Choosing the right conveyor belt system for your food application can be a tiresome task for a buyer who doesn’t know about the key factors that should be considered. These simple tips to consider when purchasing a food conveyor can be seen as guidance and a good starting point. Probably the most critical aspects to consider and include are testing, product analysis, degradation, cohesiveness, and maintaining a blend.
#1 – Understanding the Product
Finding the right conveyor manufacturers with a full materials testing lab and machinery test facilities is essential. These facilities should include a full selection of conveyor belt systems in addition to bulk bag fillers and unloaders. The right testing facility should provide wide-ranging scientific product evaluation of the bulk densities and particle sizes of powders or bulk solids.
It’s challenging to convey if your product is labeled as “difficult to handle,” sticky, friable, hygroscopic, or tends to cake or pack. In this case, lab tests are therefore essential to help understand how the product behaves. After lab tests, comprehensive machine trials will give a full understanding of the product to be conveyed, thereby avoiding any potential future issues when choosing the right conveyor.
#2 – Understanding the Area and Layout
Understanding requirements for installation and the conveying route is critical – for example, does the equipment need to be installed on a second floor, go through walls, or round bends? Identifying any possible hazards in the conveying area, such as ATEX zones, FLT traffic, operator safety, equipment barrier requirements, and more, is essential.
It is also important to have an awareness of the area’s environment, meaning – what is the ambient temperature, does it change seasonally, as this can affect the equipment if it’s really hot and humid in the summer, cold in winter, for example, or is humidity/sea air a consideration which could influence corrosion. Asking questions about cleaning, following up on maintenance, and thinking ahead on plans is also advisable. Plus, having a good old-fashioned walk-around is always the best place to start!
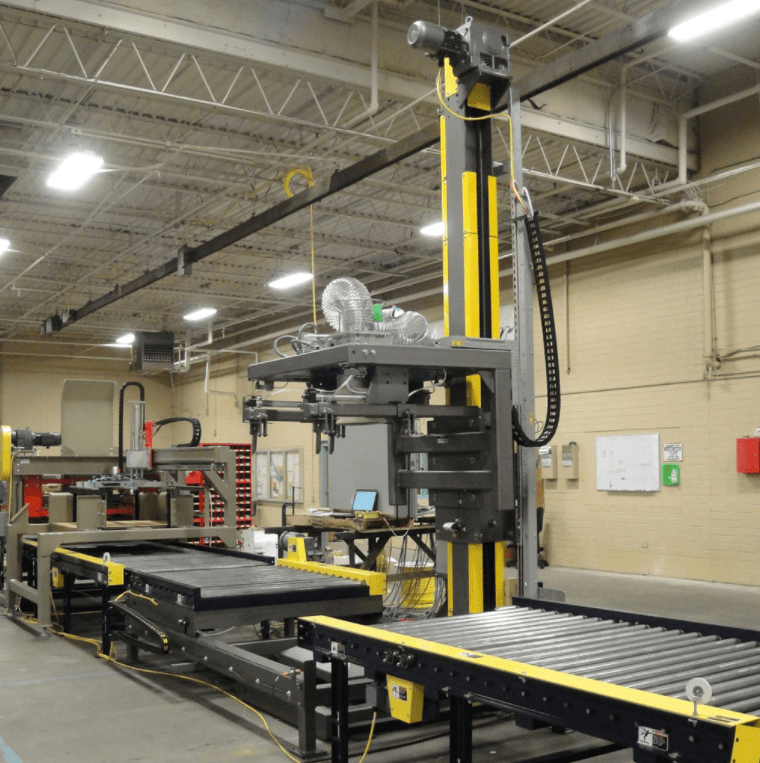
#3 – Key Objectives
It sounds obvious, but identifying the key objectives of the process is an important factor to consider when selecting a conveyor. Maintaining the blend, increasing throughput, reducing degradation, improving efficiency, or reducing manual handling could be driving factors influencing the choice. For example, if the conveyor needs to minimize degradation on a fragile product, then a gentle conveyor such as a Cablevey tubular drag conveyor would be a better choice over the spiral of the flexible screw conveyor. Or if the conveyor needs to maintain a mixing blend, then the rotating spiral of the flexible screw conveyor or aero-mechanical conveyor is a great choice.
#4 – Hygiene and Safety Requirements
A crucial deciding factor in choosing a conveyor is the hygiene specification. With food applications requiring the highest hygiene standards and dust-free operations, especially if they operate in an ATEX environment, choosing a conveyor that meets these needs is vital. The simplicity of cleaning a flexible screw conveyor, for example, with its drop-out tray and reversible bung, makes it ideal for many food applications. Furthermore, because air isn’t used as a conveying medium in the FSC, there’s no danger of dust contamination or humidity. Similarly, an aero-mechanical conveyor or pneumatic conveyor is an excellent conveyor choice, as it offers near-total transfer capability, which means it requires minimal cleaning.

#5 – Installation Speed or Mobile Requirements
For applications that need results quickly, a mobile conveying solution might be the best option for a shorter lead time. Aero mechanical conveyors and flexible screw conveyors can readily be mounted on wheeled frames, complete with integral controls and a power connection fly lead. This enables the use of a single conveyor to support multiple processes or the removal of the conveyor for cleaning and washing at a distance. Optional height adjustments on mobile units may also be a consideration if they have to pass under low doorways or if they discharge at differing heights. Mobile conveyor solutions offer versatility for those applications that do not have the time to wait for a longer lead time or prolonged installation times. Plug and play is the name of the game here.
#6 – Consider the Costs
As always, cost is a pivotal factor when selecting a belt conveyor system for your process and depends largely on several variables, many of which will have been identified by following the above guidance. However, it is worth mentioning that when comparing mechanical industrial conveyor systems, the simplest and least expensive solution available is a flexible screw conveyor, which consists of a revolving stainless steel spiral housed inside a food-grade UHMWPE tube.
If cost is a deciding factor, it is even more important to select a supplier who will still achieve your objectives and give value. Buying off cost alone can be fraught with danger. It is impossible to pay a little and get a lot, as it simply can’t be done. Going with the lowest bidder offers great risk, as frequently, the conveyors purchased at the lowest price are not fit for purpose.
Mind These Tips to Consider When Purchasing a Food Conveyor and Contact the Best Conveyor Systems Manufacturers
Selecting the right conveyor belt solutions for your food application involves more than just considering the cost. It requires a holistic approach that addresses various factors such as product characteristics, installation area, process objectives, hygiene and safety requirements, installation speed, and mobility needs. Remember, the cheapest option may not always be the best in the long run. Prioritize quality, functionality, and a reputable supplier who understands your specific needs.
For expert advice and a range of solutions tailored to your unique requirements, don’t hesitate to reach out to a company that is among the leading belt conveyor manufacturers – Spiroflow. We can provide you with the insights and options you need to make an informed decision. Contact us today to discuss the conveyor technologies requirements and take the first step towards optimizing your food processing operations.