppliers
These entities utilize FIBC bulk bags to facilitate the efficient discharge of their products into these containers, ensuring safe transportation and handling.
End Users and Buyers
Companies that receive products supplied in FIBCs as part of their operations value the convenience and reliability of these bulk bags for their material handling needs.
In-House Handling
Some organizations employ FIBCs as a handling unit within their own facilities, streamlining internal processes and bolstering material transport efficiency.
Custom Packers
Businesses engaged in custom packing rely on FIBC bulk bags to receive bulk products, enabling them to pack and distribute materials effectively.
Transportation, Shipping, and Storage Companies
Entities involved in the transportation, shipping, and storage of goods appreciate the durability and versatility of FIBC bulk bags when handling a variety of cargo.
- Product Manufacturers and Suppliers
These entities utilize FIBC bulk bags to facilitate the efficient discharge of their products into these containers, ensuring safe transportation and handling.
- End Users and Buyers
Companies that receive products supplied in FIBCs as part of their operations value the convenience and reliability of these bulk bags for their material handling needs.
- In-House Handling
Some organizations employ FIBCs as a handling unit within their own facilities, streamlining internal processes and bolstering material transport efficiency.
- Custom Packers
Businesses engaged in custom packing rely on FIBC bulk bags to receive bulk products, enabling them to pack and distribute materials effectively.
- Transportation, Shipping, and Storage Companies
Entities involved in the transportation, shipping, and storage of goods appreciate the durability and versatility of FIBC bulk bags when handling a variety of cargo.
End of Accordion
These diverse applications demonstrate the broad appeal and adaptability of FIBC bulk bags within the industry. Moreover, many professional conveyor systems manufacturers will also recommend using this safe equipment.
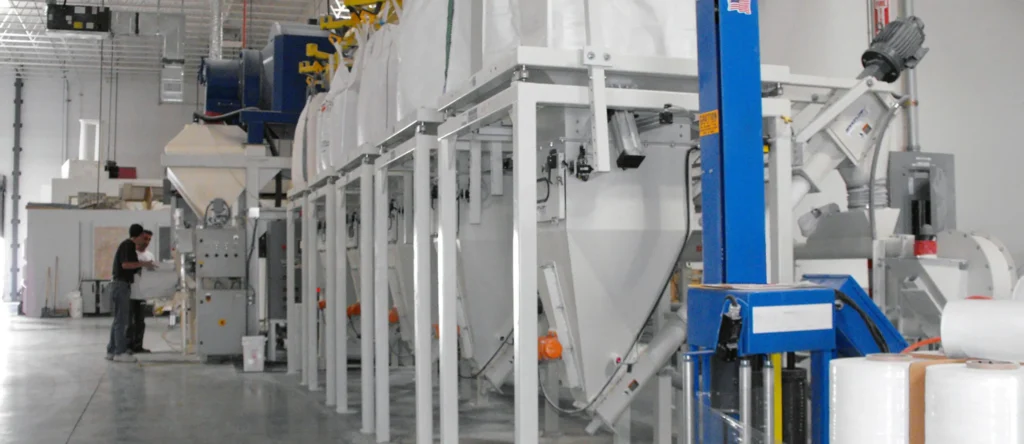
FIBC Bulk Bag Design and Filling System Guide
Explore the best practices for handling FIBC bulk bags and optimizing the design of your bulk bag filling system, all with an eye toward seamless cooperation with belt conveyor manufacturers. Remember, the careful design of both the bulk bag and the filling system can be the key difference between unwieldy, uneven, and unsafe bags and well-organized, flat-top, and secure bags that smoothly interface with both tubular drag and conveyor belt systems.
Determining FIBC Size and Shape
When determining the bulk bag size, the following criteria must be considered for the bulk bag filling system:
- Product weight in the FIBC bag,
- Product-tamped bulk density,
- Internal dimensions of the shipping container or vehicle on which the FIBC will be transported,
- The net filled height of the FIBC (after filling).
When it comes to determining the bag shape, remember that rectangular base FIBCs will round out while filling in their mid-section. Also, square or panel bags do not round out as much. To determine the correct base size and shape, the internal dimensions of the shipping container or trailer should be evaluated to ensure a “push fit.” ISO containers are usually 7′ 6″ wide internally.
“Push fit” means that, when placed side by side in a container/trailer, the exterior side of the bags touch the container wall, and the interior sides touch each other. This prevents the bags from shifting during transport.
Use Formula for Placing FIBCs Side by Side
To place two FIBCs side by side across the container/trailer, use the following formula:
Maximum FIBC Base width = (3.14 X Internal Width of Container or Trailer)/(8 x (1 + Stretch Factor)).
FIBC Rounded Out Diameter = (2x (Base length + Base width) x (1 + stretch factor)) / 3.14
Count on the Stretch Factor
The stretch factor can vary depending on the tightness of the weave of the FIBC fabric being used, the structural design of the bag, and the density of the filled product. Generally, a figure of 3% – 5% should be used.
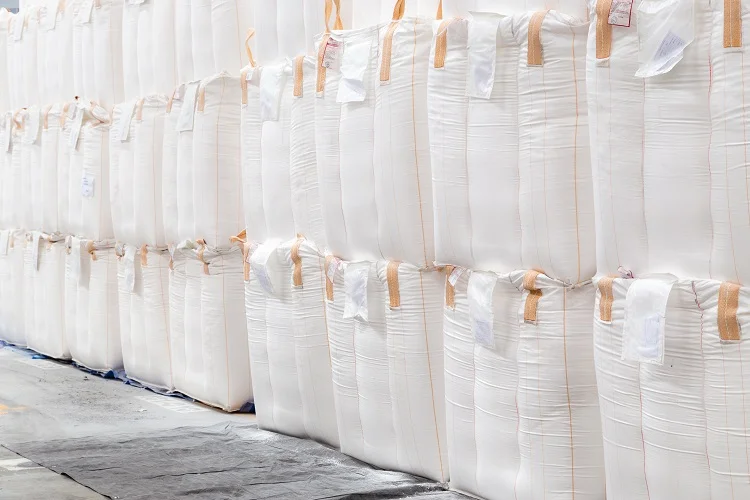
FIBC Manufacturer Relationship
To arrive at the base size that will fit the selected method of transportation, a close partnership between conveyor solutions and FIBC manufacturers is required to ensure that they can supply the right size. The height of the bag depends on the filled density, the weight required, and any height restrictions placed on the FIBC by the user.
Storage and Transportation Considerations
Where storage of filled bulk bags plays an important cost factor for both the filler and the discharger, you should consider both – safe stacking height and test filled height.
For safe stacking of FIBCs, it is not advisable to stack bags two high if the bags are over 5′ high and three high if they are over 4′ high – regardless of whether they are on pallets or not. FIBCs should not be higher than twice the base plus width. Additionally, leveraging a bulk bag filler that results in higher densification should be considered to produce a flatter bag top, which is more stable for stacking.
The filled height of the product in the FIBC after filling can vary considerably depending on the type of filling machine used and the characteristics of the product. It is important to get the product tested on the selected filling machine before ordering FlBCs. Bulk bag filling machines that have the capability of densifying the product during filling save on FIBC height and make a safer and more stable FIBC for stacking and handling.
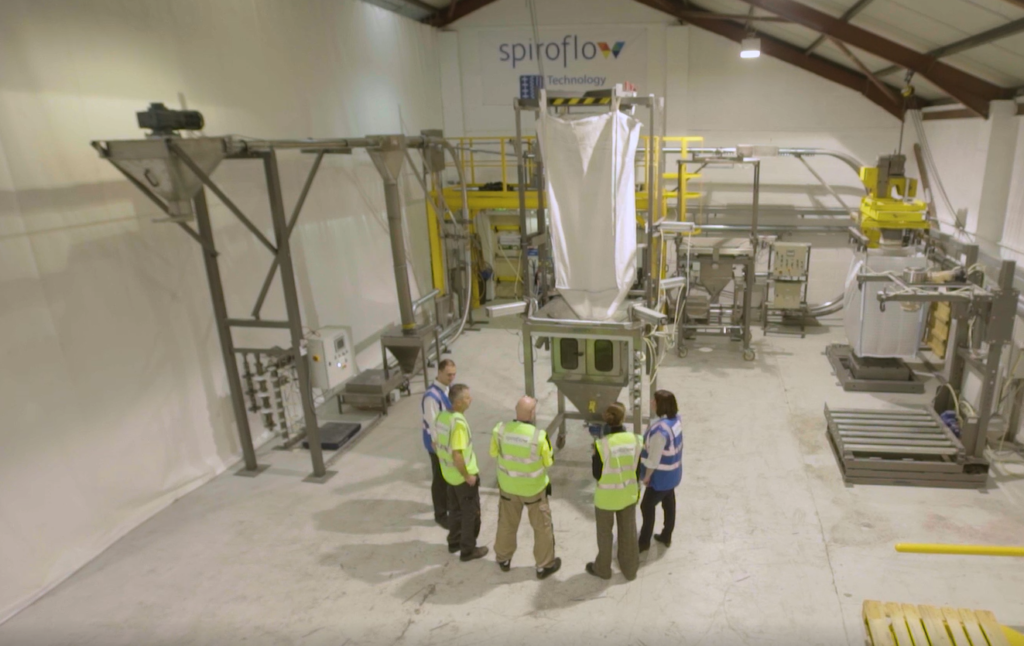
How to Select Lifting Loops, Spouts, and Outlets
These elements are crucial not only for safe and efficient handling but also for seamless integration with industrial conveyor systems (even the traditional belt conveyor system). Here are the key considerations that will empower you to make informed decisions, ensuring a harmonious flow within your conveyor-based operations.
Lifting Loop Options
Lifting loops are usually located at the top four corners of the FIBC and are used to lift up and move the bag. They may also be of the “Cross Corner” type. “Pop Up” loops help to enable a forklift truck to engage the loops without additional labor, but they do incur additional costs. The length of the loop is generally 10″ but may increase to 12″ if the FlBC is to be picked up and moved by forklift truck tines.
Filling Spouts
Bulk bag fill spouts are tailored to fit the filling machine head. When liners are used, some machines clamp only the liner, in which case the diameter of the filling spout can be increased to 20 – 24″ to allow the product to reach the “shoulders of the FIBC” and not bridge in its neck. This is most important with powders. A 15″ diameter is the most common filling spout diameter.
Outlet Spouts
The diameter of the outlet spout should be enough to ensure the easy discharge of filled product from the bulk bag. Diameters tend to vary between 10″ and 24″. Outlet spout length should be enough to ensure that it can be tied off and, in most cases, goose-necked. The length can vary from 16-36″ depending on the diameter.
Ease of discharge is also assisted by the correct design of the discharge machine. Most modern-day bulk bag discharge units can handle poor-flowing products, depending on their design and choice of product flow promotion device.
Other FIBC Outlet Systems
These are many and various, but all are designed to accommodate a product or discharger type that cannot be overcome by a standard outlet spout. Here are some of them:
- Flat bottom,
- Conical bottom,
- Hygiene flaps and hygiene system,
- Fully bottom opening bags.
Transportation, Shipping, and Storage Companies
Entities involved in the transportation, shipping, and storage of goods appreciate the durability and versatility of FIBC bulk bags when handling a variety of cargo.
Selecting the Right Liner for Your FIBC: Considerations and Types
Lined FIBCs, commonly used for fine powders, food, and pharmaceutical products, typically feature liners that are designed to resist moisture but are not entirely waterproof. It’s important to note that over time, moisture can gradually seep through the polythene material of the liners, so it’s crucial to securely tie off the bag after filling to maintain product integrity.
These liners usually come in a standard tube-like design, with the circumference of the extruded tube matching the base perimeter of the FIBC plus an additional 2% to prevent overstretching. They are predominantly made from linear blend polythene, which offers greater strength compared to low-density polythene, reducing the risk of tearing or crumbling when cut.
The thickness of these liners typically ranges from 5/16 inches, depending on the specific product and protection requirements. Keep in mind that these liners are suitable for products filled at temperatures not exceeding 176°F, as they can begin to soften and lose effectiveness at higher temperatures. For materials requiring higher temperature resistance, specialized liners are recommended.
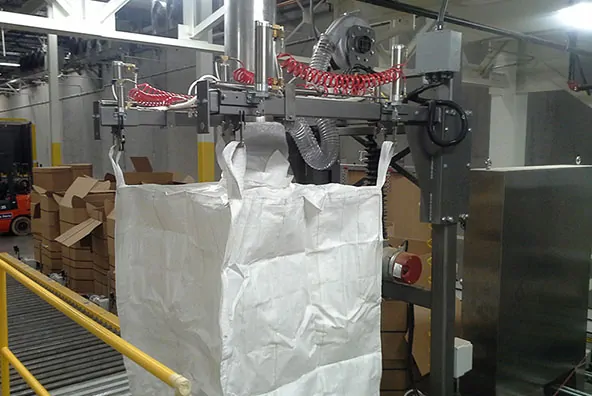
FIBC Bulk Bag Design: Bag Construction and Quality
FIBCs are designed to be lifted by their loops when filled, and strength is built into the FlBC to give a safety factor of 5:1 for single-trip bags and 6:1 for multi-trip (used more than once) bags. UN Chapter 16 FIBCs are tested to a safety factor of 8:1.
FIBCs designed to hold food or pharmaceutical products should be manufactured in such a fashion to ensure loose cotton ends or frayed material from hand-cut areas do not occur. Outlet spouts should be hemmed, and tie cords should have “flames” ends.
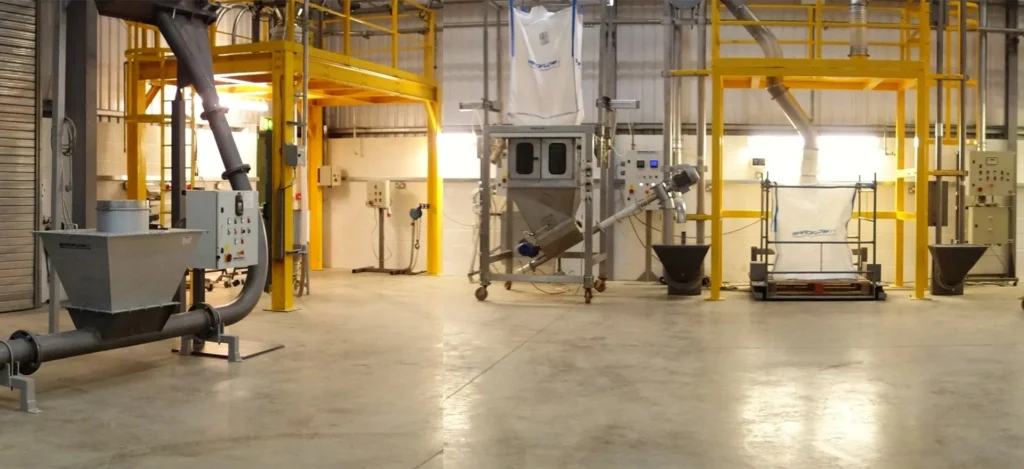
FIBC Bulk Bag Handling
Proper handling techniques are essential to prevent accidents, product spillage, and damage to both the bag and its contents. The following considerations are important for safe and efficient movement by pallet:
- The correct size of the pallet should allow the rounded section of the FIBC to overlap the edges of the pallet so that when two palletized bags are placed side by side, the bags touch and not the pallets. This increases the stability of the bags when packed in containers/trailers.
- The FIBC should be positioned as close to a central position on the pallet as possible, especially after filling. A wide range of mechanical devices that can assist the forklift truck driver to achieve this are available, as well as the side shift on the truck itself.
- If the FIBCs are to be stacked, close slatted pallets, both top and bottom, should be used to stop “pinching” of the bag by allowing the top and the bottom of the FIBCs to protrude through the slats. These tend to be expensive and may only be financially justified for “in-plant” use unless their return can be guaranteed.
Check out the table with the tapped and untapped densities of common products:
Tapped BulkDensity lb/ft3 | Untapped BulkDensitylb/ft3 | Ratio % | |
Aluminum Chips | 15 | 7 | 47 |
Aluminum Oxide | 120 | 60 | 50 |
Ammonium Nitrate | 62 | 45 | 72 |
Baking Soda | 55 | 40 | 73 |
Barium Soda | 180 | 120 | 67 |
Portland Cement | 94 | 60 | 64 |
Wheat Flour | 40 | 33 | 83 |
Talc | 60 | 50 | 83 |
Effect of Particle Shape on Air Removal
Particle shape, as well as size, plays an important part in the time it takes to remove entrained air. Plate-shaped particles of clays, for instance, take three to four times the amount of vibration to remove entrained air than a similar-sized round particle. Granular particles will lose their entrained air quickly under their own weight.
The larger the granule, the shorter the time it takes to get to a tamped bulk density. Even then, vibration will ensure that added stability is achieved. Vibration will only act on the weight of the material above the weight of the vibration platform. Therefore, don’t start the vibration until a minimum FIBC’s weight is 450 lbs.
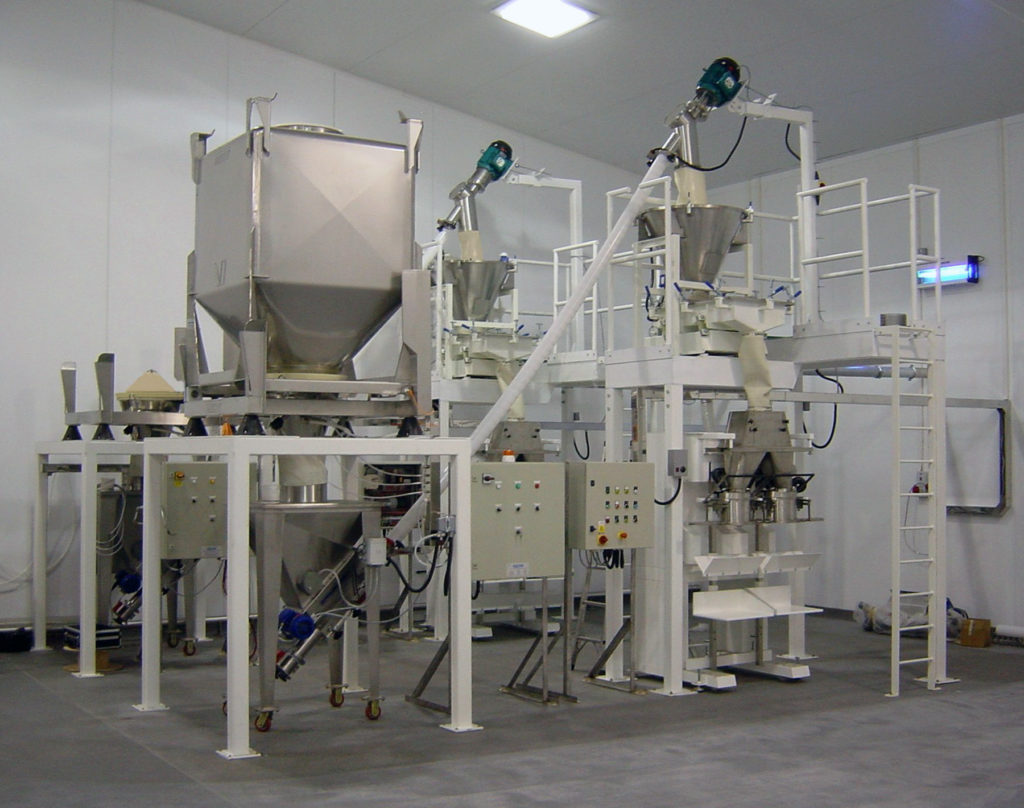
What Are the Key Considerations for Filling Bulk Bags?
Whether you’re using tubular drag or traditional conveyor belt solutions, knowing some of the key considerations when it comes to developing FIBCs is a must. Here’s what shouldn’t be overlooked:
- Proper bag position – When you hang woven polypropylene bags for filling, they tend to stretch a bit. So, it’s crucial to position the FIBC so that its seams can stretch down during filling, with the bag’s corners only touching the base once filling is done.
- Vibration for density – The stuff inside the bag should be as densely packed as possible. This density should be achieved while the bag is waiting to be removed from the filling machine by using base vibrations.
- Control the filling rate and air – You need to have precise control over how fast the product goes into the bag to ensure a steady fill rate. The filling head should also allow air to escape to prevent dust buildup and pressure inside the bag during filling.
- Inflating and sealing liners – If your FIBC has liners inside, it’s important to inflate them before filling. These liners should be sealed to the filling head to prevent dust from escaping. However, they should also be free to move inside the bag without stretching. To keep your products fresh longer, you can use nitrogen to remove oxygen from the bag before filling. Oxygen can lead to bacteria growth, so a nitrogen purge and heat-sealing process can extend the shelf life of your products.
- Robust construction – Robust construction will ensure long life and protection from potential damage from forklift trucks.
Operator Access – Ensure Operator Ease of Access To
Creating a smooth and efficient workflow is essential in any operational setting. One critical aspect of achieving this goal is ensuring that operators have easy access to the tools, equipment, and systems they need to perform their tasks effectively.
- Attach the loops to the FIBC Support Arms,
- Connect the filling spout/liner to the filling head,
- Disengage the filling spout/liner from the filling head,
- “Tie off” the filling spout (the operator should be able to carry out all of these functions at shoulder height without the need to climb on the machine),
- Electrical controls, preferably compact microprocessor-based and easily accessible by the operator. All bag-filling functions should be able to be performed manually (as required by the operator) and automatically (once the filling cycle is initiated).
Bulk Bag Filling Automation
The above basic bulk bag-filling principles have been augmented by options designed to automate the filling operation and reduce operator involvement. These developments, including innovative solutions like the flexible screw conveyor, have enabled an increasing number of products to be handled in FIBCs, leaving the future open for more companies to benefit from the advantages offered by this form of packaging:
- Pallet magazine/stacker – This equipment holds multiple pallets in preparation for the filling process. It selects a single pallet from the stack and sends it to the filling machine.
- Slip sheet dispenser – Automatically places a slip sheet on the pallet before filling.
- Automatic bag loop release – After filling, the bag is automatically released from the filling machine for removal.
- Take off/accumulation conveyor – Transports the filled bag away, making room for a new bag to be filled.
- Spinning head – An attachment to the filling head used with “baffle” bags and granules to ensure even product distribution by dispersing the product stream as it enters the bag, achieving a uniform fill.
As industries continue to evolve and demand greater efficiency, the adoption of bulk bag filling automation is likely to grow, offering companies a competitive edge and greater control over their packaging operations.
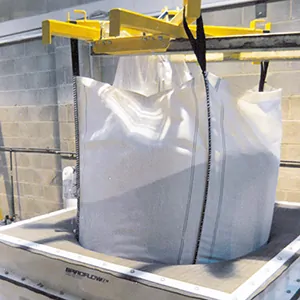
Follow the Principles of FIBC Bulk Bag Filling for Design and Handling and Have Optimized Manufacturing Process
Focusing on design and size and selecting the right FIBC bulk bagging system is vital, as the FIBC constitutes the costliest component in this packaging system. A poor decision can result in product wastage, increased labor expenses, and potential damage to customer trust in FIBC bulk bagging solutions.
Spiroflow can help you make the best decision for your production, especially when planning to use FIBC with a conveyor belt system. Contact us today, and our professional team will provide you with all the needed information – shipping, storage, fill weight requirements, bagging rate requirements, and any special considerations for the specific flowable material or application.