In the world of material handling and logistics, there’s an alarming number of forklift-related injuries reported each year. Surprisingly, most of these accidents are completely preventable. The National Forklift Safety Day serves as a crucial reminder of the importance of bulk bag safety and operator training around heavy machinery. It also allows us to learn about the innovative solutions companies like Spiroflow are implementing to reduce risks for everyone involved.
Unpacking Safety Numbers
Every year, forklifts are involved in between 35,000 and 62,000 accidents. Many of these accidents also harm people nearby, including bystanders and pedestrians. The Occupational Safety & Health Administration (OSHA) has found that over 70% of these accidents could have been avoided.
This brings us to the importance of National Forklift Safety Day, which is marked on the second Tuesday of June (which, in 2023, fell on June 13th). Originally started as an initiative by the Industrial Truck Association, this day serves as a reminder about the importance of safety training for everyone, no matter if you’re driving the forklift or working in close proximity to industrial conveyor systems.
The Role of Spiroflow and FIBCs in Enhancing Safety
As a global leader in bulk material handling and processing equipment, where operators commonly utilize forklift equipment to move bulk bags, Spiroflow understands the importance of keeping operators safe on the job. One way the industry has addressed growing concerns was the introduction of flexible intermediate bulk containers (FIBCs) and advanced handling systems. This is a significant step away from the smaller, manually managed bags that put operators at risk.
In fact, the use of bulk bags has grown significantly in recent years, in part driven by legislative efforts to reduce the strain on workers’ backs and prevent injuries from manual labor. Moreover, Spiroflow has integrated advanced conveyor technologies, such as the flexible screw conveyor, reducing the need for manual interferences, thus lowering the risk of injuries.
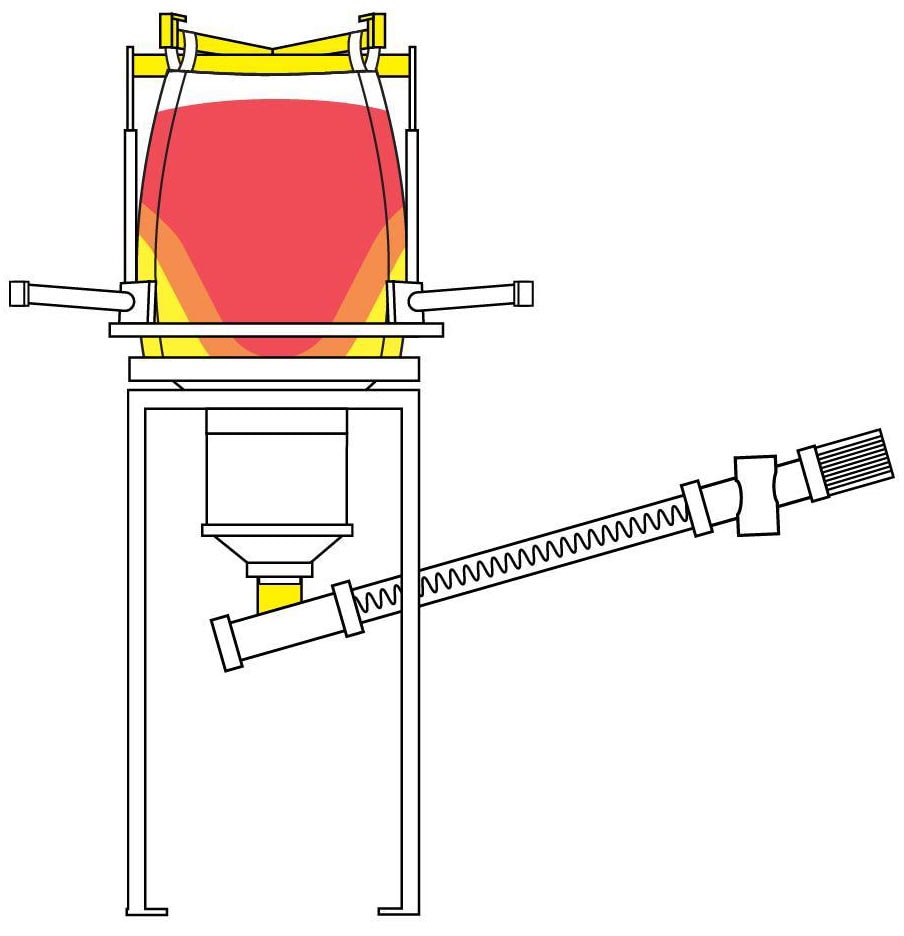
Benefits of Bulk Bag Handling Equipment and Advanced Conveyor Belt Solutions
The transition to more advanced handling systems marks a significant step towards reducing manual labor and enhancing workplace safety. However, it’s important to understand that the size of these bags themselves poses a risk. If they are not filled, stacked, or handled properly, they can cause injury.
Still, proper integration of these technologies into the production line brings a host of safety improvements, including the following:
- Reduction of manual labor & related injuries – by cutting down the need for direct manual handling, this equipment reduces repetitive lifting injuries and the all-too-common cut or puncture-related hand injury,
- Reduction & containment of dust – bulk bag unloading equipment can be designed to minimize dust escaping into the environment and the risk of exposing operators to potentially harmful substances,
- Automatic transfer of materials – they can often be configured to automatically transfer materials into the production process with minimal operator assistance,
- Built-in lifts & hoists – some bulk bagging equipment, such as the Spiroflow T6 Bulk Bag Unloader, comes equipped with a built-in lift or hoist for those scenarios where a forklift might not be available or its use is not ideal,
- Enhanced ergonomic design – this ensures that operators can perform their tasks more comfortably and with less strain, reducing the risk of musculoskeletal injuries and making the workplace safer.
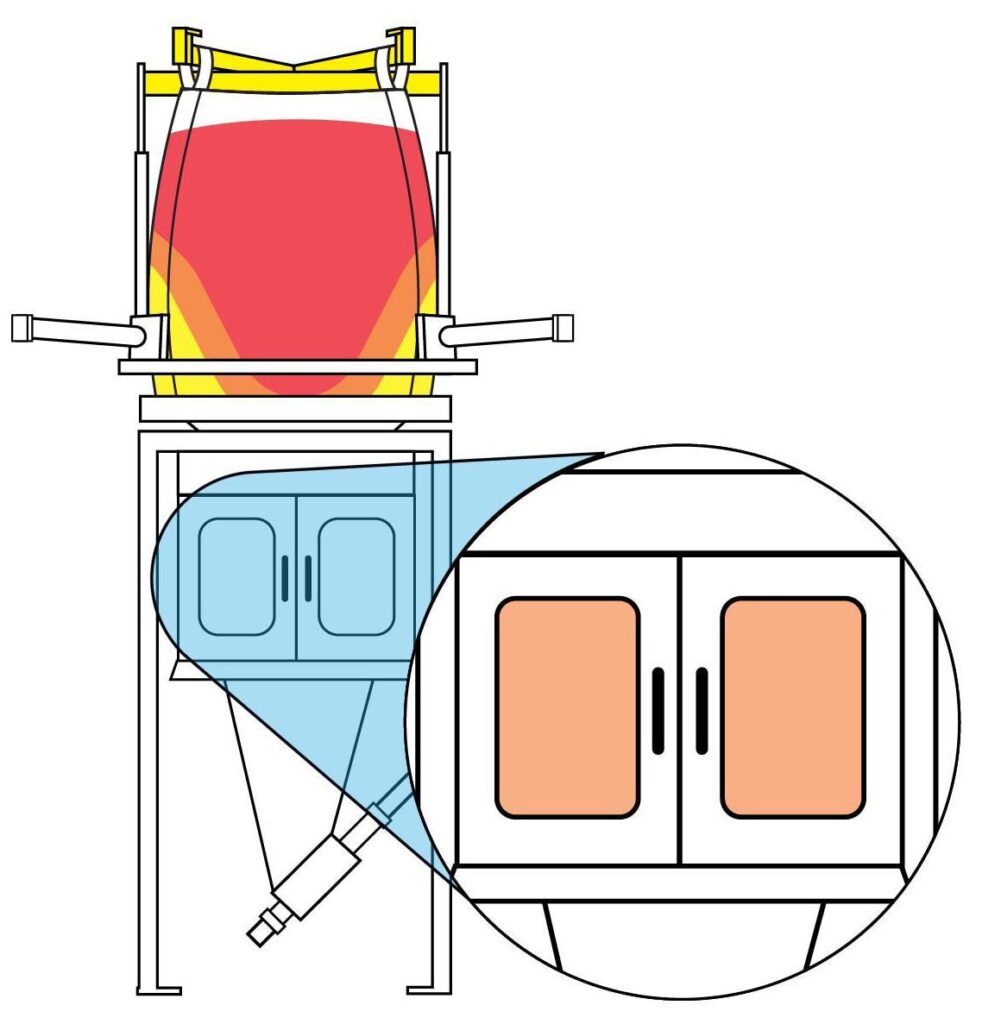
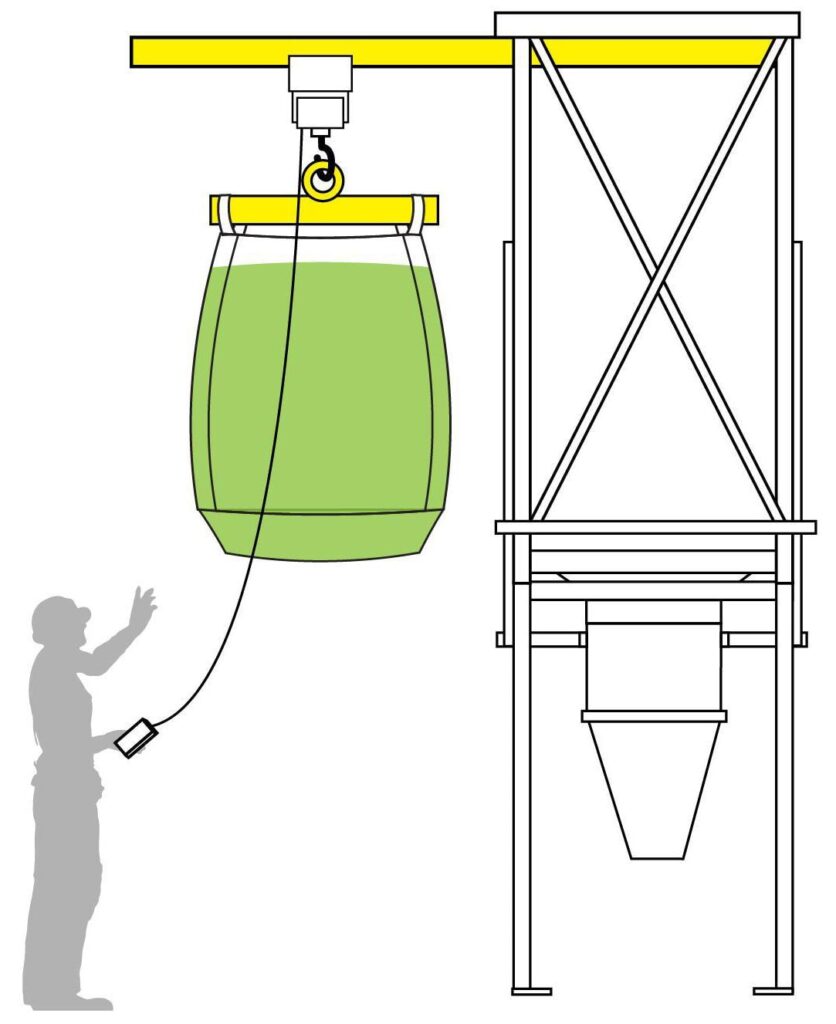
Design Considerations for Bulk Bag Safety
The design of handling equipment, along with conveyor belt systems, should always prioritize the safety and ease of use for operators. In order to ensure maximum safety, it’s important to define system requirements to find the best filling and unloading solution.
Moreover, considering the number of operators available and establishing realistic expectations for their workload is essential, regardless of the conveyor solutions that are utilized. Even automated systems will typically require some operator assistance.
Spiroflow’s patented CTE bulk bag filler features the cone table densification system, which densifies the material and increases stability
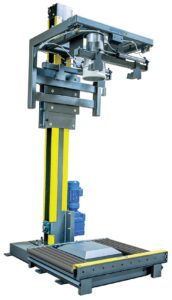
How to Find the Right Handling Equipment for Your Production Line
Selecting the appropriate equipment for your production line involves careful consideration of various factors to ensure efficiency, safety, and compatibility with your operational needs. Here are some important considerations when researching the right bulk bag handling equipment to meet your needs:
- Material properties – Is the material prone to dusting? Is it highly flammable if dusting occurs? Is it dangerous for the operator to inhale the material?
- Flow characteristics – How well will the material discharge from bags? Does the bulk bag unloader need a bag tensioning device or other flow aids, like massage paddles or vibrators, to ensure all products are discharged?
- Size and type – How can we ensure that the right type of bag is being used so no product can escape or other issues occur?
- Placement and removal – Is there a forklift available, or is an integral hoist needed? Will partial bags ever need to be removed from a discharger?
- Headroom or space constraints – Where will this equipment be installed? Are there space constraints that need to be considered?
- Weight or batching requirements – What sizes and weights will be used? What are the batch and accuracy requirements?
- Dust containment or hygienic requirements – Are materials hazardous or toxic and require dust containment? Are there hygienic requirements that accompany your application (i.e., food processing)?
Spiroflow Offers Many Advanced Solutions
Spiroflow’s comprehensive range of equipment caters to a wide array of applications, ensuring there’s a perfect match for every need. This includes the C Series Bulk Bag Fillers, designed for high-volume operations that demand quick and accurate filling, as well as the CTE Bulk Bag Fillers, which are customized to meet the unique requirements of specific industries. Also, our Base Model Bulk Bag Fillers provide a dependable and cost-efficient solution for companies looking for high-quality filling without a hefty price tag.
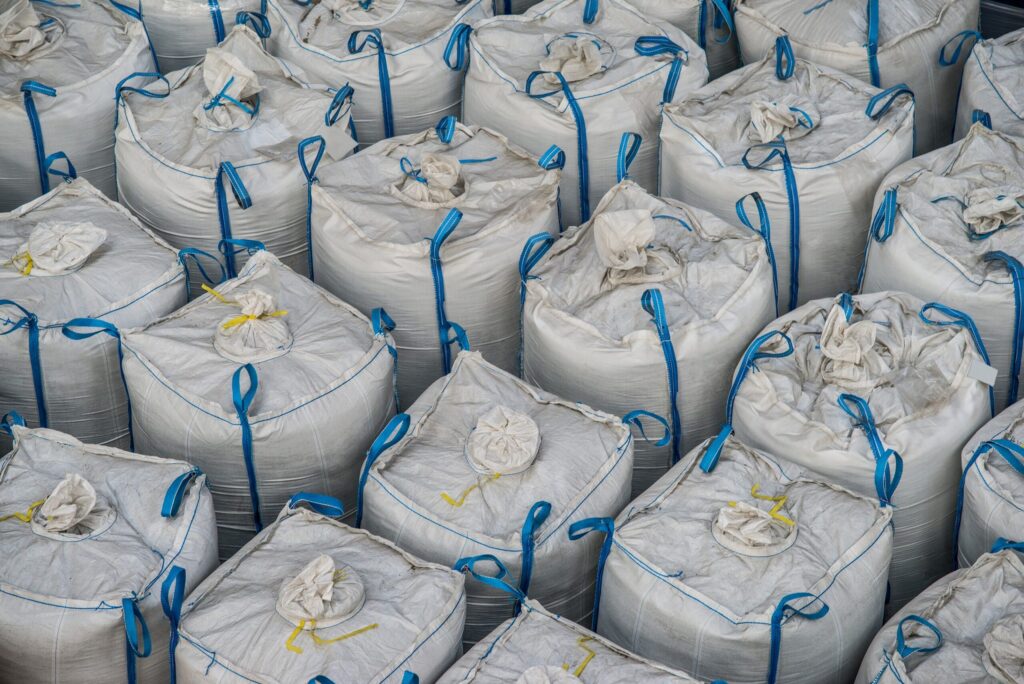
Create Customized Solutions for Your Production With Spiroflow
At Spiroflow, we understand that each manufacturing process is unique and that there’s no one-size-fits-all when it comes to conveyor belts and bagging equipment. Our engineers consider unique material characteristics, types, and manufacturing processes in designing this equipment, thus covering a comprehensive range of applications. Contact us today and learn more about our line of bulk bag fillers, as well as bulk bag unloaders and discharging stations.