Dealing with structural drag chain conveyor problems can be a headache for any operation. They are a considerable investment to any organization, and you want to make sure you’re getting your money’s worth. To make matters worse, most issues with this conveyor belt system are completely avoidable. With over 45 years in the industry, Spiroflow is here to provide valuable insights into maintaining these powerful systems for peak performance.
Understanding Structural Drag Chain Conveyors
Let’s briefly delve into what makes structural drag chain conveyors unique and indispensable. These conveyor belt systems are constructed from schedule 40 pipe and move material with an ultra-heavy-duty chain and disc assembly.
Unlike tubular drag chain conveyor belts, structural drag chains are capable of handling a wider variety of materials, offering a versatile solution for even the most challenging conveying applications. Here are some notable advantages of integrating this system into your production line:
- Moves materials smoothly and continuously, optimizing production flow,
- Capable of transporting a wide range of bulk materials, from dry and fragile to moist and cohesive,
- Optimized design requires less power, even when extending to longer distances or higher capacities.
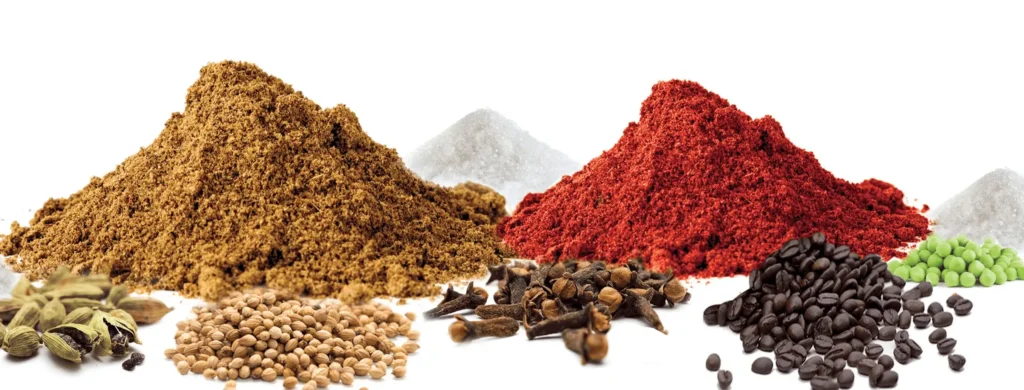
What Are the Most Common Structural Drag Chain Conveyor Problems?
Structural drag chain conveyors are renowned for their efficiency and versatility. However, no conveyor is immune to the need for regular maintenance and operating challenges. This not only disrupts your workload but also consumes valuable time that could have been used more productively, turning into a real conveying nightmare.
Such situations highlight the importance of preventive maintenance and being prepared for the following common issues that might arise:
Wear and Tear on Conveyor Housing
Structural drag chain conveyors are built to last a long time, and this is the main reason behind their hefty pricing. However, over time, the constant movement of materials can lead to wear and tear on the housing. This deterioration not only affects the conveyor’s efficiency but can also lead to material leakage, posing cleanliness and safety risks. It’s best to make it a point to check the conveyor’s housings for wear every month.
Chain and Disc Maintenance
The chain and disc assembly is the heart of the structural drag chain conveyor, responsible for the smooth transportation of materials. However, without proper care, the chain can stretch, and discs can wear down or break, leading to disruptions in material flow and potential downtime. Implementing a routine maintenance schedule can help here, identifying and rectifying these issues before they escalate.
Material Buildup and Blockages
Certain materials, especially those that are moist, sticky, or very fine, can accumulate within this belt conveyor system, leading to blockages or inefficient material flow. Regular cleaning and choosing the right type of conveyor solutions for specific materials are crucial for mitigating these challenges.
Making Informed Decisions for Smooth Operation
Neglecting regular maintenance can lead to plenty of troubles down the road. However, it’s equally as important to make an informed choice and integrate the right conveyor belt solutions into your operation in the first place.
Structural drag chain conveyors can operate in up to three planes, creating a Z-formation, but keep in mind that with each added bend, an increase in horsepower is required. Most of the time, simple layouts are best, but it all comes down to your specific requirements.
Choosing the Right Disc Is Equally as Important
Besides choosing the conveyor itself, implementing the correct disc can also prevent issues in the future. This piece must be able to withstand possible chemical attack, abrasion, temperature, and more. There are plenty of options to choose from:
- Ultra High Molecular Weight Polyethylene (UHMWPE) discs – one of the most popular choices, this material has extremely high abrasion resistance, low coefficient of friction, high impact strength, and long service life, handling temperatures up to 176°F (80°C),
- Cast iron discs – offer cost-effectiveness and a reasonable service life, making them ideal for applications where corrosion, abrasion resistance, chemical attack, and product contamination are not primary concerns,
- Mild steel discs – can be used as an alternative and coated for added resistance to corrosion or wear, handling temperatures up to 420˚F (216˚C).
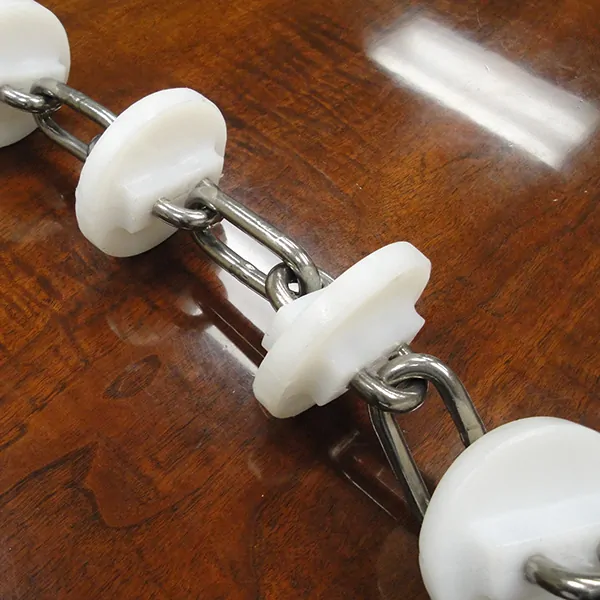
Is a Structural Drag Chain Conveyor a Good Fit?
Designing the ideal conveyor setup and choosing the right components can be complex. In this endeavor, consulting with experts stands out as a wise course of action. To help you make an informed decision, here are the most important aspects that will help you understand if a structural drag chain conveyor is a good fit for your organization:
Speed, Capacity, and Length
Structural drag chain conveyors can run at speeds up to 50 ft/min (15 m/min) with a capacity of up to 10 ft³/min (0.28 m³/min). A conveyor’s maximum total length is up to 400 ft (120 m). On top of that, multiple industrial conveyor systems can be linked together.
Conveyable Material
The structural drag chain conveyor is considered to be an ultra-heavy-duty piece of equipment. With that label, it means this solution can handle almost any type of bulk material. Dry, fragile, abrasive, hygroscopic, moist, cohesive, sludge – you name it. It’s worth mentioning that these conveyor technologies also leave behind a low amount of residual material.
Dust Control
Designed to be mechanically dust-tight, these conveyors operate within an enclosed loop system. This eliminates the need for additional dust control measures and ensures minimal material residue is left behind.
Remember to Use a Test Lab
A trustworthy supplier will suggest running a material test before your design is finalized. That’s the only way to know for sure that your material will run in your application. Spiroflow offers this service in both the United States and the United Kingdom, facilitating the fine-tuning of your application before finalizing the design.
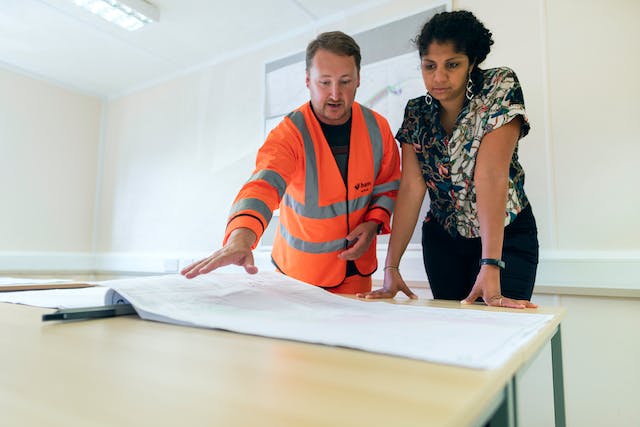
Our Team at Spiroflow Is Here to Help
Each processing need is unique, and choosing the right setup can be a real head-scratcher. But you don’t have to sort these details out on your own. Our experts at Spiroflow are happy to help with any questions you might have, as well as assist you with broader mechanical conveying, bulk bag filling and discharging, or control systems integration needs. Contact us for tailored advice and support.