We have been setting up processors with flexible screw conveyors for more than four decades, so our team is often asked about how these conveyors compare to other mechanical conveyors. That’s why we’ll analyze flexible screw conveyors vs other mechanical conveyors differences.
It’s common to hear flexible screw conveyors called different names. We’ve heard them all. If you call them auger screws, screw augers, flexible augers, screw conveyors, flex conveyors, helix or helical conveyors, flexible spiral conveyors, or spiral screw conveyors, we’ll know what you’re talking about.
Flexible Screw Conveyors – How They Compare
Flexible screw conveyors earn their name. These machines can convey material in any direction, from horizontal to vertical. These conveyors can be routed around fixed objects and from room to room. They are often used to feed filling machinery and to convey products from a hopper to a process. They are also used to provide controlled feeding and dosing from bulk bags, to feed products from multiple inlets, load silos, or fill bulk bags.
Benefits of Flexible Screw Conveyors
Flex screw conveyors offer users low-cost, low-maintenance, dust-free, and low-energy conveying solutions. These conveyor belt solutions can have multiple inlets and outlets. Interestingly, screw conveyors offer the added benefit of constantly remixing blends. A spiral or screw rotates within a sealed tube. The speed and helical action of the screw induces rotation of the product inside the conveyor in tandem with the screw’s movement. This rotation results in a tumbling motion, ensuring an even distribution of particles throughout the conveyor – a vital factor for consistently feeding pre-mixed ingredients. Spiral speed is typically up to 1,150 RPM depending on the size of the conveyor, and capacities are typically up to 29 ft3/min (0.82 m3/min). The conveying rate can vary.
Materials Best Moved With Flexible Screw Conveyors
Explore the unique advantages and limitations of flexible screw conveyors. It is a dynamic and versatile solution in material handling, designed to cater to a wide range of materials and conditions:
- Flexible screw conveyors are able to transport everything from fine powders to large pellets.
- Material degradation is less than what might be expected compared to other mechanical industrial conveyor systems.
- Moist materials, sludge, and slurries are not suitable for flex screws.
- They can transport hot and cold materials.
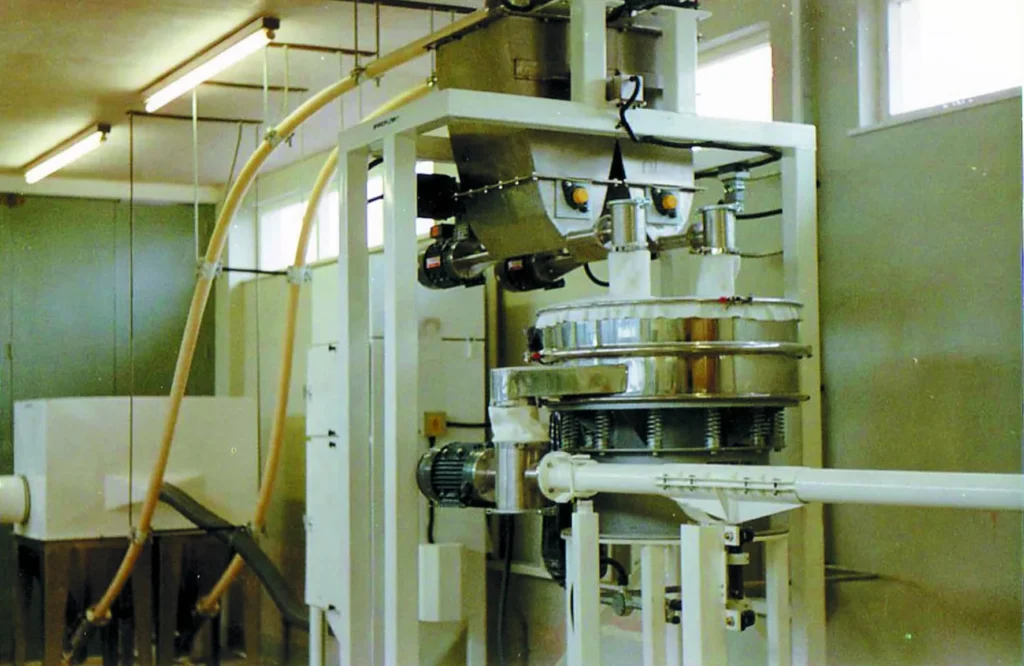
Aero Mechanical Conveyors – How They Compare
The cable and disc assembly inside an aero mechanical conveyor moves at a high speed, and the movement creates an air stream running at the same velocity. The material is fed into the airstream, where it’s fluidized and conveyed to the outlet(s) where it’s centrifugally ejected. The entire system is dust-free.
Benefits of Aero Mechanical Conveyors
An aero mechanical conveyor has a high conveying capacity and provides total batch transfer. Like a flexible screw conveyor, an aero mechanical conveyor is a totally enclosed tubular system. The tubing provides a path for the driven cable and disc assembly to move around a circuit. These conveyors can operate at any angle with multiple inlets and outlets. They offer a reliable means of transporting material between processes and can be designed as mobile units. Aero mechanical conveyor speeds can reach up to 1,200 ft/min (366 m/min) with capacities typically up to 36 ft3/min (1 m3/min). They do not operate at variable conveying rates.
Materials Best Moved With Aero Mechanical Conveyors
Learn about the key features and application considerations of aero mechanical conveyors, engineered to handle a diverse array of materials efficiently:
- The design of an aero mechanical conveyor allows the machine to convey a wide variety of materials.
- Successful conveying of fragile, abrasive, hygroscopic, and fine particles is application-dependent. That’s why we recommend material testing them first.
- Hot materials with temperatures over 300˚F (149˚C) and sludge-like materials are not recommended for these conveyors.
Benefits of Tubular Drag Conveyors
Tubular drag conveyor technologies can operate with a chain and disc assembly or a cable and disc assembly. They are made of a sequence of straight and curved tubes that totally enclose the dust-tight system. This allows for gentle conveying of the material inside. It can operate in three planes, which eliminates transfer points. They can have multiple inlets and outlets. The conveyor only needs one drive.
A cable drag conveyor’s speed is typically up to 140 ft/min (43 m/min), and its capacity is typically around 11 ft3/min (0.31m3/min). A chain drag conveyor’s speed is up to 100 ft/min (30 m/min), and its capacity is usually around 6.2 ft3/min (0.18 m3/min). Structural ultra-heavy-duty conveyor belt systems can reach speeds up to 50 ft/min (15 m/min). Variable conveying rates are possible.
Materials Best Moved With Tubular Drag Conveyors
Tubular drag conveyors are designed to move a variety of bulk materials. Whether it’s a chain and disc assembly or a cable and disc assembly will affect what materials can be conveyed.
Non-Structural Medium-Duty Cable and Heavy-Duty Chain Drag Conveyors vs. Structural Ultra-Heavy-Duty Chain Drag Conveyors
This table provides a clear comparison of the capabilities and suitability of each conveyor type for different materials and conditions.
Feature | Non-structural Medium-duty Cable and Heavy-duty Chain Drag Conveyors | Structural Ultra-heavy-duty Chain Drag Conveyors |
Material Blending and Handling | Both chain and cable conveyors maintain blends and move dry, fragile products well | Not specified |
Abrasive Materials | Best with chain drag conveyors, not suitable for cable drag conveyors | Not specified |
Hygroscopic Materials | Should be avoided with cable drag conveyors, can work with chain conveyors but testing recommended | Not specified |
Moist Materials | Work well with both, chain drag conveyors tend to be more effective | Not specified |
Material and Temperature Handling | Not specified | Handles any material and temperatures up to 482˚F (250˚C) |
Disc Material | Not specified | Discs made from various materials including steel and cast iron, other conveyors typically use UHMW discs |
Slurry and Fine Particles | Not specified | Can work with slurry and fine particles, but testing is suggested |
Do I Need to Use a Test Lab?
I referenced testing a conveyor belt system with your material a few times in this post, but I haven’t mentioned how you do that. Here at Spiroflow, we have test labs in North America and the UK. We highly recommend testing your product in your desired belt conveyor system. This is the best way we can guarantee the final product. If you’re interested in a free consultation, let us know!
Flexible Screw Conveyors vs. Other Mechanical Conveyors
Flexible screw conveyors offer a distinctive advantage over other mechanical conveyor technologies in terms of handling a diverse range of materials, from fine powders to large pellets. They excel in maintaining product integrity with minimal material degradation, a key consideration for handling fragile products.
For a comprehensive understanding of how flexible screw conveyors can meet your specific material handling needs, or to explore other conveyor options that might better suit your application, contact Spiroflow. Our experts are ready to provide tailored advice and solutions, ensuring you choose the right equipment for your operations.By the way, we don’t just manufacture conveyor solutions – we also perform control systems integration. Click here to see our entire line of products.