Selecting a mechanical conveyor for material handling solutions will depend on the specific requirements of the end user. Points to consider are safety, energy consumption, prevention of contamination, dust containment, and minimal degrading of the product. The budget and return on investment will determine the level of sophistication and the suitability of a particular conveyor to meet the application.
Selecting a Mechanical Conveyor – Defining Your System Specifications
During the conveyor selection process, preparing a comprehensive specification is essential. This document is critical in ensuring the chosen conveyor meets the diverse needs across industries.
It outlines the specific requirements and limitations the conveyor system must adhere to, ensuring a perfect fit for your material handling needs. When crafting your specification, consider these key factors:
- Material characteristics – the nature of the materials being handled, including their size, shape, and any special handling requirements.
- Conveying capacity – how much material the system needs to move within a given timeframe.
- Construction materials – the types of materials used in the conveyor’s construction can impact its durability and suitability for certain environments.
- Dimensional constraints – the available space for the conveying system, including length, width, height, and the layout of the surrounding area.
- Environmental and product hazards – any potential risks associated with the materials being conveyed or the environment in which the conveying system will operate.
Choosing the Right Conveyor Supplier
Specialist suppliers in the field of material handling offer a variety of conveyor types and options, each designed to transport a range of materials efficiently. To ensure the equipment fits your specific needs, testing raw materials with the selected conveyor system is crucial. This step verifies both the conveying rate and the equipment’s compatibility with your materials.
Tailoring Conveyor Solutions to Your Needs
When selecting a material handling supplier, prioritize those with proven experience with your products and the expertise to customize their equipment to your requirements. Such customization often involves engineered solutions, complete with layout drawings and custom-designed parts to fit your system and application perfectly.
Experienced vendors and conveyor manufacturers excel in adapting their equipment to various scenarios, offering modular components to meet your needs. Spiroflow can provide comprehensive solutions for moving products between processes, featuring a range of conveyors and systems for high containment.
Their capabilities include handling everything from silo/hopper unloading and process links to container filling and ingredient mixing. Spiroflow will also ensure seamless integration and operation within your material handling framework.
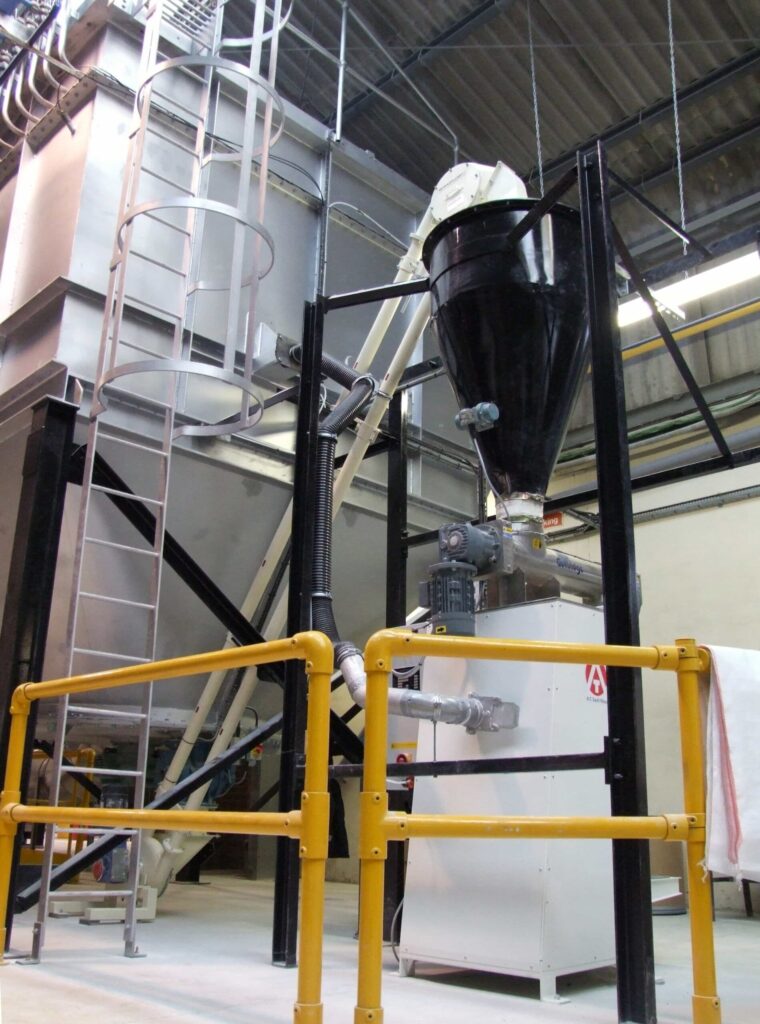
Explore Different Mechanical Conveyor Options
When faced with the choice, there are several types of mechanical conveyors available, each offering unique benefits. Considering the value and functionality of each type is crucial in making an informed decision. Let’s go through them:
Flexible Screw Conveyors
Flexible Screw Conveyors (FSCs) are an excellent choice for those seeking dust-free, energy-efficient, low-maintenance, and cost-effective conveying solutions. A flexible screw conveyor excels in gently handling materials and continuously mixing contents, ensuring a uniform mix.
This mixing action is particularly beneficial for pre-mixed ingredients, ensuring a consistent blend before reaching packaging or processing machines. The size, screw type, and speed of FSCs are tailored during the testing phase to meet specific needs.
Aero Mechanical Conveyors
Aero mechanical conveyors (AMCs) provide high conveying capacities and a total batch transfer. The enclosed tubular system creates a pathway for the driven rope and disc assembly to navigate the circuit. This design results in a gentle conveying action, ensuring reliable material transport between processes.
Tubular Drag Conveyors
Tubular drag conveyors offer a sophisticated solution, featuring a series of straight and curved tubes that create a fully enclosed system. Unlike the previous two, they support intricate circuits with multiple entry and exit points. This design doesn’t rely on air to move materials but uses discs along a cable to transport items gently.
Although they operate at a slower speed, their design allows for a complete batch transfer. This makes them suitable for complex applications where material integrity is paramount. The operating speed is carefully calibrated based on the system’s layout and the total length of the circuit, balancing gentle handling with operational efficiency.
Optimize Post-Processing With Advanced Container Filling Solutions
Container filling plays a crucial role in material handling, specifically when transferring materials to offsite locations after processing. A variety of low-cost container options are available for this purpose, including bulk bags, cardboard totes, drums, and sacks.
Custom filling systems are designed to accommodate these containers, offering different levels of automation and complexity to match various budgetary constraints. Typically, a larger investment allows for more automated processes, leading to greater operational efficiencies.
Modern filling machines boast programmable controllers that enhance filling accuracy and optimize cycle speeds. They feature automatic gain-in-weight adjustments, capable of compensating for weight variations within a tight margin of +/- 1%.
This precision is particularly beneficial for companies aiming for NTEP approval. Additionally, these systems offer a range of customizable features, ensuring they can be tailored to meet the needs of various containers and applications. This adaptability makes them an invaluable asset in streamlining the post-processing phase.
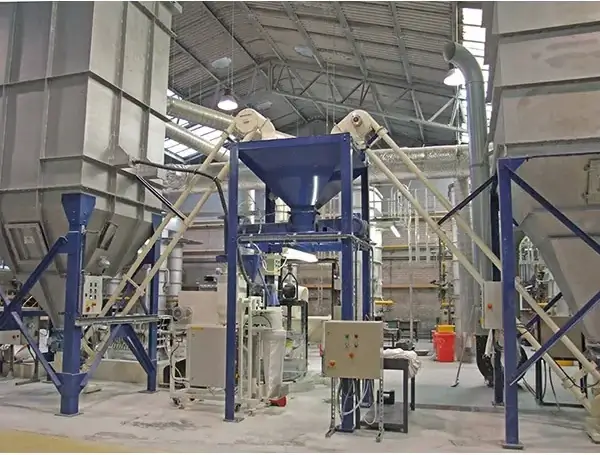
Streamline Your Operations With Spiroflow Conveyor Solutions
Whether your needs align with flexible screw, aero mechanical, or sophisticated tubular drag conveyor systems, Spiroflow has the technology to enhance your operation’s efficiency. Leverage our comprehensive conveyor belt solutions and container-filling systems for seamless material handling. Ready to transform your processes? Contact Spiroflow to explore our conveyor technologies and find the perfect fit for your needs. Join us in driving innovation and efficiency in your industry today.