In a world increasingly conscious of its environmental footprint, innovative recycling initiatives are more crucial than ever. That’s why Spiroflow, one of the leading conveyor systems manufacturers, has partnered with Unifi Inc. Explore how Spiroflow helps recycle fabric waste & water bottles into fiber at Unifi in a groundbreaking project that turns the tide on fabric waste and used water bottles.
Spiroflow & Unifi Inc. – A Partnership Towards a Greener Tomorrow
In an era where sustainability is not just a goal but a necessity, our team at Spiroflow is making some significant moves. The recent collaboration with Unifi Inc., a titan in the production of polyester and nylon yarns, exemplifies a shared commitment to minimizing waste.
Together, Spiroflow and Unifi Inc. have embarked on an ambitious project with a clear mission – to transform waste materials, including recycled plastic water bottles, into premium recycled polyester fiber. At its core, this project aims to address numerous concerns associated with waste accumulation:
- Waste materials, especially plastics, contribute significantly to pollution, affecting land, waterways, and oceans,
- The production of new materials consumes finite natural resources, worsening resource depletion,
- The decomposition of waste in landfills releases methane, a potent greenhouse gas contributing to climate change.
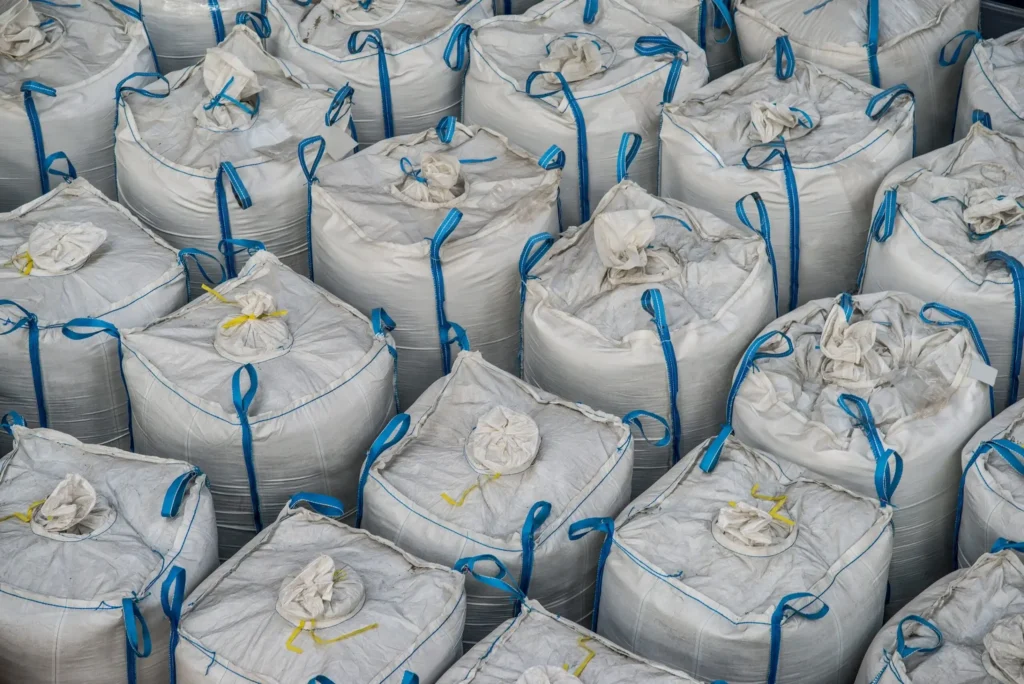
Introducing Repreve – High-Quality Eco-Friendly Fibers
Unifi Inc. has redefined sustainability through the creation of Repreve, an innovative recycled fiber derived from pre-consumer waste and recycled plastic water bottles. What sets Repreve apart from other similar materials is its exceptional versatility and ability to match, if not surpass, the quality of virgin fibers.
This groundbreaking material is transforming the sustainability landscape of consumer products, finding its way into a diverse range of items. This includes clothing, home furnishings, automotive interiors, and versatile tote bags. Repreve has become the fiber of choice for leading global brands such as Ford, The North Face, Patagonia, and Haggar, marking a significant shift towards more responsible manufacturing practices.
2010 Saw the Opening of a New Recycling Center in Yadkinville
Marking a milestone in sustainable innovation, 2010 witnessed the launch of Unifi’s new recycling center in Yadkinville, North Carolina. This facility was set up with a clear vision – to recycle a broad spectrum of materials efficiently in this area. Central to its operation were three pivotal requirements:
- Fill mixing silos with plastic flakes from gaylords and bulk bags,
- Re-circulate plastic flake material within each of the two silos and re-circulate material between these two silos,
- Deliver material to the next manufacturing process step.

Spiroflow Solution – How We’re Meeting Unifi’s Requirements
To fulfill Unifi’s specific requirements, our team at Spiroflow engineered a comprehensive material handling system. This system comprises a box dumper, two bulk bag dischargers, five flexible screw conveyor setups, four aeromechanical conveyor belts, and one custom control panel complete with an HMI (Human Machine Interface). Let’s take it step by step:
Filling Mixing Silos
The journey begins with the arrival of plastic flake materials, either nestled within gaylords or packed in bulk bags. They are placed in the custom-built box dumper, which empties plastic flake material into the live bottom bulk bag discharging system. Once freed from their confines, the plastic flakes are guided by twin flexible screw conveyors into a hopper. Here, a critical safety step unfolds, where material is passed through a metal detector where any metal particles are removed.
From the hopper, a third flexible screw conveyor takes charge, propelling the material upwards to a vertical aeromechanical conveyor. It’s here that the strategic brilliance of Spiroflow’s system shines, with a horizontal aeromechanical conveyor adeptly moving to fill either silo A or B, depending on the need. This configuration allows for efficient transfer of flake materials directly into the silos, marking the first step in the manufacturing process.
Re-Circulating Material
Once inside the silos, the flake material is transported with the help of two flexible screw conveyors strategically placed at the base of each silo to a vertical aeromechanical conveyor belt system. This vertical conveyor then elevates the materials to the pinnacle of the silos, where horizontal conveyor solutions now take the lead.
Depending on the specific requirements of the recycling process, this belt conveyor system has the flexibility to advance either forward, directing the flakes into silo A, or in reverse, to fill silo B. By allowing for this level of control and flexibility, this dynamic setup not only facilitates the seamless re-circulation of material within each silo but also between A and B.
Introducing the Next Manufacturing Step
The final leg of the plastic flakes’ journey through the recycling process involves their meticulous transition into the initial stages of manufacturing. This crucial phase is facilitated by the same two flexible screw conveyors located at the base of each silo.
From there, the journey continues as the material merges with fabric cut-waste, moving together towards the next phase of processing. This integration is pivotal, marking the point where recycled plastic flakes begin their transformation into new, sustainable products.
Innovative Solutions in Action – Spiroflow Is Leading the Way
Spiroflow’s rigorous testing has unequivocally proven the superior efficiency and performance of its innovative conveyor belt solutions in handling plastic flakes. These setups not only transport materials more efficiently and quickly than alternative methods but also significantly reduce energy consumption compared to pneumatic systems suggested by other vendors.
Mathias Lee, Vice President of Sales at Spiroflow Systems, highlights the critical role of testing in ensuring reliability and effectiveness: “Extensive material testing wasn’t required, but was important in verifying that our solution would operate as expected, at the rates we promised. We highly recommend material testing to all of our customers.”
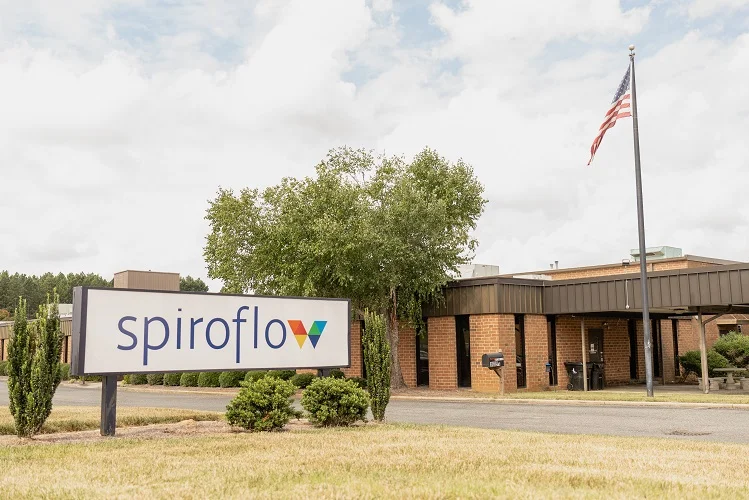
Discover Spiroflow’s Customized Solutions
Located in Monroe, NC, Spiroflow offers an extensive portfolio of material-handling solutions catering to both small and large-volume users. From simple conveyor technologies to supplying replacement parts for even the most complex setups, we offer a variety of processing systems and automated solutions. For more information, contact us and dive into the world of innovative material handling, where sustainability meets efficiency.