A flexible screw conveyor has emerged as a versatile workhorse in the world of handling materials. However, like any essential piece of equipment, there could be some problems with flexible screw conveyors that can impact efficiency, safety, and overall productivity. In this blog post, we’ll explore effective solutions to help you find the perfect setup for your specific needs and keep your operations running smoothly.
Problems with flexible screw conveyors often revolve around issues of material clogging, wear and tear, and achieving optimal performance. Finding the best setup involves addressing these challenges to ensure seamless material handling and maximize efficiency in your operations.
What Are Flexible Screw Conveyors and Why It’s Important to Know All About the Possible Problems?
Flexible screw conveyors (FSCs) are vital equipment in various industries, facilitating the smooth movement of materials. However, understanding their possible problems is equally crucial. From preventing costly downtime to ensuring workplace safety, knowing the ins and outs of these conveyors is paramount.
Additionally, awareness of these issues promotes workplace safety by addressing potential hazards. Moreover, comprehensive knowledge of possible problems allows for efficient system optimization, ensuring that your operations run smoothly and productively.
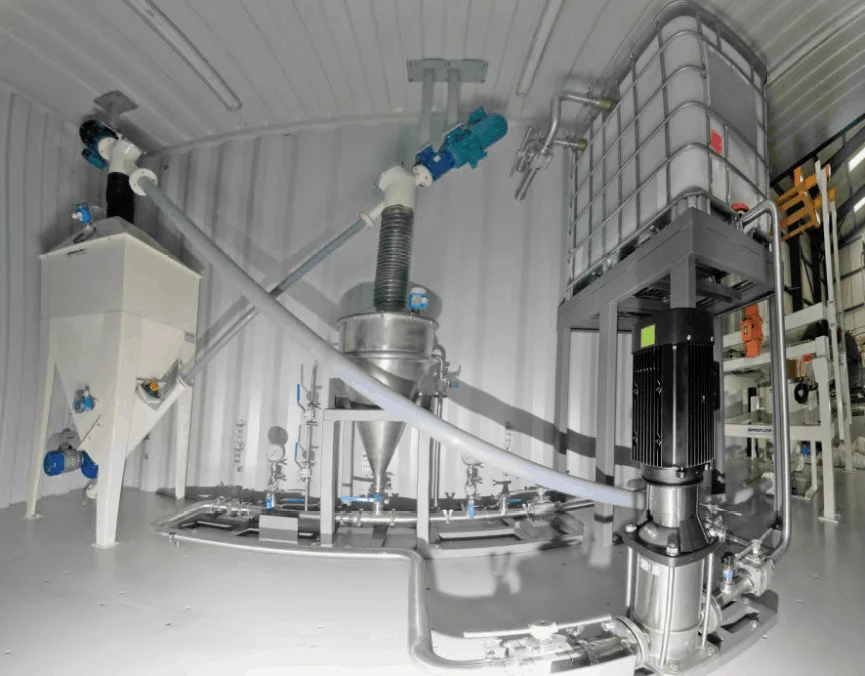
Problems With Flexible Screw Conveyors Caused During Installation or Setup
The first thing you should have in mind when thinking about challenges you could come into while working with these conveyor belts involves the installation and layout of the flexible screw conveyor.
If you’re not getting the results you expected with the conveyor belt solutions, the FSC setup could be the problem. This being said, here are some steps you can take to eliminate the issues with setup.
Inspect the Conveyor Tube
Take a look at the conveyor tube and ask yourself the following questions:
- Is the tube straight?
- If a bend is needed, is that bend within your manufacturer’s radius restrictions?
- Is the bend smooth and gradual – If the radius is too tight, the spiral will be under extreme stress and will eventually break. It can also cause excessive wear.
- Are the inlet and outlet housings in line with one another – This minimizes the degree of the bend required to fit the layout and eliminates undesirable “S” curves, which create extreme stress on a spiral. The double curve puts the spiral in a real bind as it rotates.
Inspect the Conveyor Supports
If you wonder why your spiral is breaking or why the tube is wearing out so quickly, the answer could be inadequate support. So, after inspecting the conveying tube, go over the supports. In this phase, you should ask yourself whether the conveyor tube is supported properly.
Supports should be placed every 6 – 8 feet (1.8m – 2.4m) under normal conditions. If you are conveying dense materials, supports should be closer together to keep the tube from sagging. As a guideline, supports should be rigid enough to support the weight of a full conveyor tube and to prevent the tube from swaying during operation.
Check the Drive Assembly Stability
Motor or drive assembly stability should also be examined if you’re having issues. Be sure to ask, “Is the drive assembly mounted rigidly?” If the drive assembly moves too much, the spiral, tube, and steel housing components could be stressed, which could lead to a system failure.
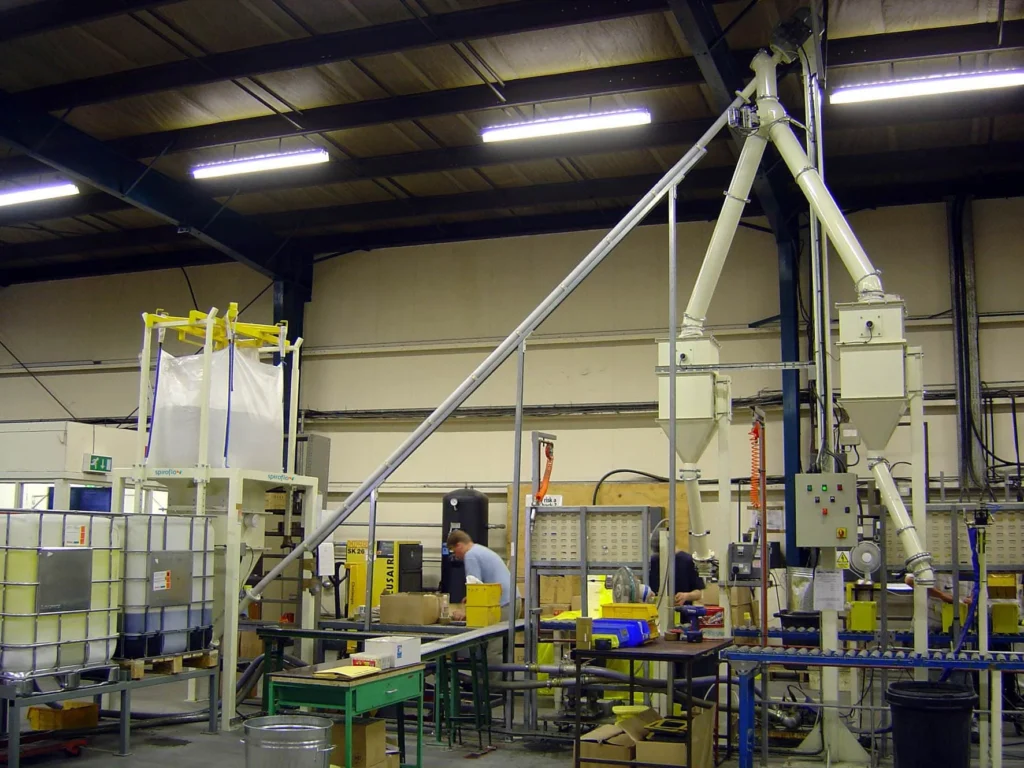
Check the Inlet Housing Setting
Another place to look if you’re encountering a flex screw failure is the inlet housing setting. Be sure to ask if the inlet housing is adjusted properly. Communicate closely with your manufacturer. Ask about design options and possible add-ons and how the inlet housing is set.
Account for Spiral Stretch
Spiral stretch can lead to broken spirals or motor overload. It’s important that the spiral has room to expand under load, or it could scrape the back of the inlet or restrictor cap and cause failure.
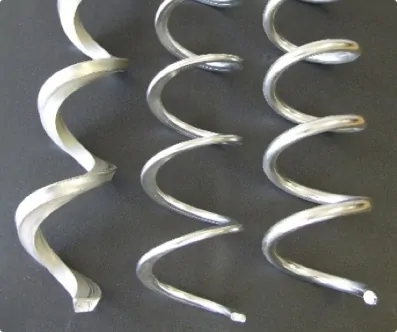
Why Won’t My Flex Screw Convey Material?
Users of these conveyor technologies may also ask. “Why won’t my material convey?” Here’s what to look out for in that case:
- Is the spiral turning in the right direction – If you’re standing at the inlet end and looking toward the outlet, the spiral should turn in a counter-clockwise direction. If you’re at the discharge end and looking toward the inlet, the spiral should be turning in a clockwise direction. The correct rotational direction depends on the type of helix, left hand or right hand. Spiroflow and most manufacturers use right-hand helixes.
- Is there adequate material in the hopper – Flexible screw conveyors will not completely empty out. Even if there is some material in the hopper, it may not convey without an adequate amount of “head” of material.
- Does your material rathole or bridge in the hopper – If so, you can utilize flow aids, such as an agitator, vibration, or bin aerators. Bin aerators are silicone or rubber discs inside the hopper that air is injected under from the outside. When air escapes from under the discs, they vibrate and aerate the material.
- Is the material fluidizing & falling back down in the tube – Very fine materials can react like water inside a flex screw, often called a flexible auger. The solution for this problem is a full-length center core. Center cores also lighten the load when moving very dense materials. Running at slower speeds can also be effective in fluidizing materials.
Check the Feed Restriction
Although a traditional conveyor belt system could seem like less hassle, it also has some potential challenges. But when it comes to FSCs, be sure to know whether the feed restriction is opened up enough to allow adequate material into the spiral. If there isn’t adequate material being fed into the conveyor, you may not attain your desired conveying rate.
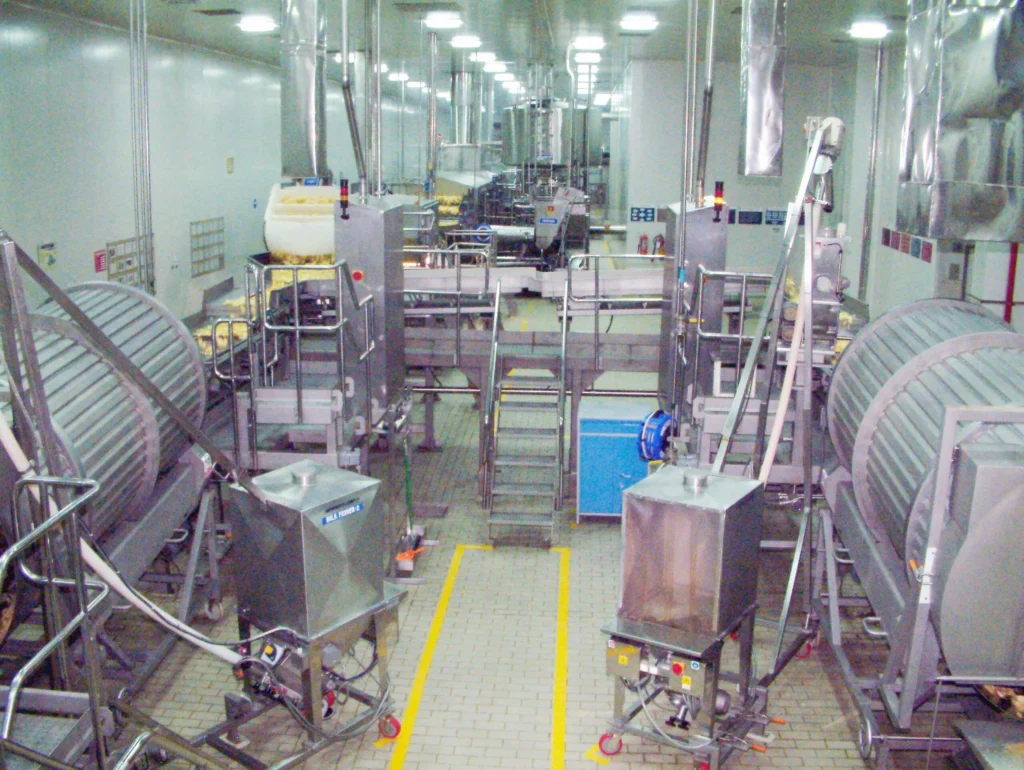
Why Is My Flexible Screw Conveyor Locking Up or Failing?
Jamming, stalling, or locking up are other common issues our service technicians hear about, and these problems can also be encountered in conveyor belt systems. Several things can cause this, and here’s what you need to know about them.
The Spiral Is Overloaded
The best way to check whether the spiral is overloaded is to ask yourself: Is the feed restrictor set properly? Overloading the conveyor can result in high amp draw or motor overload, motor damage, spiral damage, premature wear, etc.
The Material Isn’t Flexible Screw Friendly
Not all materials convey well in this type of conveyor. Cohesive materials or materials high in moisture can smear and cause the spiral to lock up. In some cases, a conveyor with a beveled spiral can convey those types of material. We always recommend having your material tested in a test lab so that you get the best type of conveyor for your application.
Check the Power Supply to the Motor
Lock out, tag out (LOTO) the conveyor, and try to turn the spiral by hand. If there is no obvious mechanical reason why the spiral will not turn, it could be an electrical issue. Check the controls to see if there has been a variable-frequency drive (VFD) fault or if a thermal overload has tripped out. Refer to the VFD manual to troubleshoot the error code produced by the VFD. If the thermal overload is tripped, rest it and try to source the cause of the overload.
Check Your Wiring
Check the wiring to the controls and to the motor itself. Also, check the voltage supplied to the motor. To do that, simply ask: Are you getting the proper voltage on all three phases supplied to the motor?
Check That You Have the Right Motor
Is the motor/drive assembly sized properly? It could be that you simply don’t have enough horsepower for the conveyor to work under full load. Refer to the motor’s nameplate for its full load amperage limits and check the motor’s amp draw while under full load. If there are no physical restrictions other than the material being conveyed and the motor draws high amps, it could be undersized.
Why Are My Tubes & Spirals Wearing Out So Quickly?
Another issue customers may have, which is not uncommon in belt conveyor systems, is excessive tube and spiral wear. While most customers are aware of the abrasive nature of their materials, not all fully understand why their tubes and spirals tend to fail frequently.
That’s why it’s always a prudent practice to have spare spirals and tubes on hand to minimize any process downtime, a tip that many experienced manufacturers advocate. To prevent potential equipment damage, here are some common causes of tube and spiral wear that belt conveyor manufacturers and users should be mindful of.
Abrasive Materials
Coarse sands, minerals, and sugar can be very harsh on tubes and spirals. Heavy-duty spirals are available, and, in extreme cases, double-wind spirals can be used. We often recommend stainless steel or rubber Rhinoveyor tubing as a more wear-resistant option over the standard UHMWPE tube.
An undersized screw can also be placed in a conveyor to reduce tube wear. This allows more clearance between the spiral and tube, allowing the material to act as a buffer between the two.
Tube Radius
The radius of the tube may be too tight. This can cause the spiral and tube in the arc area to wear out quicker than normal. As a general rule, you always want to keep the conveyor tube as straight as possible.
Heat
Heat can be a factor in tube life. A steel conveyor tube should be considered for materials hotter than 125-150˚F (51-65˚C). You should also consider the environment. Will the tube be subject to extreme ambient temperatures?
External Wear
Is the outside of the tube rubbing against anything? It is common for the flexible screw conveyor tube to move slightly during use. This constant swaying action could wear a hole from the outside if it is in contact with another object.
Spiral Fatigue
Spirals can become fatigued over time simply due to continuous use. Spiral fatigue is a phenomenon that occurs gradually as a result of continuous and prolonged usage of flexible screw conveyors. This wear and tear process is a natural consequence of the repeated bending and flexing that the spiral experiences while conveying materials.
Welds
Improper welding techniques can also have an adverse effect on the spirals, making them weaker. Welded spirals that are not assembled properly may cause the conveyor to be out of balance. This will cause excessive shaking and/or movement of the tube.
It will also cause premature tube failure and put the spiral under excessive stress. Extreme cases of poorly assembled spirals can cause damage to the inlet and outlet housings, too!
Prevent Problems and Ensure Smooth Operations With Professional Installation
To avoid any of the issues, especially with industrial conveyor systems, it’s best to invest in installation supervision from your supplier’s service department. It’s always a good idea to have an experienced technician on hand to assist with the setup and installation process.
If you are comfortable handling the installation with your in-house team, a reputable supplier should offer phone support during the installation. You may also wish to consider scheduling a startup and commissioning visit. What a good technician can see and correct during commissioning could save you thousands of dollars down the road. It also offers you in-depth onsite training, even for the traditional belt conveyor system.
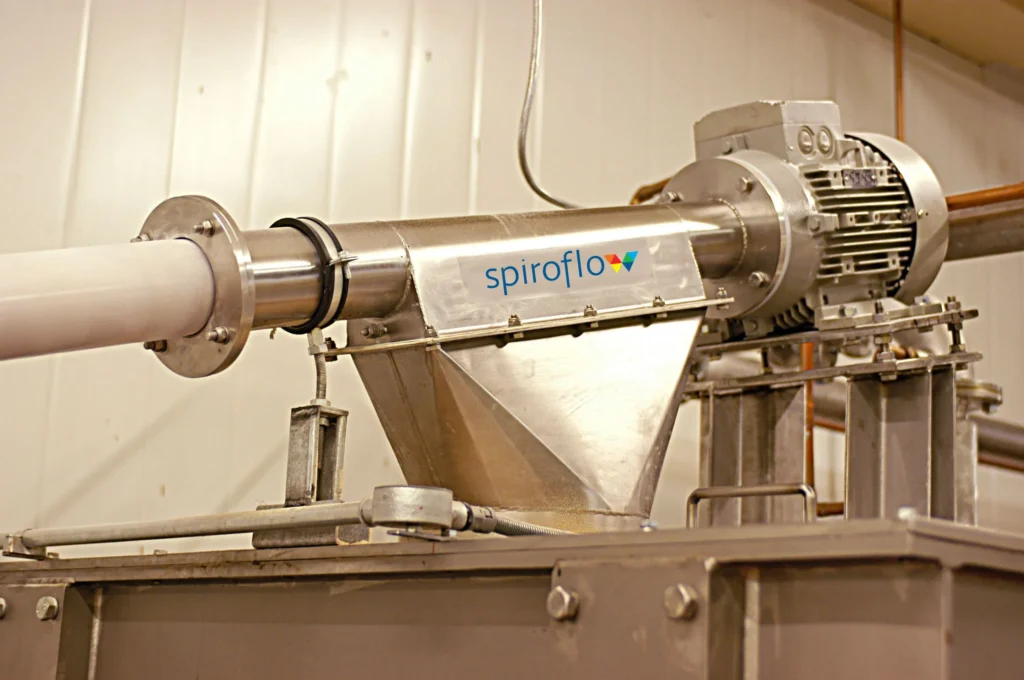
Get a Flexible Screw Conveyor From a Well-Known Industry Manufacturer
We all know a flexible screw conveyor is an important investment that you rely on in your process. At Spiroflow, we can pre-test your material in our test lab to make sure it’s suited for conveying with a flexible screw conveyor. We’re one of the most reputable conveyor systems manufacturers with an expert staff of service technicians who work closely with our customers to make sure everything operates as promised. We have solved flexible screw conveying challenges for customers around the world, so if you need some help or advice, don’t hesitate to contact us.